40 Manufacturing Positions jobs in Rutherfordton
Manufacturing Technician
Posted 3 days ago
Job Viewed
Job Description
Your Career Begins at Timken
If you're ready for a challenging career that provides you with the ability to advance personally and professionally, look to Timken. Our associates make the world more productive by improving the efficiency and reliability of the machinery that keeps industry in motion.
Manufacturing Technician
Scope: Set-up and operate precision CNC machining equipment to produce ball bearing components.
This is a 2nd shift position, with regular hours of 3:00 p.m. to 11:00 p.m. Monday - Friday.
What We Offer
-
Competitive pay.
-
Comprehensive benefits package including medical, prescription drug, dental, and vision insurance.
-
Benefits start on first day of employment.
-
Opportunities for career advancement.
-
Supportive and team-oriented work environment.
-
Safe, clean, comfortable work environment.
Position Summary
Timken is looking for a skilled Machine Operator to set up, maintain, and operate production machinery. You'll ensure high productivity while meeting exacting safety and quality requirements. If you have a strong attention to detail and passion for ensuring quality output, we invite you to apply.
Position Responsibilities:
-
Setup and Operations - Set-up and operate production equipment including CNC lathes, honers, and bore grinders.
-
Gauging - Basic measurement of bearing geometry using state-of-the-art computer controlled gauging equipment as well as digital calipers, micrometers, metallurgical techniques, and dial indicators.
-
Quality through Process Control - Use process control techniques such as SPC, Histograms, Pareto analysis, etc. to understand and make adjustments to the manufacturing process. Emphasis placed on recognition, diagnosis and correction of out-of-control conditions. Will make quality checks to include concentricity, roundness, barreling, and eccentricity. Tolerancing up to and including .00050. Problem solve to achieve above tolerancing and quality.
-
Zone Control - sound ANDON to signal abnormal condition or problem. Problem solve to correct issue.
-
Maintenance - Monitor, clean, and inspect equipment to prevent problems before they occur, tied with routine maintenance of equipment and troubleshooting problems of minor to moderate complexity. Perform operator level Preventive Maintenance.
-
Material Handling - Move work in process to adjacent operations. Complete affiliated administrative flow requirements as needed.
-
Customer Focus - Achieve a clear understanding of the customer's (internal and external) technical requirements for each order. Responsible for assuring conformance to these requirements.
-
Team Participation - Collaborate with a variety of plant teams focused on continuous improvement. Occasionally serve as facilitator of such teams. Regularly rotate to other machines and assist team members in meeting Team Metrics.
-
Training - Continuously develop and upgrade training materials used to train other technicians, and occasionally assist in training.
-
Safety - Requires daily participation and involvement in individual and team safety responsibilities such as Behavior Based Safety, daily housekeeping, proper use of Personal Protective Equipment (PPE), and adherence to all safety requirements and policies.
-
Continuous Improvement - Generate and implement ideas for quality improvements and cost savings.
Basic Requirements:
-
Proven experience as a Machine Operator or similar role in a manufacturing environment.
-
Technical skills in machine operation and troubleshooting.
-
Ability to read blueprints, schematics, and manuals.
-
Physical stamina and strength to lift heavy materials and work in a fast-paced environment.
-
Attention to detail and quality-focused mindset.
-
High school diploma or GED.
All qualified applicants will receive consideration for employment without regard to race, color, religion, sex, national origin, protected veteran status, or disability status.
The Timken Company, a global technology leader in engineered bearings and industrial motion, designs a growing portfolio of next-generation products for diverse industries. For more than 125 years, Timken has used its specialized expertise to innovate and create customer-centric solutions that increase reliability and efficiency. The company posted $4.6 billion in sales in 2024 and employs more than 19,000 people globally, operating from 45 countries. Timken has been recognized among America's Most Responsible Companies and America's Greatest Workplaces for Diversity by Newsweek, the World's Most Ethical Companies® by Ethisphere and America's Most Innovative Companies by Fortune.
Why Choose Timken?
-
Over a century of knowledge and innovation
-
A culture of top performance
-
A global, diverse environment
-
Products that contribute to a sustainable world
-
A conviction to improve communities around us
-
Competitive salary and benefits
Not Ready To Apply?
Stay connected by joining our network and we'll keep you informed about upcoming events and opportunities that match your interests.
Talent Community
Nearest Major Market: Charlotte
Job Segment: CNC, Maintenance, Machinist, Industrial, Manufacturing
Manufacturing Engineer

Posted 10 days ago
Job Viewed
Job Description
Company Overview:
If a culture of excellence, innovation and ownership is what you're searching for, consider putting your experience in motion at Flowserve. As an individual contributor, or as a leader of people, your enterprise mindset will ensure Flowserve's position as the global standard in comprehensive flow control solutions. Here, your opportunity for professional development and industry leading rewards will be supported by our foundational commitments to the values of people first, integrity and safety. Thinking beyond opportunity and reward, at Flowserve, we are inspired by working together to create extraordinary flow control solutions to make the world better for everyone!
