Reshoring U.S. manufacturing 2025 marks a turning point for the American industrial sector. After decades of offshoring to low-cost countries, many firms are now returning operations to American soil in a movement known as reshoring. At the same time, automation is revolutionizing production processes—raising productivity while transforming the kinds of jobs available. Together, these forces are reshaping the American industrial workforce in profound ways.
This dual trend is creating both optimism and anxiety. On one hand, reshoring promises job growth, economic security, and national resilience. On the other, automation threatens to eliminate traditional roles while demanding higher skills, creating challenges for workers and employers alike.
Table of Contents
The Reshoring Revival: Why Companies Are Coming Back
Geopolitical and Economic Shifts
The COVID-19 pandemic laid bare the vulnerabilities of extended global supply chains. Factory shutdowns in Asia, port delays, and semiconductor shortages prompted U.S. companies to rethink their heavy reliance on overseas production. Add to this the Russia-Ukraine conflict, tensions with China, and global inflation, and reshoring has become not just practical, but strategic.
According to the Reshoring Initiative, the U.S. brought back a record 327,000 jobs in 2024, with an even higher pace anticipated in 2025. Major sectors leading this charge include semiconductors, electric vehicles (EVs), pharmaceuticals, aerospace, and electronics.
Consumer and Corporate Pressure
Consumers increasingly favor domestically produced goods for quality, ethical, and sustainability reasons. Meanwhile, investors are pushing companies to de-risk supply chains and focus on long-term resilience over short-term cost savings.
Reshoring allows companies to be more agile and responsive to customer demands—especially for highly customized or rapidly evolving products. In sectors like advanced manufacturing and defense, domestic production is now seen as essential to national security.
The Automation Boom: More Machines, Smarter Factories
While factories are returning, they look nothing like those of the past. Automation, robotics, and artificial intelligence are redefining manufacturing from the inside out.
Robots on the Assembly Line
Automated robots are now integral to many U.S. factories, handling everything from assembly to quality inspection. Collaborative robots—or “cobots”—work alongside human operators, improving safety and efficiency. Advances in machine vision and AI have enabled these machines to perform complex tasks with minimal supervision.
One example is the use of autonomous mobile robots (AMRs) in warehouse and production environments, drastically reducing the need for human transport workers and pickers.
Smart Manufacturing Systems
IoT-enabled sensors, cloud-based analytics, and predictive maintenance tools are helping manufacturers run leaner and smarter operations. These systems track equipment health, detect inefficiencies, and even make real-time adjustments to production—minimizing downtime and increasing output.
While these advances increase competitiveness, they also raise concerns about job displacement, especially for workers whose roles are repetitive or routine.
Manufacturing Jobs: What’s Changing?
Decline of Traditional Roles
Jobs involving simple assembly, material transport, and manual inspection are shrinking. Employers now look for workers who can troubleshoot equipment, analyze performance data, or manage digital platforms. This shift is often referred to as the “blue-collar reboot”—less about manual labor, more about mechatronics and software.
Rise of Hybrid Roles
New manufacturing roles blend technical know-how with problem-solving skills. These include:
- Automation Technicians: Maintain and repair robotic systems.
- Industrial Data Analysts: Monitor and interpret performance metrics.
- Digital Twin Engineers: Use simulations to optimize product design and factory layouts.
Even jobs in logistics, maintenance, and materials management now require familiarity with digital tools and data platforms.
The Talent Crisis: A Critical Skills Gap
Despite the return of factories, U.S. manufacturers are struggling to hire qualified workers. The National Association of Manufacturers warns that over 2 million jobs could go unfilled by 2030 due to a lack of skilled labor.
Root Causes
- Aging Workforce: Many skilled technicians and machine operators are nearing retirement, with too few replacements entering the pipeline.
- Perception Problems: Manufacturing is still seen by many young people as dirty, low-paid, or unstable—despite high salaries in many modern roles.
- Training Shortfalls: Few high schools and colleges offer up-to-date vocational training aligned with today’s advanced manufacturing needs.
Responses and Solutions
- Community College Partnerships: More companies are collaborating with community colleges to develop apprenticeship and certification programs in robotics, mechatronics, and industrial maintenance.
- Upskilling Initiatives: Programs like “Workforce for the Future” are helping existing employees transition from low-skill jobs to higher-paying technical roles.
- Incentives for Training: State and federal tax credits are being offered to employers that invest in workforce development and retraining.
