2,042 Industrial Process jobs in the United States
Industrial/Process Engineer
Posted 9 days ago
Job Viewed
Job Description
Job Type
Full-time
Description
ME Elecmetal is a globally competitive supplier, recognized by its excellence and leadership in the delivery of integral solutions which add value to the mining processes and to other target markets. Our fast-paced production environment is recruiting for a talented and experienced Industrial Engineer in its Duluth, MN foundry.
Industrial Engineer: The Industrial Engineer will develop and maintain systems to accurately measure the specific cost of all products. Establish and maintain production standards, systems, and methods. Provide accurate product quotations and costs. Reduce operating costs by improving methods, processes, equipment, and materials for the effective utilization of human and plant resources to improve quality and productivity.
- Maintain costing, labor, quoting, and engineering data in the SAP Product Master.
- Coordinate, monitor, and ensure proper administrative controls are completed accurately by the appropriate person on all samples.
- Develop and maintain production standards through time studies, audits and other analytical processes to determine accurate product cost and efficiencies.
- Develop alternative production methods where appropriate based on labor and cost reductions.
- Keep Manager, Manufacturing informed of all relevant activity and actions.
- Maintain knowledge and understanding of the developments and changes in foundry technology.
This position must have an Engineering degree in Industrial Engineering, Systems Engineering, or a closely related field with a minimum of 1 year of related experience.
All qualified candidates must be:
- Committed to creating a safe work environment
- Adhere to high performance standards
- Able to work in a hot environment
- Committed to producing high quality products
- Willing to work in an environment that expects excellence.
OUR VISION:
Our Vision is to be a globally competitive supplier, recognized by its excellence and leadership in the delivery of integral solutions which add value to the mining processes and to other target markets.
OUR MISSION:
Our mission is to meet the needs and exceed the expectations of our shareholders, customers, employees, and communities where we operate, by providing comprehensive solutions to the market.
Our Values:
- Respect for integrity
- Teamwork
- Commitment to the community and environment
- Creativity and innovation
- Customer focus
- Proactive search for excellence
- Human development
- Responsibility and integrity
We are looking for employees who share our vision, mission and values. ME Elecmetal is an Equal Opportunity Employer and Drug Free Workplace.
Salary Description
$75,000 - $100,000
Industrial Process Engineer
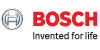
Posted 3 days ago
Job Viewed
Job Description
Welcome to Bosch Power Tools in West Memphis, AR, where innovation meets action in our bustling warehousing operation! As a key division of Robert Bosch Tool Corporation NA, we're not just distributing top-tier power tools-we're driving excellence and efficiency every step of the way. Our facility is a hub of activity, where every day is an adventure in logistics and distribution.
Here at Bosch Power Tools, we infuse our work with passion, energy, and a sense of ownership. Our team thrives on the excitement of optimizing operations and delivering high-quality tools to professionals around the world. We believe in making work fun and engaging while pushing the boundaries of what's possible in warehousing and distribution.
If you're ready to join a team where your drive and enthusiasm are valued, and where every role contributes to our mission, come experience the #LikeABosch spirit with us!
**Job Description**
The Industrial Process Engineer is responsible for driving operational excellence within both distribution and production environments. This role ensures process efficiency and standardization through the application of Bosch Production System principles, Lean Manufacturing concepts, and data-driven problem-solving methodologies. The Industrial Process Engineer collaborates with cross-functional teams to integrate new products, optimize workflows, and meet customer expectations while maintaining cost targets and safety standards.
**Primary Duties and Accountabilities:**
Operational Excellence and Continuous Improvement: Drive operational excellence initiatives with Engineering, Design, Project Management, Operations, and Logistics teams. Utilize Lean Production principles and BPS methodologies to identify and implement process improvements.
Process Standardization and Optimization: Support standardization and modularization in a Make-to-Order (MTO) environment to enhance efficiency. Integrate new products and processes into existing manufacturing systems while ensuring seamless transition.
Cost and Quality Control: Analyze product cost drivers and implement changes to meet cost targets. Define, measure, analyze, implement, and improve processes using data-driven approaches.
Problem Solving and Data Analysis **:** Utilize Plan-Do-Check-Act (PDCA) and A3 methodologies to control processes and drive sustainable improvement.
Cost and Quality Control: Analyze product cost drivers and implement changes to meet cost targets. Define, measure, analyze, implement, and improve processes using data-driven approaches.
Shop Floor and Logistics Support: Provide direct shop floor support to resolve process-related issues. Collaborate with engineers, planners, supervisors, and associates to optimize material flow and production efficiency. Apply Statistical Process Control (SPC) techniques and problem-solving tools in a production setting.
Software and Systems Utilization: Use SAP and Microsoft Office tools for data analysis and report generation. Work with CAD software to support process and line design activities.
Safety and Compliance: Ensure compliance with industrial safety requirements, including ergonomics and control system functionality. Develop and implement safety-conscious process improvements.
**Qualifications**
+ Bachelor's degree in Industrial Engineering, Mechanical Engineering, Electrical Engineering, Mechatronics or a related technical field required.
+ BPS (Bosch Production System) knowledge and experience preferred
+ Microsoft Excel, Word, Outlook and Warehouse Management (WMS) familiarity preferred
+ Knowledge of quality processes, product requirements, as well as quality hold reasons, typical product damages, and customer requirements for products.
+ 3-5 years of previous experience in a similar position
**Proficiency:**
+ Proven aptitude for line design, logistic movements, and process optimization.
+ Experience in executing projects and implementing Lean Manufacturing concepts.