**Role Summary:**
The Manufacturing Engineer position addresses the day-to-day issues supporting production demands within the manufacturing facility. Responsibilities include process improvements, responding to technical challenges, dispositioning non-conforming product, general machine shop support, new equipment specification and implementation of manufacturing best practices. Individuals in these roles are involved in proactively creating accurate routings that are complete and reflect the customer's as well as code requirements. Interaction with production operators in manufacturing process methods and new testing criteria may be required.
**Responsibilities Include:**
+ Support company policies and procedures, goals and objectives, FDA regulations, and goods manufacturing practices. Beneficial Knowledge, Skills and Abilities: Knowledge of software used at facility including Microsoft Office products, Avante, Pro Engineer/Creo, SAP, Windchill, Solidworks, Esprit, Oracle, etc.
+ Participate and direct project activities such as Lean Manufacturing, Six Sigma activities to drive continuous improvement of operation performance. Maintenance of standard estimate system for product quoting and costing purposes. Capital expenditure projects, machine tool purchases, facility layout, and supporting key projects that help drive the business will be assigned as needed.
+ Work Environment: This position occasionally requires work near moving mechanical parts and/or exposure to fumes or airborne particles. Typical noise levels for this job are moderate.
+ Develop and implement process improvements which continuously improve the quality of the product manufactured in the shop, OTD, reduce operating & product costs, and reduce lead-times.
+ Collaborate with configuration control and design engineering regarding product tooling and design to ensure effectual production methods.
+ Work closely with manufacturing department to develop, coordinate, and implement technical training for employees.
+ Create tool drawings, design concepts, shop orders, and concepts in accordance with the R&D and quality assurance functions and maintain accurate documentation of such.
+ Provide engineering support in production department to troubleshoot and resolve technical problems.
+ Support quality testing processes and equipment including data acquisition, process measurements, and fixturing.
+ Assist engineering in providing accurate routings to the shop. This requires a working knowledge of materials, surface feet, speeds & feed.
+ Backup NC programming and support blank drawings for manufacturing.
+ Coordinate work with tool room/tool crib personnel, assigned technicians, and outside vendors.
+ Proficiently implementing Lean Manufacturing and Six Sigma techniques in a manufacturing environment (6S, Kaizen, Manufacturing Wastes, Cycle Time, etc.)
+ Support company policies and procedures, goals and objectives and good manufacturing practices.
**Requirements:**
+ Bachelor's degree (BS) in manufacturing or engineering from four-year college or university; or a minimum of 6 years related experience and/or training in parts manufacturing on standard and CNC controlled equipment.
+ Strong knowledge of preparing CNC programs using computer assisted techniques and manual definition.
+ Fanuc B-macro programming knowledge.
+ Essential Knowledge, Skills, and Abilities: Proficient in manufacturing engineering core subjects.
+ Computer-aided-drafting using Solidworks software. Geometric dimensioning and tolerancing.
+ Communicate professionally and with accepted business etiquette; work well with people in other departments and with customers.
+ Knowledge of manufacturing concepts.
+ Must be a good communicator.
+ Ability to prioritize multiple projects.
+ Enthusiastic, cooperative, and positive behavior.
+ Knowledge of manufacturing processes.
+ Knowledge and experience in applying Lean Manufacturing and Six Sigma methodologies.
**Preferred Skills / Experience:**
+ 5 years of direct manufacturing support experience
+ Exemplary communication skills
+ Strong problem solving experience
+ Self directed, task oriented
**Flowserve offers competitive pay, annual bonuses, medical benefits on day 1, generous paid vacation time, paid holidays, 401(k) and many other excellent benefits!**
**Req ID** : R-14947
**Job Family Group** : Engineering
**Job Family** : EN Engineering
EOE including Disability/Protected Veterans. Flowserve will also not discriminate against an applicant or employee for inquiring about, discussing or disclosing their pay or, in certain circumstances, the pay of their co-workers. Pay Transparency Nondiscrimination Provision
If you are a qualified individual with a disability or a disabled veteran, you have the right to request a reasonable accommodation if you are unable or limited in your ability to use or access flowservecareers.com as result of your disability. You can request a reasonable accommodation by sending an email to In order to quickly respond to your request, please use the words "Accommodation Request" as your subject line of your email. For more information, read the Accessibility Process.
Manufacturing Engineer

Posted 10 days ago
Job Viewed
Job Description
We are looking for a Manufacturing Engineer, to join our Shelby team!
