As tech-sector turbulence continues to dominate headlines, a quieter but equally important transformation is taking place across America’s blue-collar industries. In 2025, skilled labor sectors like construction and manufacturing are showing remarkable resilience and sustained job demand, with job demand steady in 2025 emerging as vital pillars of the national economy.
Amid concerns over AI-driven job losses, offshore outsourcing, and economic uncertainty, these hands-on careers are proving to be stable, rewarding, and increasingly attractive to a broad range of job seekers.
In this context, the job demand steady in 2025 highlights the importance of these roles for both economic stability and workforce development.
Understanding how job demand steady in 2025 can shape industry trends is crucial for prospective job seekers.
The consistent job demand steady in 2025 underscores the resilience of the construction industry amid evolving economic landscapes.
As investments pour in, the job demand steady in 2025 is likely to remain a focal point for analysts and policymakers alike.
Construction Industry: Building the Future, One Hire at a Time
The U.S. construction industry is booming, and it’s not just due to population growth or urban sprawl. A renewed national commitment to infrastructure renewal is reshaping everything from roads to renewable energy sites.
Since the launch of the Infrastructure Investment and Jobs Act (IIJA), over $1.2 trillion has been allocated to transportation, broadband, water systems, and energy projects. This long-term investment is creating millions of job opportunities, particularly for workers in skilled trades.
Among the fastest-growing roles:
- Electricians to install grid-connected smart systems
- Heavy equipment operators for transportation projects
- Carpenters and concrete workers for commercial builds
- HVAC specialists to retrofit aging public buildings with energy-efficient systems
“We’ve had job openings go unfilled for months. There’s more work than we can handle,” says Sheila Watkins, a hiring manager at a major general contracting firm in Colorado. “We’ve increased wages, offered sign-on bonuses, and are still struggling to keep up with demand.”
In 2025, construction companies are also expanding their diversity outreach, seeking more women, veterans, and minorities to close workforce gaps. This inclusive hiring trend is helping to reshape the image of construction work from “gritty and manual” to modern, skilled, and future-ready.

Manufacturing: A Sector Reinventing Itself
This transformation contributes to the narrative of job demand steady in 2025, showcasing a shift towards higher-skilled roles.
The rising job demand steady in 2025 reflects a broader trend of innovation within the manufacturing sector.
Manufacturing in the U.S. has come a long way from its Rust Belt-era image. Today, it’s a high-tech industry powered by robotics, AI, and precision engineering, with demand rising in strategic sectors like:
- Electric vehicle (EV) assembly
- Semiconductor fabrication
- Aerospace and defense systems
- Medical equipment and PPE production
Factories aren’t shutting down—they’re reshoring, thanks to global supply chain recalibration and geopolitical shifts.
“We’re not just making things—we’re making smarter things, faster,” explains Bryan Lee, operations director at a chip manufacturing plant in Arizona. “From smart factories to digital twins, U.S. manufacturing is redefining how things get built.”
Skilled roles in demand include:
- CNC machinists and mill operators
- Quality assurance inspectors
- Industrial maintenance technicians
- PLC programmers and robotics integrators
These jobs now pay between $55,000 and $90,000 annually, often with benefits and overtime. What’s more, they offer real career ladders, with many line workers moving into supervisory or engineering roles over time.
The Talent Shortage: A Double-Edged Sword
While job opportunities abound, there’s a major challenge: a shortage of qualified workers. According to the National Association of Manufacturers (NAM), nearly 2.1 million manufacturing jobs could go unfilled by 2030 if current trends continue. In construction, the Associated General Contractors of America (AGC) reports that 89% of firms struggle to find craft workers.
This shortage is driven by:
- Retirements of experienced baby boomers
- Perception gaps among younger job seekers
- Lack of vocational education in high schools
- Urban-rural mismatches in job availability
To counteract this, employers and governments are investing in training programs, scholarships, and partnerships with community colleges.
“We’ve partnered with local school districts to introduce construction and manufacturing courses at the high school level,” notes Tina Alvarez, a workforce strategist in Ohio. “When students see that they can earn $70,000 by age 25 without college debt, they start paying attention.”
As job demand steady in 2025 continues to grow, manufacturers must adapt to remain competitive.
No Degree, No Debt—Just a Career
One of the most compelling advantages of these sectors is their low barrier to entry. Unlike tech or finance roles that demand expensive degrees, most skilled trade careers require:
- High school diploma or GED
- Vocational training or community college certificate
- On-the-job learning via apprenticeships
Many companies provide paid training, covering costs of certifications and safety equipment. In many states, pre-apprenticeship programs help underrepresented groups prepare for full apprenticeships.