+ Strong analytical and problem-solving skills with attention to technical details.
+ Ability to effectively communicate and collaborate across departments.
+ Proficiency in CAD software, SAP and data analysis tools.
+ Knowledge of industrial safety regulations and ergonomic standards.
+ Excellent verbal and written communication skills.
**Additional Information**
BOSCH is a proud supporter of STEM (Science, Technology, Engineering & Mathematics) Initiatives
+ FIRST Robotics (For Inspiration and Recognition of Science and Technology)
+ AWIM (A World In Motion)
Equal Opportunity Employer, including disability/veterans.
Thanks to the work of every associate, Bosch has been recognized for award-winning culture by the following organizations:
+ Great Place to Work Certified, 2024
+ Fortune's World's Most Admired Companies, 2024
+ America's Best Large Employers, 2024
+ America's Best Employers for Diversity, 2024
+ America's Greatest Workplaces for Women, Newsweek2024
+ Greatest Workplaces for Diversity, Newsweek 2024
**Indefinite U.S. work authorized individuals only. Future sponsorship for work authorization is not available.**
The U.S. base salary range for this full-time position is $90,000 to $105,000. Within the range, individual pay is determined based on several factors, including, but not limited to, work experience and job knowledge, complexity of the role, job location, etc.
In addition to your base salary, Bosch offers a comprehensive benefits package that includes health, dental, and vision plans; health savings accounts (HSA); flexible spending accounts; 401(K) retirement plan with an attractive employer match; wellness programs; life insurance; short and long term disability insurance; paid time off; parental leave, adoption assistance; and reimbursement of education expenses. Learn more about our full benefits offerings by visiting: . Pay ranges included in the postings generally reflect base salary; certain positions may include bonus, commission, or additional benefits.
Salary estimates published on online job boards, rather than the Bosch US Careers Page, may not be a true representation of the actual pay range offered for this position.
Industrial Process Engineer
Posted 19 days ago
Job Viewed
Job Description
Are you a process engineer with a passion for working on complex industrial (refining, chemical and power) engineering projects in a dynamic, multi-disciplinary environment? Eichleay is looking for an Industrial Process Engineer to join our process engineering team at Eichleay. This position offers the flexibility to work remotely. It may be based from a home office within 50 miles of one of Eichleay’s office locations - Orange, CA; Larkspur, CA; Billings, MT; or Ferndale, WA. We also welcome applicants located in states where Eichleay operates across the Western U.S., including CA, CO, ID, MT, NV, and WA. Please note that all remote roles will involve periodic travel. Don’t miss out on this exciting career move!
Compensation : $100,000-$150,000 *anticipated annual salary may vary based on skills, experience, qualifications and internal peer equity. The pay range listed for this position is based on the anticipated base compensation at the time of the posting.
Company Overview:
Eichleay is a dynamic organization with over 150 years of experience in delivering project management and engineering solutions across various industries, including life sciences, energy, and chemicals, power, and food and beverage. We are committed to innovation, excellence, and building long-lasting relationships with our clients.
Position Summary:
Do you enjoy getting involved in small to large projects collaborating with multi-disciplinary teams of engineers and designers? At Eichleay you will perform design engineering for a variety of brown field and revamp facilities in the refining, chemical and power industries. Design engineering consists of feasibility through detailed design and construction for reimbursable & lump sum projects.
Your duties will include performing process simulations / studies, heat and material balances, process flow diagram (PFD) and piping & instrumentation diagram/drawings (P&ID) development, design calculations, hydraulics and line sizing, equipment data sheets/specifications, utility requirements/systems analysis, relief contingency analysis and pressure safety valve (PSV) sizing, process engineering reports, and proposal development.
You may provide technical guidance to less experienced design and engineering personnel.
Key Responsibilities:
- Apply extensive and diversified knowledge of Chemical Engineering principles to complete process engineering tasks with minimal supervision.
- Interface with other internal engineering disciplines (mechanical, piping, civil/structural, electrical, instrumentation, automation, architecture) to ensure a coordinated design and complete engineering deliverables.
- Work on all project phases from feasibility studies, conceptual design, detailed design and construction support.
- Develop process data sheets for stationary and rotating equipment including pressure vessels, tanks, separators, filters, heat transfer equipment, pumps, and compressors.
- Review vendor drawings to ensure design accuracy and compliance with specifications.
- Oversee and/or produce process engineering calculations such as pressure drop, PSV sizing, and equipment sizing.
- Perform utility sizing calculations and utility system analysis.
- Prepare and complete equipment Qualification and/or Commissioning documentation.
- Participate in Process Hazard Analysis (PHA) sessions.
- Attend Factory Acceptance Testing and Site Acceptance Testing.
- Provide construction support activities including responding to submittals and RFIs.
- Consistently achieve goals, deliver quality and accurate work, and meet timelines. This includes reviewing project documents for conformity and quality assurance.
- May independently lead projects, manage process budgets and resources for small to medium sized projects.
Job Requirements:
- Experience: Minimum of 5 years of experience in process engineering, with demonstrated expertise in applying Chemical Engineering principles to execute complex, multi-discipline refinery or chemical plant projects.
- Education: Bachelor of Science in Chemical Engineering from an ABET accredited program.
- Skills: Strong communication skills, including writing skills, preparing reports to describe design conclusions, deliver presentations, analyses, etc.
Technical Competence:
- Experience developing process data sheets for stationary and rotating equipment including pressure vessels, tanks, separators, filters, heat transfer equipment, pumps, and compressors.
- Thorough knowledge of API, ASME and ANSI standards.