As our Manufacturing Engineer you will write CNC programs using Siemens NX CAM. Your programming will consist of a high level of complexity; typically, programming for Machining Centers & Mills, but may include complex surface, and 5-axis tool paths. You will verify CNC programs using Vericut, create Renishaw probing routines and Macro B programs. You will also develop processes, routing, and tooling documentation. In addition, you will support projects improving operating income through projects to reduce cycle times, scrap, tooling costs and other related productivity areas. Other responsibilities include interfacing with design engineering in coordinating the release of new products, estimate manufacturing cost, and determines time standards. You will also have good written and oral communication skills.
**Location: Shelby, NC**
**We Take Care of Our People**
Paid Time Off **I** 401K with Employer Match and Profit Sharing **I** Health and Wellness Benefits **I** Learning and Development Opportunities **I** Referral Program **I** Competitive Pay **I** Recognition **I** Employee Stock Purchase Plan ( **I** Inclusive & Supportive Culture ( *
**Your Challenge**
+ Write CNC programs for Machining Centers and Mills using Siemens NX CAM, program verification using Vericut.
+ Create Renishaw probing routines and Macro B programs.
+ Tool selection, fixture design and provide technical support for machining processes.
+ Create and update manufacturing standard procedure, work instructions, which defines specific manufacturing processes.
+ Performs various operational or methods analyses related to labor standards and reviews product/project flow data, equipment, and labor requirements for use in conducting manufacturing operations, increasing productivity, and reducing production unit cost.
+ Assist in the evaluation of engineering changes and/or other specifications requirements and performs as technical liaison with other engineering personnel or program management, finance, design, quality, procurement, inspection, and production.
+ Interfaces with design engineering in coordinating the release of new products and conduct review of engineering drawings prior to release.
+ Provides technical support for plant layout, purchase of equipment, upgrade of equipment, feasibility studies.
**What You Bring**
+ Experience with CAM programming CNC multi (5)-axis machining centers and exotic materials, Siemens NX CAM preferred
+ CAD experience-- Siemens NX 12 preferred
+ Ability to design fixtures and tooling
+ Must be a US Person
+ Create set up and tooling documentation
+ Working knowledge of GDT and CMM inspection methods
+ Ability to read and understand drawings and specifications
+ Demonstrated mechanical and technical knowledge with the ability to resolve and provide technical solutions
+ Understanding of LEAN manufacturing concepts
+ MS Office working experience (Excel, Project, Word, PowerPoint, Exchange)
+ Excellent verbal and written communication skills and customer focus attitude
+ Bachelor's in mechanical engineering or equivalent work experience
**Who We Are**
Our Values ( Social and Governance
Curtiss-Wright Actuation Division designs, manufactures, and supports electro-mechanical actuation products and systems for use in demanding applications in Aerospace, Defense and Industrial Automation markets. Our market leading solutions help improve the reliability, efficiency and performance of our customers' operations and platforms, as well as reducing their environmental impact with energy efficient electro-mechanical designs and technology. For the Aerospace market, we supply actuation systems for flight control, landing gear, utility and other applications on both commercial and military aircraft. In Ground & Naval Defense markets, we support a wide array of applications ranging from door assist, ramp and hatch actuation, weapons handling systems, radar and launch platform actuation, and robotic (AUV/ROV) actuation.
To learn more, please visit us at About | Actuation Division | Curtiss-Wright (cw-actuation.com) ( note, benefits are country specific and may vary from location to location.
#LI-CM1
_No unsolicited agency submittals please. Agency partners must be invited to participate in a search by our_ **_Talent Acquisition Team ( )_** _and have signed terms in place prior to any submittal. Resumes submitted directly to any Curtiss-Wright employee or affiliate will not qualify for fee payment, and therefore become the property of Curtiss-Wright._
**Compliance Statement**
This position may require exposure to export-controlled information and subject to additional security screening. In the event information provided during the security screening reveals ineligibility to access export-controlled information, any offer of employment may be reconsidered or withdrawn.
Curtiss-Wright is an equal opportunity employer. All qualified applicants will receive consideration for employment without regard to race, ethnicity, color, sexual orientation, gender identity, physical or mental disability, age, ancestry, legally protected medical condition, family care status, marital status, religion, veteran status, national origin, or any other legally protected status. If you require accommodation during the recruitment process, please contact Talent Acquisition. ( )
**For US Applicants: EEO is The Law - click here for more information. ( you require accommodation due to a disability at any time during the recruitment and/or assessment process, please contact Talent Acquisition ( ) and we will make all reasonable efforts to accommodate your request.
**Join the WRIGHT Team!**
Over 95 years of growth, Curtiss-Wright is an integrated, market-facing global diversified industrial company and remains a technology leader through this legacy of innovation. Through three well-balanced segments - Aerospace & Industrial, Defense Electronics and Naval & Power, we remain focused on advanced technologies for high performance platforms and critical applications. Diversity, commitment to excellence and dedication to the spirit of pioneering innovation continue to drive the employees of Curtiss-Wright.