Programs worth noting include:
- SkillBridge for transitioning military personnel
- Registered Apprenticeships sponsored by unions and employers
- Women in Construction Week and MFG Day outreach events
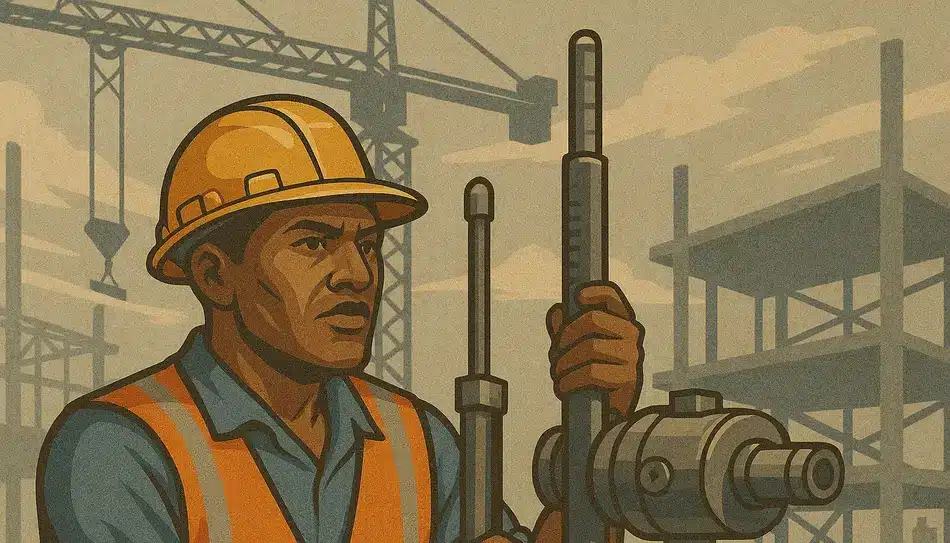
The Role of Technology: Friend or Foe?
While AI and automation are changing how work is done, they’re not replacing workers—they’re empowering them.
In construction:
- Drones are used for surveying and safety inspections
- 3D printing helps prototype modular building parts
- AI-driven software streamlines project timelines
In manufacturing:
- Robots handle repetitive or dangerous tasks
- Smart sensors monitor machinery for preventive maintenance
- Augmented reality is used for real-time training and diagnostics
These innovations are creating new hybrid roles that blend physical skills with tech know-how. Workers are increasingly called “technicians” or “specialists” rather than just “laborers.”
“The machines may assist us, but human judgment still drives decisions,” says Andre Porter, a quality control supervisor in Detroit. “You can’t replace instinct, experience, or accountability.”
Long-Term Outlook: Stability with Strong Earning Potential
With retirements accelerating and demand rising, construction and manufacturing are poised for sustained growth. According to the BLS:
- Construction job growth is projected at 4% through 2033
- Manufacturing employment is expected to increase 3%
- Combined, they’ll account for millions of job openings annually
Wages are competitive. With overtime and union benefits, tradespeople in high-demand specialties often earn six figures. Many also enjoy:
- Flexible schedules
- Retirement plans
- Paid family leave
- Travel opportunities for national projects
Suggested Internal and External Links
Internal
- Explore Skilled Trade Jobs at WhatJobs
- Construction Jobs Hiring Now
- U.S. Manufacturing Careers
External
- Bureau of Labor Statistics: Industry Outlook
- National Association of Manufacturers
- AGC of America Workforce Data
Skilled Trades: The Unsung Backbone of American Growth
In a digital-first world, skilled labor remains the engine behind physical progress. From rebuilding bridges to crafting precision tools, these sectors play a critical role in America’s economic health.
For young people reconsidering the traditional college route, mid-career workers seeking new purpose, or veterans transitioning into civilian roles—construction and manufacturing offer pathways to pride, purpose, and prosperity.
Discover your next career move, Visit WhatJobs News to explore skilled labor opportunities across the U.S.
Frequently Asked Questions
What jobs are most in demand in the U.S. construction sector in 2025?
Electricians, plumbers, carpenters, HVAC technicians, and heavy equipment operators are in high demand due to infrastructure funding and housing growth. Projects tied to energy efficiency and green building are creating new roles. Employers are expanding apprenticeship programs and offering higher wages to address persistent labor shortages across both commercial and residential construction.
How is technology changing manufacturing jobs in 2025?
Technology is enhancing—not replacing—manufacturing jobs. Robotics, automation, and AI improve productivity, but they also require skilled human oversight. Workers trained in programming, maintenance, and system diagnostics are increasingly valuable. Many roles now blend hands-on expertise with digital tools, and employers are offering upskilling programs to support the shift toward high-tech, precision-based production environments.
Can you advance in these careers without a college degree?
Yes. Most skilled trades offer clear career paths starting with apprenticeships or vocational training. With experience and certifications, workers can progress into supervisory, technical, or management roles. Many tradespeople earn strong incomes and benefits—often exceeding white-collar peers—without taking on student debt. Employer-funded development programs make long-term growth achievable from day one.
Why is there a skilled labor shortage, and what’s being done about it?
Aging workers, fewer vocational programs, and outdated trade stereotypes have caused a skilled labor shortage. In response, companies are raising pay, improving job benefits, and promoting trade careers through school partnerships and media campaigns. Government-backed training and fast-track apprenticeships are also helping rebuild the talent pipeline for construction and manufacturing roles.