- Simulation experience using HYSYS, PRO II or other comparable process simulation software.
- Understanding of refinery or chemical plant unit operations.
- Proven ability to develop PFDs and P&IDs.
- Safety: Demonstrates awareness and commitment to health, safety, and environmental issues. Addresses those issues as necessary to ensure zero harm to all employees, clients, and contractors with zero environmental incidents.
- Collaboration: Ability to form and foster collaborative relationships within Eichleay and with clients and partners.
Preferred Skills/Experience:
- Professional Engineer (PE) Certification preferred
Industry Requirements:
This role may require all or some of the following requirements (as applicable):
- Client cGMP and Sterile Area Training and current badge or ability to obtain.
- RSO Safety Training and current card or ability to obtain.
- Client Safety Training and current badge or ability to obtain.
- TWIC Certification and current card or ability to obtain.
- Background screening including previous employment, education, criminal history, and driving record verification.
- Participation in random drug and alcohol program.
Work Environment and Physical Demands:
The characteristics described below are representative of those encountered while performing the essential functions of this position. Reasonable accommodation will be made to enable individuals with disabilities to perform the essential functions.
While performing duties of this job, you would occasionally be required to stand, walk, sit, reach with hands and arms, climb or balance, stoop or kneel, talk and hear (this includes being able to hear and talk on site based communication equipment), distinguish between various colors, be able to hear safety tones/notifications, and use fingers and hands to feel objects, tools, temperature or controls.
- Must occasionally lift and/or move up to 25 pounds.
- Specific vision abilities required include close vision, distance vision, depth perceptions, and the ability to adjust focus.
- Overtime may be necessary as workload dictates. This may include weekdays, weekends and/or holidays.
- Job duties may be performed at a Client’s office, client site, production facility or industrial/construction job site. Day to day job direction will typically be lead by our Clients designated project leader.
- Conditions and/or schedule will vary at each Client location, but the conditions listed above will generally apply.
- Candidates will be required to follow our clients' site based rules and protocols regarding infectious diseases.
All opportunities with Eichleay will require authorization to work in the US without the need for sponsorship. Positions will require in-person interactions and may require working onsite in an office or field envir onment. This position is subject to federally mandated drug/alcohol testing. Candidates applying to Eichleay must have the ability to be badged and maintain a badge as a safety sensitive position and/or within the Building and Construction trade for process safety management governed facilities. This will require in-depth drug screening for all positions.
We are an equal opportunity employer and value diversity at our company. Qualified applicants will receive consideration for employment without regard to race, color, religious creed, sex (including pregnancy, childbirth, breast-feeding and related medical conditions), sexual orientation, gender identity, gender expression, national origin or ancestry, age, mental or physical disability (including medical condition), military or veteran status, political preference, marital status, citizenship, genetic information or other status protected by law or regulation.
Education Required- Bachelors or better in Engineering
- cGMP Certification
- Professional Engineer
- TUV Certification
- TWIC
- Adaptability
- AutoCAD
- Automation
- Bluebeam
- Cadworks
- Application of codes and standards
- Collaboration
- Communication
- Computer skills
- Construction support
- Creativity
- Critical thinking
- Attention to detail
- Estimates
- Phase gate
- Interpersonal
- Quick learner
- Material requisition
- Navis Works
- Problem-solving
- Presentation skills
- Quality assurance
- Revit
- Research skills
- Software skills
- Technical bid evaluation
- Teamwork
- Time management
- Work package
Equal Opportunity Employer
This employer is required to notify all applicants of their rights pursuant to federal employment laws. For further information, please review the Know Your Rights notice from the Department of Labor.
Industrial Process Technician
Posted today
Job Viewed
Job Description
Description
Job duties as an industrial technician include working to install, maintain, and repair industrial equipment and their associated electrical or mechanical systems. In addition to providing maintenance, you may be called in to troubleshoot malfunctioning equipment to keep operations online and on schedule. Install equipment on-site. Manage the routine maintenance of a customers equipment and ensure they're working properly. Perform repairs on faulty equipment as soon as possible. Coordinate with all other teams in the customer organization while managing on-site installation, repair, maintenance, testing, error diagnosis, technical problem solving and determining proper solutions.
Industrial Maintenance Technician Job Responsibilities:
- Installs, repairs, and maintains machinery and mechanical equipment by completing preventive maintenance inspection and reporting all required repairs or deficiencies.
- Locates sources of problems by observing mechanical devices in operation.
- Dismantles machinery and removes/replaces defective parts.
- Determines changes in requirements of parts by inspecting and measuring various instruments for proper performance operation and calibration.
- Maintains inventories of equipment parts and supplies by checking stock and placing orders as required for scheduled repairs and on site inventories.
- Trains production workers on routine preventive maintenance and operation of equipment.
- Provides mechanical maintenance information by answering questions and requests.
- Prepares maintenance reports by collecting, analyzing, and summarizing information and trends.
- Maintains a safe and clean work environment by complying with procedures, rules, and regulations.
- Ability to operate adjust and maintain compressor and all associated components.
- In-depth knowledge of system maintenance requirements for Low, and Medium temperature chillers.
- Knowledge of DX, Flooded, Liquid Overfeed, Recirculation, pumped or gravity fed systems.
- Familiarity with safety standards and regulations of OSHA, RETA, EPA, along with PSM, ERP and related process safety compliance.
- Skilled in analyzing information and creating reports and determining proper repair parts and time required to restore equipment to proper operation
Salary Description$80,000 - $120,000
Industrial Process Technician
Posted 2 days ago
Job Viewed
Job Description
Job Type
Full-time
Description
This is a full-time, direct placement role at Letsos Company.