**Our Values**
What makes a world-class organization? It all begins with core values that provide a strong foundation for success. Simple in theory, the values of Curtiss-Wright are reflected in every aspect of our operations. To our employees, these are more than words on a wall - we all take these values to heart in our relationships with our customers and each other.
**Leadership**
We lead based on vision and strategic direction, empowering employees to reach goals through thoughtful and decisive action.
**Customer Focus**
We are committed to achieving total quality by meeting our customers' expectations and delivering products and services in a timely fashion.
**Teamwork & Trust**
Working in a spirit of trust and collaboration, we actively encourage employees to contribute their ideas and innovations to keep our company moving forward.
**Respect for People**
We believe that people are our most valuable asset and will always do the right thing in our dealings and interactions with all employees.
**Integrity**
We will act with the highest integrity in all of our business relationships and strategic partnerships.
**What We Offer Our Employees:**
**Opportunity:** As part of the Curtiss-Wright team, you have the opportunity each day to transform the way customers do business, as well as transform your career. Our entrepreneurial environment provides you with excellent experiences that enable you to develop your skills through stretch assignments and the opportunity to work with the best talent in the industry. You will have the opportunity to contribute from day one!
**Challenging Work:** The work we do here is not only challenging, but it is meaningful to our customers, our employees and the communities in which they live and work. You are given the chance to work on some of the most advanced technology projects in the world. Now that something to be proud of!
**Collaborative Environment:** The teamwork among our exceptionally talented people enables us to deliver some of the most advanced solutions to our customers.
Program Manager, Manufacturing
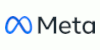
Posted 10 days ago
Job Viewed
Job Description
Manufacturing is a pillar within Meta's Delivery Team supporting data center construction. We exist to support the predictable delivery of capacity at scale through manufactured solutions.The Manufacturing Team's primary focus is supply chain engagement and optimization. We accept Manufacturing Informed Designed (MID) components and orchestrate their detailing and prototyping to optimum manufacturability then work with our partners in Delivery to plan logistics and integration to avoid challenges in construction.This team is comprised of strategic designers, strategic builders, tactical specialists, plus internal and external subject matter experts (SME) including preconstruction managers, contractors, schedulers, equipment reliability engineers, and sourcing specialists. This position will lead program management of all manufactured components in support of Meta's RPL project. This mega-project is of such scale that it requires a high-performing PM to drive strategic and tactical aspects of first-of-kind prototyping, logistics, and integration. Never before have we relied so heavily on offsite construction; a necessity here to deliver a project of this magnitude on an aggressive timeline. The successful candidate will be instrumental in ensuring the timely delivery of this capacity on what will be the largest project in Meta's history and one of a few of the largest data centers in the world.
**Required Skills:**
Program Manager, Manufacturing Responsibilities:
1. Program Management - Lead coordination, document, and anticipate program needs to ensure cost, schedule, and quality in concert with the mega-project construction
2. Primary Interface with the Manufacturing CAPs (Component Accountable PMs) - to coordinate on Supplier production (manufacturing execution) including configuring supply chain, production, scheduling, strategic inventory, logistics, and integration in collaboration with our delivery and quality teams
3. Interface with mega-project MOFE (Manufactured Owner Furnished Equipment) Onsite Logistics PM for logistical planning
4. Interface with mega-project MOFE Onsite Integration / Testing PM for planning and coordination
5. Manage GC (General Contractor) MOFE Coordinators for logistics, planning, coordination, reporting, lessons learned, etc.
6. Risk Matrix development, maintenance, and related reporting
7. Cost & Change Coordination with mega-project Meta designees including CM/PCA, ISCE, & MOFE CAPs
8. Schedule Development with Engineering/Scheduling, GCs, CAPs, & Suppliers
9. Regular Debriefs / Lessons Learned development, summary and communication to Engineering, Leadership, & XFNs (cross-functional partners)
10. Partner with cross functional teams on related efforts to ensure alignment and transparency across Design, Engineering, & Construction (DEC)
11. Partner closely with Sourcing Team for strategy and deployment of owner furnished equipment.
12. Partner with Global QA/QC Team to identify and strategically shift to the vendors and manufacturers, appropriate elements of the multi-trade integration and commissioning efforts to reduce onsite efforts. Your objective is to embed as much trade work and commissioning as is appropriate at the optimum points of fabrication from start through to the final point of integration.
13. Support team learning by bring lessons learned, vendors, new technology, and other topics to the group for exploration.
14. Travel approximately 40% Domestic Travel to construction and fabrication sites required (including minimal international travel as required)
**Minimum Qualifications:**
Minimum Qualifications:
15. Bachelor's degree or equivalent work experience in program management
16. 10+ years' experience in construction, manufacturing, and/or project planning
17. Experience in large scale construction management and/or scalable manufacturing
18. Manufacturing-for-construction background with understanding of lean manufacturing and supply-chain management plus knowledge of production machinery, processes, and standards in the field or industry experience with developing workflows and their associated flowcharts, schedules, and action plans
19. Experience building consensus and communicate effectively with a wide range of audiences (stakeholders to executive leadership).