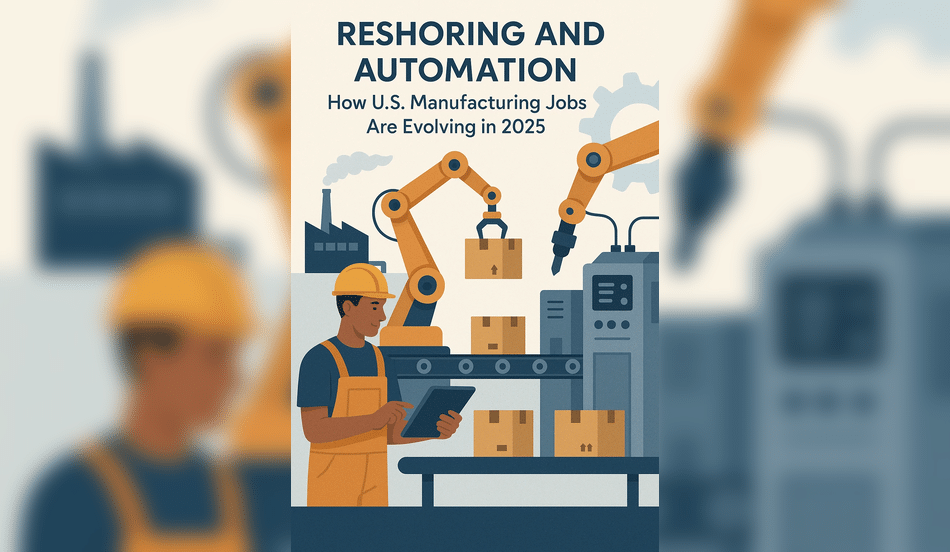
Regional Growth and Economic Resilience
Reshoring and automation are transforming local economies—especially in the South, Midwest, and parts of the Rust Belt. Cities like Columbus (Ohio), Greenville (South Carolina), and El Paso (Texas) are experiencing a renaissance as new plants open and supply chains localize.
This localized growth:
- Revives depressed areas.
- Strengthens domestic supply chains.
- Encourages innovation through local R&D hubs and university partnerships.
Yet, the benefits are not evenly distributed. Communities lacking training infrastructure or digital access risk being left behind.
Government’s Role: Catalyzing a Smart Manufacturing Ecosystem
Legislative Incentives
Several federal policies are accelerating reshoring and automation:
- CHIPS and Science Act: Offers billions in subsidies for domestic semiconductor manufacturing.
- Inflation Reduction Act: Encourages clean energy manufacturing through tax breaks and investment credits.
- Manufacturing USA: A network of innovation institutes promoting collaborative R&D and workforce training.
Infrastructure and Energy
Reliable broadband, resilient power grids, and efficient transportation are vital for modern factories. Federal infrastructure funding is helping regional clusters upgrade these systems, making them more attractive for reshoring.
Worker Concerns and Public Sentiment
Not all workers are optimistic. There’s growing fear that automation will replace more jobs than reshoring can create—particularly among older workers with limited tech exposure.
Unions and advocacy groups are calling for:
- Stronger labor protections during tech transitions.
- Equity programs to help underrepresented groups access training.
- Universal reskilling funds to prepare all citizens for the digital industrial era.
In some sectors, such as textiles and food processing, wage stagnation persists despite modernization, raising questions about who benefits from automation-driven productivity.
🏗️ Discover the Future of U.S. Manufacturing Jobs
America’s industrial landscape is evolving rapidly. With companies reshoring operations and automation redefining production, new career opportunities are emerging across advanced manufacturing, engineering, and technology sectors.
Whether you’re an experienced technician or a recent STEM graduate, WhatJobs connects you with high-demand roles at the forefront of this transformation.
👉 Explore cutting-edge manufacturing and engineering jobs now — and help shape the future of American industry.Future Outlook: A Balanced Transformation?
If executed correctly, reshoring and automation could spark a golden age of American manufacturing:
- Cleaner factories
- Safer working conditions
- Higher-skilled, higher-paid jobs
- Lower carbon emissions due to shorter supply chains
But this requires continuous investment in human capital. Without it, automation will deepen inequality, and reshoring may underdeliver on its job-creation promises.
FAQs
Q: Are reshored factories creating as many jobs as expected?
A: Not always. Many new facilities rely heavily on automation, which means fewer workers per unit of output—though the jobs created are typically higher skilled and better paid.
Q: What’s the biggest challenge for U.S. manufacturers today?
A: The lack of skilled labor, especially in automation, robotics, and industrial software roles.
Q: How can workers prepare for the future of manufacturing?
A: By acquiring digital and technical skills through vocational training, certifications, or community college programs in relevant fields.
Q: Will automation eliminate more jobs than it creates?
A: In the short term, some routine roles may disappear. But long-term success depends on reskilling the workforce to fill the new types of jobs that automation creates.
Final Thoughts
America’s manufacturing revival is real—but it’s not your grandfather’s assembly line. Factories today are smart, connected, and increasingly autonomous. Reshoring is bringing them home, but automation is defining how they operate and who they employ.
For policymakers, educators, and industry leaders, the mission is clear: Build a future where reshoring and robotics don’t just coexist—but collaborate to deliver quality jobs, resilient supply chains, and inclusive growth. The manufacturing renaissance is here—but only if we’re prepared to meet it with skills, strategy, and shared purpose.