Job duties as an industrial technician include working to install, maintain, and repair industrial equipment and their associated electrical or mechanical systems. In addition to providing maintenance, you may be called in to troubleshoot malfunctioning equipment to keep operations online and on schedule. Install equipment on-site. Manage the routine maintenance of a customer's equipment and ensure they're working properly. Perform repairs on faulty equipment as soon as possible. Coordinate with all other teams in the customer organization while managing on-site installation, repair, maintenance, testing, error diagnosis, technical problem solving and determining proper solutions.
Industrial Maintenance Technician Job Responsibilities:
- Installs, repairs, and maintains machinery and mechanical equipment by completing preventive maintenance inspection and reporting all required repairs or deficiencies.
- Locates sources of problems by observing mechanical devices in operation.
- Dismantles machinery and removes/replaces defective parts.
- Determines changes in requirements of parts by inspecting and measuring various instruments for proper performance operation and calibration.
- Maintains inventories of equipment parts and supplies by checking stock and placing orders as required for scheduled repairs and on site inventories.
- Trains production workers on routine preventive maintenance and operation of equipment.
- Provides mechanical maintenance information by answering questions and requests.
- Prepares maintenance reports by collecting, analyzing, and summarizing information and trends.
- Maintains a safe and clean work environment by complying with procedures, rules, and regulations.
- Ability to operate adjust and maintain compressor and all associated components.
- In-depth knowledge of system maintenance requirements for Low, and Medium temperature chillers.
- Knowledge of DX, Flooded, Liquid Overfeed, Recirculation, pumped or gravity fed systems.
- Familiarity with safety standards and regulations of OSHA, RETA, EPA, along with PSM, ERP and related process safety compliance.
- Skilled in analyzing information and creating reports and determining proper repair parts and time required to restore equipment to proper operation
Salary Description
$80,000 - $120,000
Industrial / Process Architect
Posted 10 days ago
Job Viewed
Job Description
Our vision is simple. In our commitment to the Southeast, we create architecture that enriches community through a culture of design excellence and expertise, innovation and collaborative engagement.
What sets us apart is our unwavering commitment to creating spaces that enrich communities with lasting impact. Our projects are driven by a deep understanding of local culture, needs, and aspirations, resulting in designs that resonate with and enhance the communities they serve.
At LS3P, we don't just design buildings; we create iconic landmarks that define skylines, inspire people, and transform spaces. Join us in shaping the future of architecture and design in the Southeast!
We are currently seeking an Industrial / Process Architect to join our Raleigh office. In this role, you will play a pivotal role in growing our pharmaceutical manufacturing business. You possess experience in planning and design for the life sciences realm, specifically in biotechnology, pharmaceutical, biomedical or other process architecture. You are passionate about design and devoted to quality. You possess the organizational skills to prioritize tasks and handle multiple deadlines, a thorough knowledge of relevant codes, operations, processes and trends, a demonstrated ability to mentor and manage teams, and foster and nurture Client relationships.
A Day in the Life:
Work in a collaborative team environment to spearhead development of biopharmaceutical planning strategies at all levels of detail from initial planning through construction.
- Create visual presentations and communications for client interactions
- Able to partner with and work collaboratively with Process Engineers
- Develop design assignments throughout all project phases
- Support communication between project team, client, vendors, contractors, and consultants
- Play an integral part in overall client satisfaction, design quality and profitability of all projects undertaken that contribute to the firm's strategic priorities
- Foster and support creative pharmaceutical manufacturing planning, technical design and detailing decisions that align with project goals, cost implications, sustainability, and other factors.
- Technical production skills and a demonstrated ability to effectively produce design and construction documents
- Expertise in designing sophisticated biopharmaceutical manufacturing facilities.
- Drive to build out a team and lead projects in the life sciences industry.
- Proficiency in Revit
- Experience with 3D communication, by hand or graphic software such as SketchUp, Lumion, or Enscape
- Understanding of relevant codes such as state building codes, ANSI 117.1, BOMA
- LEED accreditation or interest in achieving accreditation is preferred
- Understanding of the design and procurement processes
- Ability to direct and motivate work efforts of others and handle project challenges
- Capability to self-manage project assignments from start to finish with oversight
- Experience with incorporating research in design process
- Registered Architect with Bachelor's Degree or Master's Degree in Architecture from a NAAB-accredited university
- Solid experience in process architecture.
- 10+ years of design experience post licensure is preferred, including at least 8 years in the field of pharmaceutical or biotechnology design/engineering/construction.
- Personal network in the life science industry desired
Life at LS3P
Together, we are building the skylines of the Southeast.
Our values articulate our beliefs and ground us in a common culture. They are the core of our practice, and reflect the "who" of our community.
- EXCELLENCE is a beginning point
- INTEGRITY is at the core of our decision making and actions
- EMPOWERMENT with accountability makes better decisions
- COLLABORATION leverages the best in everyone
- BALANCE gives us fuel to do our best
- STEWARDSHIP ensures a future
- CARING for each other is what holds us together
LS3P's Commitment To You:
- Ongoing engagement with fantastic design team members
- To develop new skills and contribute to world-class projects
- Participate in meaningful collaboration and research efforts
- A competitive compensation and benefits package
- Professional development allowance to toward educational opportunities
- Leadership development and mentoring across sectors, markets, offices and the firm
- Participation in community service and outreach occasions supporting local and national organizations
- Flexibility and balance in your schedule
LS3P recognizes the value of diversity and inclusion in our workplace. We are committed to equal opportunity and believe that inclusivity benefits us all. We actively seek and consider all qualified employment applications without regard to race, color, religion, gender, age, national origin, disability, sexual orientation, sexual preference, partnership status, gender identity, pregnancy, childbirth, or related medical conditions and protected veteran status, status of participation in the U.S. Armed Services, or any other status protected by federal, state or local law.