20. Proven track record of adaptability and problem-solving in a dynamic work environment
21. Proficient working knowledge of Google Workspace and Bluebeam
**Preferred Qualifications:**
Preferred Qualifications:
22. Experience with off-site fabrication, pre-assembly and/or modularization of complex elements for construction (or off-shore) projects
23. Mission Critical, infrastructure, and/or data center construction experience
24. Experience working with blended architecture, engineering, manufacturing/assembly and construction teams
25. Software experience with eBuilder, Procore, Solidworks, Autodesk modeling software, Primavera P6, and/or BIM 360
26. Experience with LEAN tools (such as Choosing by Advantage, Last Planner/Pull Planning, Gemba, Kanban)
27. Experience working with Statistical Process Control (SPC), Just In Time (JIT) strategizing, and manufacturing data analytics.
28. PMP Certification
**Public Compensation:**
$144,000/year to $201,000/year + bonus + equity + benefits
**Industry:** Internet
**Equal Opportunity:**
Meta is proud to be an Equal Employment Opportunity and Affirmative Action employer. We do not discriminate based upon race, religion, color, national origin, sex (including pregnancy, childbirth, or related medical conditions), sexual orientation, gender, gender identity, gender expression, transgender status, sexual stereotypes, age, status as a protected veteran, status as an individual with a disability, or other applicable legally protected characteristics. We also consider qualified applicants with criminal histories, consistent with applicable federal, state and local law. Meta participates in the E-Verify program in certain locations, as required by law. Please note that Meta may leverage artificial intelligence and machine learning technologies in connection with applications for employment.
Meta is committed to providing reasonable accommodations for candidates with disabilities in our recruiting process. If you need any assistance or accommodations due to a disability, please let us know at
Manufacturing Quality Engineer
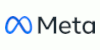
Posted 10 days ago
Job Viewed
Job Description
Meta Platforms, Inc. (Meta), formerly known as Facebook Inc., builds technologies that help people connect, find communities, and grow businesses. When Facebook launched in 2004, it changed the way people connect. Apps and services like Messenger, Instagram, and WhatsApp further empowered billions around the world. Now, Meta is moving beyond 2D screens toward immersive experiences like augmented and virtual reality to help build the next evolution in social technology. To apply, click "Apply to Job" online on this web page.
**Required Skills:**
Manufacturing Quality Engineer Responsibilities:
1. Develop the manufacturing and quality plans for cabling products for Meta's data centers, including copper, single mode fibre, and multimode fibre cabling, patch panels, cable runways, cable enclosures, and connectors.
2. Develop the manufacturing and quality plans for, IDC products such as Gen sets, Hot Aisle, Racks, UPS, PDUs, Busways, Load banks.
3. Evaluate manufacturing processes by applying knowledge of design, fabrication, assembly, tooling, and materials.
4. Participate in design reviews and provide feedback for DFM (design for manufacturability), DFT (design for testability), yield improvements, and quality control, and audit manufacturing sites to assess supplier's capabilities and implement manufacturing and quality best practices.
5. Drive Lean projects to improve manufacturing and data center processes to eliminate waste, reduce cost, and improve yield, and provide technical leadership and expertise within the supply chain teams during the hardware product lifecycle.
6. Ensure product and process quality targets are met by working with engineering to design test methods, establishing standards, and driving continuous improvement with manufacturers and equipment providers.
7. Improve manufacturing efficiency by analyzing and planning workflows, space requirements, and equipment layout, and prepare product and process reports by collecting, analyzing, and summarizing information and trends in manufacturing, field, and RMA data.
8. Knowledge of quality control techniques, including statistical process control (SPC), measurement system analysis (MSA), and failure mode and effects analysis (FMEA).
9. Knowledge of quality control techniques, including statistical process control (SPC), measurement system analysis (MSA), and failure mode and effects analysis (FMEA).
10. Familiarity with product lifecycle management (PLM) systems and enterprise resource planning (ERP) systems.
11. Experience in working with suppliers to ensure compliance to UL listing and EHS regulations.
12. Familiarity with quality management systems, such as ISO 9001 or similar standards.
13. Strong communication and negotiation skills to work with suppliers on resolving quality issues and improving performance.
14. Lead XFN Meta team and Manage supplier team for product delivery.
15. Telecommute from anywhere in the US permitted.
**Minimum Qualifications:**
Minimum Qualifications:
16. Requires a Master's degree in Computer Science, Electrical Engineering, Mechanical Engineering, or related field and 24 months of work experience in job offered or in a quality engineering-related occupation.