Industrial / Process Architect
Posted 1 day ago
Job Viewed
Job Description
What sets us apart is our unwavering commitment to creating spaces that enrich communities with lasting impact. Our projects are driven by a deep understanding of local culture, needs, and aspirations, resulting in designs that resonate with and enhance the communities they serve.
At LS3P, we don't just design buildings; we create iconic landmarks that define skylines, inspire people, and transform spaces. Join us in shaping the future of architecture and design in the Southeast!
We are currently seeking an Industrial / Process Architect to join our Raleigh office. In this role, you will play a pivotal role in growing our pharmaceutical manufacturing business. You possess experience in planning and design for the life sciences realm, specifically in biotechnology, pharmaceutical, biomedical or other process architecture. You are passionate about design and devoted to quality. You possess the organizational skills to prioritize tasks and handle multiple deadlines, a thorough knowledge of relevant codes, operations, processes and trends, a demonstrated ability to mentor and manage teams, and foster and nurture Client relationships. A Day in the Life:Work in a collaborative team environment to spearhead development of biopharmaceutical planning strategies at all levels of detail from initial planning through construction.
- Create visual presentations and communications for client interactions
- Able to partner with and work collaboratively with Process Engineers
- Develop design assignments throughout all project phases
- Support communication between project team, client, vendors, contractors, and consultants
- Play an integral part in overall client satisfaction, design quality and profitability of all projects undertaken that contribute to the firm's strategic priorities
- Foster and support creative pharmaceutical manufacturing planning, technical design and detailing decisions that align with project goals, cost implications, sustainability, and other factors.
- Technical production skills and a demonstrated ability to effectively produce design and construction documents
- Expertise in designing sophisticated biopharmaceutical manufacturing facilities.
- Drive to build out a team and lead projects in the life sciences industry.
- Proficiency in Revit
- Experience with 3D communication, by hand or graphic software such as SketchUp, Lumion, or Enscape
- Understanding of relevant codes such as state building codes, ANSI 117.1, BOMA
- LEED accreditation or interest in achieving accreditation is preferred
- Understanding of the design and procurement processes
- Ability to direct and motivate work efforts of others and handle project challenges
- Capability to self-manage project assignments from start to finish with oversight
- Experience with incorporating research in design process
- Registered Architect with Bachelor's Degree or Master's Degree in Architecture from a NAAB-accredited university
- Solid experience in process architecture.
- 10+ years of design experience post licensure is preferred, including at least 8 years in the field of pharmaceutical or biotechnology design/engineering/construction.
- Personal network in the life science industry desired
A cover letter, resume and portfolio demonstrating Revit skills and rendering abilities are required.
Life at LS3PTogether, we are building the skylines of the Southeast.
Our values articulate our beliefs and ground us in a common culture. They are the core of our practice, and reflect the "who" of our community.
- EXCELLENCE is a beginning point
- INTEGRITY is at the core of our decision making and actions
- EMPOWERMENT with accountability makes better decisions
- COLLABORATION leverages the best in everyone
- BALANCE gives us fuel to do our best
- STEWARDSHIP ensures a future
- CARING for each other is what holds us together
We are made up of 12 offices that celebrate their own unique traditions, but we embrace a "one firm" attitude that unifies us.
LS3P's Commitment To You:
- Ongoing engagement with fantastic design team members
- To develop new skills and contribute to world-class projects
- Participate in meaningful collaboration and research efforts
- A competitive compensation and benefits package
- Professional development allowance to toward educational opportunities
- Leadership development and mentoring across sectors, markets, offices and the firm
- Participation in community service and outreach occasions supporting local and national organizations
- Flexibility and balance in your schedule
LS3P recognizes the value of diversity and inclusion in our workplace. We are committed to equal opportunity and believe that inclusivity benefits us all. We actively seek and consider all qualified employment applications without regard to race, color, religion, gender, age, national origin, disability, sexual orientation, sexual preference, partnership status, gender identity, pregnancy, childbirth, or related medical conditions and protected veteran status, status of participation in the U.S. Armed Services, or any other status protected by federal, state or local law.
Be The First To Know
About the latest Industrial process Jobs in United States !
Industrial Process Technician
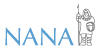
Posted today
Job Viewed
Job Description
**Responsibilities**
+ The Incumbent performs troubleshooting, repair, overhaul, maintenance, and servicing of commercial and Industrial chillers and process piping systems.
+ Skilled and certified in the repair of HVAC equipment and in the usage of moisture, temperature, pressure and flow measurement equipment for air and fluids.
+ Keeps supervisor apprised of unique situations and problems encountered and identify and reports safety, environmental and other work requirements for resolution.
+ Scans utility systems such as water and steam piping system for leaks or other problems such as waterlogged steam traps. Lubricate, grease oil & perform filter changes plus labeling of all lubrication points.
+ Performs periodic inspections on chiller systems; troubleshoots and locates malfunctions, diagnoses problems, and performs condition assessments as directed and completes appropriate repairs with minimal supervision.
+ Repairs or replaces compressors and components, electric motors, fans, belts, and pulleys.
+ Services and repairs evaporators, condensers, and receivers. Repacks valves, lubricates moving parts, replaces filters, and cleans coils.