17. Requires 24 months of experience in the following:
18. 1. Driving root cause and corrective action for failures during manufacturing and operation
19. 2. Assisting in implementing failure analysis tools and processes
20. 3. Creating and maintaining all product process, quality, and technical training documentation, and BOMs
21. 4. Engineering change notifications, and manufacturing process changes through product lifecycle management tools
22. 5. PCBA assembly and test processes
23. 6. Conduct product quality reviews on all first of kind equipment
24. 7. Perform Supplier Quality management system Audit and manage the Supplier quality improvement plan and ensure corrective/preventive action implementation.
**Public Compensation:**
$215,433/year to $231,110/year + bonus + equity + benefits
**Industry:** Internet
**Equal Opportunity:**
Meta is proud to be an Equal Employment Opportunity and Affirmative Action employer. We do not discriminate based upon race, religion, color, national origin, sex (including pregnancy, childbirth, or related medical conditions), sexual orientation, gender, gender identity, gender expression, transgender status, sexual stereotypes, age, status as a protected veteran, status as an individual with a disability, or other applicable legally protected characteristics. We also consider qualified applicants with criminal histories, consistent with applicable federal, state and local law. Meta participates in the E-Verify program in certain locations, as required by law. Please note that Meta may leverage artificial intelligence and machine learning technologies in connection with applications for employment.
Meta is committed to providing reasonable accommodations for candidates with disabilities in our recruiting process. If you need any assistance or accommodations due to a disability, please let us know at
Program Manager, Manufacturing

Posted 10 days ago
Job Viewed
Job Description
Manufacturing is a pillar within Meta's Delivery Team supporting data center construction. We exist to support the predictable delivery of capacity at scale through manufactured solutions.The Manufacturing Team's primary focus is supply chain engagement and optimization. We accept Manufacturing Informed Designed (MID) components and orchestrate their detailing and prototyping to optimum manufacturability then work with our partners in Delivery to plan logistics and integration to avoid challenges in construction.This team is comprised of strategic designers, strategic builders, tactical specialists, plus internal and external subject matter experts (SME) including preconstruction managers, contractors, schedulers, equipment reliability engineers, and sourcing specialists. This position will lead program management of all manufactured components in support of Meta's RPL project. This mega-project is of such scale that it requires a high-performing PM to drive strategic and tactical aspects of first-of-kind prototyping, logistics, and integration. Never before have we relied so heavily on offsite construction; a necessity here to deliver a project of this magnitude on an aggressive timeline. The successful candidate will be instrumental in ensuring the timely delivery of this capacity on what will be the largest project in Meta's history and one of a few of the largest data centers in the world.
**Required Skills:**
Program Manager, Manufacturing Responsibilities:
1. Program Management - Lead coordination, document, and anticipate program needs to ensure cost, schedule, and quality in concert with the mega-project construction
2. Primary Interface with the Manufacturing CAPs (Component Accountable PMs) - to coordinate on Supplier production (manufacturing execution) including configuring supply chain, production, scheduling, strategic inventory, logistics, and integration in collaboration with our delivery and quality teams
3. Interface with mega-project MOFE (Manufactured Owner Furnished Equipment) Onsite Logistics PM for logistical planning
4. Interface with mega-project MOFE Onsite Integration / Testing PM for planning and coordination
5. Manage GC (General Contractor) MOFE Coordinators for logistics, planning, coordination, reporting, lessons learned, etc.
6. Risk Matrix development, maintenance, and related reporting
7. Cost & Change Coordination with mega-project Meta designees including CM/PCA, ISCE, & MOFE CAPs
8. Schedule Development with Engineering/Scheduling, GCs, CAPs, & Suppliers
9. Regular Debriefs / Lessons Learned development, summary and communication to Engineering, Leadership, & XFNs (cross-functional partners)
10. Partner with cross functional teams on related efforts to ensure alignment and transparency across Design, Engineering, & Construction (DEC)
11. Partner closely with Sourcing Team for strategy and deployment of owner furnished equipment.
12. Partner with Global QA/QC Team to identify and strategically shift to the vendors and manufacturers, appropriate elements of the multi-trade integration and commissioning efforts to reduce onsite efforts. Your objective is to embed as much trade work and commissioning as is appropriate at the optimum points of fabrication from start through to the final point of integration.
13. Support team learning by bring lessons learned, vendors, new technology, and other topics to the group for exploration.
14. Travel approximately 40% Domestic Travel to construction and fabrication sites required (including minimal international travel as required)
**Minimum Qualifications:**
Minimum Qualifications:
15. Bachelor's degree or equivalent work experience in program management
16. 10+ years' experience in construction, manufacturing, and/or project planning
17. Experience in large scale construction management and/or scalable manufacturing
18. Manufacturing-for-construction background with understanding of lean manufacturing and supply-chain management plus knowledge of production machinery, processes, and standards in the field or industry experience with developing workflows and their associated flowcharts, schedules, and action plans
19. Experience building consensus and communicate effectively with a wide range of audiences (stakeholders to executive leadership).
20. Proven track record of adaptability and problem-solving in a dynamic work environment
21. Proficient working knowledge of Google Workspace and Bluebeam
**Preferred Qualifications:**
Preferred Qualifications:
22. Experience with off-site fabrication, pre-assembly and/or modularization of complex elements for construction (or off-shore) projects
23. Mission Critical, infrastructure, and/or data center construction experience
24. Experience working with blended architecture, engineering, manufacturing/assembly and construction teams
25. Software experience with eBuilder, Procore, Solidworks, Autodesk modeling software, Primavera P6, and/or BIM 360
26. Experience with LEAN tools (such as Choosing by Advantage, Last Planner/Pull Planning, Gemba, Kanban)
27. Experience working with Statistical Process Control (SPC), Just In Time (JIT) strategizing, and manufacturing data analytics.
28. PMP Certification
**Public Compensation:**
$144,000/year to $201,000/year + bonus + equity + benefits
**Industry:** Internet
**Equal Opportunity:**
Meta is proud to be an Equal Employment Opportunity and Affirmative Action employer. We do not discriminate based upon race, religion, color, national origin, sex (including pregnancy, childbirth, or related medical conditions), sexual orientation, gender, gender identity, gender expression, transgender status, sexual stereotypes, age, status as a protected veteran, status as an individual with a disability, or other applicable legally protected characteristics. We also consider qualified applicants with criminal histories, consistent with applicable federal, state and local law. Meta participates in the E-Verify program in certain locations, as required by law. Please note that Meta may leverage artificial intelligence and machine learning technologies in connection with applications for employment.
Meta is committed to providing reasonable accommodations for candidates with disabilities in our recruiting process. If you need any assistance or accommodations due to a disability, please let us know at
Manufacturing Quality Engineer

Posted 10 days ago
Job Viewed
Job Description
Meta Platforms, Inc. (Meta), formerly known as Facebook Inc., builds technologies that help people connect, find communities, and grow businesses. When Facebook launched in 2004, it changed the way people connect. Apps and services like Messenger, Instagram, and WhatsApp further empowered billions around the world. Now, Meta is moving beyond 2D screens toward immersive experiences like augmented and virtual reality to help build the next evolution in social technology. To apply, click "Apply to Job" online on this web page.
**Required Skills:**
Manufacturing Quality Engineer Responsibilities:
1. Develop the manufacturing and quality plans for cabling products for Meta's data centers, including copper, single mode fibre, and multimode fibre cabling, patch panels, cable runways, cable enclosures, and connectors.
2. Develop the manufacturing and quality plans for, IDC products such as Gen sets, Hot Aisle, Racks, UPS, PDUs, Busways, Load banks.
3. Evaluate manufacturing processes by applying knowledge of design, fabrication, assembly, tooling, and materials.
4. Participate in design reviews and provide feedback for DFM (design for manufacturability), DFT (design for testability), yield improvements, and quality control, and audit manufacturing sites to assess supplier's capabilities and implement manufacturing and quality best practices.
5. Drive Lean projects to improve manufacturing and data center processes to eliminate waste, reduce cost, and improve yield, and provide technical leadership and expertise within the supply chain teams during the hardware product lifecycle.
6. Ensure product and process quality targets are met by working with engineering to design test methods, establishing standards, and driving continuous improvement with manufacturers and equipment providers.
7. Improve manufacturing efficiency by analyzing and planning workflows, space requirements, and equipment layout, and prepare product and process reports by collecting, analyzing, and summarizing information and trends in manufacturing, field, and RMA data.
8. Knowledge of quality control techniques, including statistical process control (SPC), measurement system analysis (MSA), and failure mode and effects analysis (FMEA).
9. Knowledge of quality control techniques, including statistical process control (SPC), measurement system analysis (MSA), and failure mode and effects analysis (FMEA).
10. Familiarity with product lifecycle management (PLM) systems and enterprise resource planning (ERP) systems.
11. Experience in working with suppliers to ensure compliance to UL listing and EHS regulations.
12. Familiarity with quality management systems, such as ISO 9001 or similar standards.
13. Strong communication and negotiation skills to work with suppliers on resolving quality issues and improving performance.
14. Lead XFN Meta team and Manage supplier team for product delivery.
15. Telecommute from anywhere in the US permitted.
**Minimum Qualifications:**
Minimum Qualifications:
16. Requires a Master's degree in Computer Science, Electrical Engineering, Mechanical Engineering, or related field and 24 months of work experience in job offered or in a quality engineering-related occupation.