+ Repairs components within a system to include transformers, motors, electrodes, solenoids, rheostats, and aqua stats.
+ Utilizes and interprets technical manuals, shop directives, blueprints, sketches, diagrams, and specifications, verbal and written instructions.
+ Responsible for completing daily work order log documenting inspections, maintenance and repair information, to include work performed, materials used, and hours worked on each assigned work order.
+ Responds to after normal working hours callouts as needed.
+ Interfaces with customers and responsible for customer feedback, as applicable.
+ Operates motor vehicles in accordance with company vehicle policies.
+ Complies with applicable federal, state, United States Air Force (USAF) and Occupational Safety & Health Administration (OSHA) environmental laws and regulations.
+ Complies with health and safety rules and procedures; performs work in a manner that enhances the safety of the work environment.
+ Incumbent will always wear appropriate Personal Protective Equipment (PPE) as determined by position and duties.
+ Performs other related duties as assigned.
Accountable for:
+ Accurate, timely, and cost-effective performance of duties.
+ Working harmoniously with customers and fellow co-workers.
+ Maintaining strict confidentiality of all Akima related matters.
+ Accountable for assigned tools, materials, and equipment.
+ Cleanliness and safety of shop and work areas.
**Qualifications**
+ Must have an Oklahoma Mechanical Journeyman License.
+ Must have a Factory Trained Certification from three (3) of the four (4) major chiller companies i.e. Carrier, Dakin, Trane and/or York Chillers (Chiller Certifications).
+ Must have a minimum Fifteen (15) years' licensed experience in heating, ventilation, air-conditioning, and refrigeration repair with minimum of ten (10) years' experience working on large ton chillers (100-ton and over) and process piping, including troubleshooting, corrective and preventative maintenance operations.
+ Must have a basic understanding of DDC controls and automatic control monitoring systems.
+ Must have basic computer skills and familiarity with Microsoft Office applications.
+ Must have a current state driver's license, acceptable driving record, and proof of valid insurance.
+ Must have a Universal Refrigerant license.
+ Must have the ability to obtain and maintain all necessary licenses/IDs/certifications.
+ Must maintain the ability to solve problems and work independently with minimal supervision.
+ Must maintain the ability to adapt to changes in technology and applicable facility/infrastructure codes and standards.
+ Must be familiar with facility/infrastructure codes and standards, as applicable.
+ Must have the ability to deal with a variety of people in a professional & courteous manner in diverse situations.
+ Must be proficient & possess the knowledge of a variety of hand and power tools.
+ Must demonstrate the working ability read, write, speak and understand English.
+ Must have a minimum of a High School diploma or GED.
Preferred Qualification:
+ Eighteen (18) years' experience in heating, ventilation, air-conditioning and refrigeration repair, and process piping including preventative maintenance operations.
+ Factory Trained Certification from the four major chiller companies (Carrier, Dakin, Trane and York).
+ Military experience.
+ Previous experience working on a military installation.
+ Experience working on Tinker AFB facilities.
+ Familiarity with military-specific facility/infrastructure codes and standards, as applicable.
Physical Demands:
While performing duties of this job, the employee is occasionally required to stand and/or walk for long periods at a time, sit, use hands and fingers, handle, or feel objects, tools or controls, reach with hands and arms, climb stairs, balance, stoop, kneel, crouch or crawl. The employee must be able to hear and speak. The employee must occasionally lift up to 50 pounds. Lifts exceeding 50 pounds will be accomplished with two-man teams and using appropriate safety equipment to efficiently accomplish the task. The employee must be able to work in confined spaces or at heights of 120 feet (such as in a manlift/boom lift). The employee is occasionally required to work other than normal duty hours, which may include evenings weekends and/or holidays.
This position may currently and/or in the future be required to obtain and retain a favorable National Agency Check (NAC) and/or Personal Clearance (PCL) as required by law or contract.
**Job ID**
2024-13378
**Work Type**
On-Site
**Company Description**
**Work Where it Matters**
RiverTech, an Akima company, is not just another federal professional solutions contractor. As an Alaska Native Corporation (ANC), our mission and purpose extend beyond our exciting federal projects as we support our shareholder communities in Alaska.
At RiverTech, the work you do every day makes a difference in the lives of our 15,000 Iñupiat shareholders, a group of Alaska natives from one of the most remote and harshest environments in the United States.
**For our shareholders** , RiverTech provides support and employment opportunities and contributes to the survival of a culture that has thrived above the Arctic Circle for more than 10,000 years.
**For our government customers** , RiverTech provides innovative solutions to complex engineering and operational challenges and delivers wide-ranging services for mission support, systems engineering, and IT.
**As a RiverTech employee** , you will be surrounded by a challenging, yet supportive work environment that is committed to innovation and diversity, two of our most important values. You will also have access to our comprehensive benefits and competitive pay in addition to growth opportunities and excellent retirement options.
We are an equal opportunity employer and comply with all applicable federal, state, and local fair employment practices laws. All applicants will receive consideration for employment, without regard to race, color, religion, creed, national origin, gender or gender-identity, age, marital status, sexual orientation, veteran status, disability, pregnancy or parental status, or any other basis prohibited by law. If you are an individual with a disability, or have known limitations related to pregnancy, childbirth, or related medical conditions, and would like to request a reasonable accommodation for any part of the employment process, please contact us at or (information about job applications status is not available at this contact information).
Industrial Process Safety Consultant

Posted today
Job Viewed
Job Description
Baltimore, Maryland, United States; Blacksburg, Virginia, United States; Columbia, Maryland, United States; Fairfax, Virginia, United States; Rockville, Maryland, United States
**Company Overview**
Throughout our worldwide network of experts, clients and communities, we are renowned for our leadership in fire protection engineering - a legacy of responsibility we have proudly upheld since 1939. Today, our expertise extends broadly across closely related security and risk-based fields - from accessibility consulting and risk analysis to process safety, forensic investigations, security risk consulting, emergency management, digital innovation and more.
Our engineers and consultants collaborate to solve complex safety and security challenges, ensuring our clients can protect what matters most. For over 80 years, we have helped mitigate risks that threaten lives, property and reputations. Through technology, expertise and industry-leading research, we remain dedicated to our purpose of making our world safe, secure and resilient.
At Jensen Hughes, we believe that creating and sustaining a culture of trust, integrity and professional growth starts with putting our people first. Our employees are our greatest strength, and we value the unique perspectives and talents they bring to our organization.
Our wide range of Global Employee Networks connect people from across the organization, supporting career development and providing forums for individuals to share experiences on topics they're passionate about. Together, we are cultivating a connected culture where everyone has the opportunity to learn, grow and succeed together.
**Job Overview**
Jensen Hughes is seeking an Industrial and Process Safety Consultant to join our South Team with office locations in Baltimore, MD, Columbia, MD, Rockville, MD, Fairfax, VA and Blacksburg, VA. We are open to other locations and remote work for candidates with demonstrated experience and capability. A successful candidate will demonstrate ability to perform or direct engineering consulting services pertaining to process and material hazards in the industrial section. This market segment is a key growth area for our company and offers opportunities for increasing industry engagement, business development and mentorship of emerging professionals.
**Responsibilities**
+ Perform and manage engineering work associated with storage and use of flammable and combustible liquids, flammable gases, oxidizers, toxics, corrosives, and other hazardous materials
+ Conduct site inspections to observe existing operations at client facilities, perform engineering analyses, and recommend additions/revisions to client plans and procedures
+ Conduct site inspections to perform combustible Dust Hazard Analysis (DHA) and evaluate compliance with related industry standards
+ Conduct Process Hazard Analyses (PHAs) for unique, high-hazard and high-value industrial and manufacturing facilities
+ Perform Process Safety Management (PSM) system audits and support creation of PSM programs
+ Prepare hazardous materials inventory statements, hazardous materials management plans and similar documentation to fulfill requirements of codes, regulations, or insurance carriers
+ Develop explosion protection system designs and budgetary cost estimates
+ Conduct third-party review and acceptance testing of explosion protection systems
+ Conduct electrical classification assessments for NEC Chapter 5 compliance
+ Execute business development plans for clients, markets and sectors related to industrial and process safety consulting
+ Support multiple projects while meeting deadlines and working with a variety of personnel under a range of conditions
**Requirements and Qualifications**
+ High-level written and oral communication skills to do reports, correspondence, presentations, etc.
+ Demonstrated knowledge of engineering practices, process safety principles, and industry standards applying to combustible dust handling operations, including but not limited to:
+ NFPA standards 30, 70, 77, 400, 660
+ International Fire Code and NFPA 1
+ Knowledge of Instrumentation & Controls (safety instrumented systems) is desired but not required
+ Bachelor's Degree from four-year college and 3+ years of related experience. 5+ years of related experience preferred.
+ Professional Engineer (PE), Certified Safety Professional (CSP), Certified Industrial Hygienist (CIH), Institute of Safety and Health Management (ISHM) or comparable certification strongly preferred
+ Ability to travel up to 30% for project work
+ Ability to support multiple projects and effectively share workload with colleagues across regional and service line boundaries to fulfill client expectations.
#LI-AW1
#LI-Hybrid
#LI-Remote
**_Jensen Hughes is an Equal Opportunity Employer. Qualified candidates will receive consideration for employment without regard to race, color, religion, sex, national origin, sexual orientation, gender identity, disability or protected veteran status._**
The security of your personal data is important to us. Jensen Hughes has implemented reasonable physical, technical, and administrative security standards to protect personal data from loss, misuse, alteration, or destruction. We protect your personal data against unauthorized access, use, or disclosure, using security technologies and procedures, such as encryption and limited access. Only authorized individuals may access your personal data for the purpose for which it was collected, and these individuals receive training about the importance of protecting personal data. Jensen Hughes is committed to compliance with all relevant data privacy laws in all areas where we do business, including, but not limited to, the GDPR and the CCPA. Additionally, our service providers are contractually bound to maintain the confidentiality of personal data and may not use the information for any unauthorized purpose.
*Policy on use of 3rd party recruiting agency for direct placements
Jensen Hughes will occasionally augment a recruiting search through agencies for certain positions when business conditions warrant. Jensen Hughes will not accept resumes, inquiries or proposals from recruiting agencies as an acceptable method to consider a candidate. 3rd party recruiting agencies must sign a standard Jensen Hughes agreement after being evaluated and accepted by a Human Resources or Talent Acquisition manager, or member of the talent acquisition team. Hiring managers and employees of Jensen Hughes are not authorized to accept resumes, engage in fee-based searches through recruiting firms or sign a search agreement. Please note this policy does not apply to "staffing firms" or firms that are involved with hiring temporary staff. Any recruiting agency interested in being considered may contact our recruiting team at jensenhughesrecruiting.com.
Create a Job Alert
Interested in building your career at Jensen Hughes? Get future opportunities sent straight to your email.
Industrial Process Safety Consultant

Posted today
Job Viewed
Job Description
Baltimore, Maryland, United States; Blacksburg, Virginia, United States; Columbia, Maryland, United States; Fairfax, Virginia, United States; Rockville, Maryland, United States
**Company Overview**
Throughout our worldwide network of experts, clients and communities, we are renowned for our leadership in fire protection engineering - a legacy of responsibility we have proudly upheld since 1939. Today, our expertise extends broadly across closely related security and risk-based fields - from accessibility consulting and risk analysis to process safety, forensic investigations, security risk consulting, emergency management, digital innovation and more.
Our engineers and consultants collaborate to solve complex safety and security challenges, ensuring our clients can protect what matters most. For over 80 years, we have helped mitigate risks that threaten lives, property and reputations. Through technology, expertise and industry-leading research, we remain dedicated to our purpose of making our world safe, secure and resilient.
At Jensen Hughes, we believe that creating and sustaining a culture of trust, integrity and professional growth starts with putting our people first. Our employees are our greatest strength, and we value the unique perspectives and talents they bring to our organization.
Our wide range of Global Employee Networks connect people from across the organization, supporting career development and providing forums for individuals to share experiences on topics they're passionate about. Together, we are cultivating a connected culture where everyone has the opportunity to learn, grow and succeed together.
**Job Overview**
Jensen Hughes is seeking an Industrial and Process Safety Consultant to join our South Team with office locations in Baltimore, MD, Columbia, MD, Rockville, MD, Fairfax, VA and Blacksburg, VA. We are open to other locations and remote work for candidates with demonstrated experience and capability. A successful candidate will demonstrate ability to perform or direct engineering consulting services pertaining to process and material hazards in the industrial section. This market segment is a key growth area for our company and offers opportunities for increasing industry engagement, business development and mentorship of emerging professionals.
**Responsibilities**
+ Perform and manage engineering work associated with storage and use of flammable and combustible liquids, flammable gases, oxidizers, toxics, corrosives, and other hazardous materials
+ Conduct site inspections to observe existing operations at client facilities, perform engineering analyses, and recommend additions/revisions to client plans and procedures
+ Conduct site inspections to perform combustible Dust Hazard Analysis (DHA) and evaluate compliance with related industry standards
+ Conduct Process Hazard Analyses (PHAs) for unique, high-hazard and high-value industrial and manufacturing facilities
+ Perform Process Safety Management (PSM) system audits and support creation of PSM programs
+ Prepare hazardous materials inventory statements, hazardous materials management plans and similar documentation to fulfill requirements of codes, regulations, or insurance carriers
+ Develop explosion protection system designs and budgetary cost estimates
+ Conduct third-party review and acceptance testing of explosion protection systems
+ Conduct electrical classification assessments for NEC Chapter 5 compliance
+ Execute business development plans for clients, markets and sectors related to industrial and process safety consulting
+ Support multiple projects while meeting deadlines and working with a variety of personnel under a range of conditions
**Requirements and Qualifications**
+ High-level written and oral communication skills to do reports, correspondence, presentations, etc.
+ Demonstrated knowledge of engineering practices, process safety principles, and industry standards applying to combustible dust handling operations, including but not limited to:
+ NFPA standards 30, 70, 77, 400, 660
+ International Fire Code and NFPA 1
+ Knowledge of Instrumentation & Controls (safety instrumented systems) is desired but not required
+ Bachelor's Degree from four-year college and 3+ years of related experience. 5+ years of related experience preferred.
+ Professional Engineer (PE), Certified Safety Professional (CSP), Certified Industrial Hygienist (CIH), Institute of Safety and Health Management (ISHM) or comparable certification strongly preferred
+ Ability to travel up to 30% for project work
+ Ability to support multiple projects and effectively share workload with colleagues across regional and service line boundaries to fulfill client expectations.
#LI-AW1
#LI-Hybrid
#LI-Remote
**_Jensen Hughes is an Equal Opportunity Employer. Qualified candidates will receive consideration for employment without regard to race, color, religion, sex, national origin, sexual orientation, gender identity, disability or protected veteran status._**
The security of your personal data is important to us. Jensen Hughes has implemented reasonable physical, technical, and administrative security standards to protect personal data from loss, misuse, alteration, or destruction. We protect your personal data against unauthorized access, use, or disclosure, using security technologies and procedures, such as encryption and limited access. Only authorized individuals may access your personal data for the purpose for which it was collected, and these individuals receive training about the importance of protecting personal data. Jensen Hughes is committed to compliance with all relevant data privacy laws in all areas where we do business, including, but not limited to, the GDPR and the CCPA. Additionally, our service providers are contractually bound to maintain the confidentiality of personal data and may not use the information for any unauthorized purpose.
*Policy on use of 3rd party recruiting agency for direct placements
Jensen Hughes will occasionally augment a recruiting search through agencies for certain positions when business conditions warrant. Jensen Hughes will not accept resumes, inquiries or proposals from recruiting agencies as an acceptable method to consider a candidate. 3rd party recruiting agencies must sign a standard Jensen Hughes agreement after being evaluated and accepted by a Human Resources or Talent Acquisition manager, or member of the talent acquisition team. Hiring managers and employees of Jensen Hughes are not authorized to accept resumes, engage in fee-based searches through recruiting firms or sign a search agreement. Please note this policy does not apply to "staffing firms" or firms that are involved with hiring temporary staff. Any recruiting agency interested in being considered may contact our recruiting team at jensenhughesrecruiting.com.
Create a Job Alert
Interested in building your career at Jensen Hughes? Get future opportunities sent straight to your email.