17. Requires 24 months of experience in the following:
18. 1. Driving root cause and corrective action for failures during manufacturing and operation
19. 2. Assisting in implementing failure analysis tools and processes
20. 3. Creating and maintaining all product process, quality, and technical training documentation, and BOMs
21. 4. Engineering change notifications, and manufacturing process changes through product lifecycle management tools
22. 5. PCBA assembly and test processes
23. 6. Conduct product quality reviews on all first of kind equipment
24. 7. Perform Supplier Quality management system Audit and manage the Supplier quality improvement plan and ensure corrective/preventive action implementation.
**Public Compensation:**
$215,433/year to $231,110/year + bonus + equity + benefits
**Industry:** Internet
**Equal Opportunity:**
Meta is proud to be an Equal Employment Opportunity and Affirmative Action employer. We do not discriminate based upon race, religion, color, national origin, sex (including pregnancy, childbirth, or related medical conditions), sexual orientation, gender, gender identity, gender expression, transgender status, sexual stereotypes, age, status as a protected veteran, status as an individual with a disability, or other applicable legally protected characteristics. We also consider qualified applicants with criminal histories, consistent with applicable federal, state and local law. Meta participates in the E-Verify program in certain locations, as required by law. Please note that Meta may leverage artificial intelligence and machine learning technologies in connection with applications for employment.
Meta is committed to providing reasonable accommodations for candidates with disabilities in our recruiting process. If you need any assistance or accommodations due to a disability, please let us know at
Be The First To Know
About the latest Manufacturing positions Jobs in Rutherfordton !
Open Positions - Food Manufacturing
Posted 2 days ago
Job Viewed
Job Description
Are you passionate about food production, quality, and innovation? We're looking for dedicated individuals to fill multiple roles at our brand new food manufacturing facility.
Be part of something delicious - whether you're just starting your career or bringing a wealth of experience, there's a place for YOU on our team.
Why Work at Wow Bao?
- Competitive pay rate starting at $17.00 an hour
- Benefits - medical, dental, vision
- Paid Time Off
- 401(k) Retirement
- Monday through Friday operations (no weekends)
- Hiring First Shift (8 hours), Monday to Friday
- Brand new facility, be part of this exciting opportunity!
In the meantime, if you have any questions, feel free to contact our Human Resources team at -we're happy to assist!
Thank you for your interest in joining our team-we look forward to connecting soon!
ABOUT WOW BAO
At Wow Bao, we believe that life is too short for uninspired food. We're here to transform the Asian Street Food experience from every day and expected to extraordinary and inventive. Wow Bao is the fastest growing Frozen Asian Snack brand in the United States growing retail sales over 370% in 2024. Through strategic relationships with retail partners Wow Bao is now available in over 15,000 grocery stores nationwide!
Wow Bao has a long history of manufacturing restaurant quality food, that started in 2003 when the first Wow Bao restaurant location was opened. Today, our omni-channel brand operates several Chicago restaurants, airports, virtual kitchens, and universities. Wow Bao is poised for continued growth within all its verticals, as well as in the corporate setting.
Wow Bao is the only brand to be recognized three times by Fast Casual magazine as a Top 100 Movers & Shaker. Ranked no. 1 in 2019 and 2022 and no. 4 in 2023, we are the only brand to have the honor more than once.
WE FOSTER A CULTURE OF CARING
At Wow Bao, every team member leads from a place of care. Whether it's our guests or employees, we put people first. We strive to inspire, motivate, and appreciate one another every day. We live by the golden rule and treat everyone with kindness, empathy, respect, and a healthy dose of humor. We take our work, not ourselves, seriously.
Wow Bao is an Equal Opportunity Employer
Requirements
- Must be able to access and navigate all areas of the production facility
- Frequent standing, walking, bending, and lifting up to 50 pounds at a time
- Ability to work in various environments including cold environments for extended periods
- Use of protective equipment such as gloves, safety glasses, and ear protection
- Health Insurance (medical, dental, vision)
- 401(k) Retirement Plan
- Voluntary life insurance
- Voluntary disability insurance
- Paid Time Off
- Employee Discount Programs with Perkspot and Working Advantage
- We foster a culture of CARE
Senior Client Manager (Manufacturing)

Posted 10 days ago
Job Viewed
Job Description
Join a company that is pushing the boundaries of what is possible. We are renowned for our technical excellence and leading innovations, and for making a difference to our clients and society. Our workplace embraces diversity and inclusion - it's a place where you can grow, belong and thrive.
**Your day at NTT DATA**
The Senior Client Manager is an advanced subject matter expert. This is a quota-bearing sales persona, and the primary responsibility of the role is to take full ownership of assigned accounts, retain these clients and find new business.
The focus of this role is to manage and grow relationships in order to drive land, expansion and renewals across all solutions within assigned accounts.
The Senior Client Manager is required to pursue leads identified by aligned lead generation representatives/business development representatives.
**What you'll be doing**
**In this role you will:**
+ Manages and grows relationships to drive land, expansion and renewals across all solutions within assigned accounts.
+ Pursues leads identified by aligned Lead Generation/Business Development Representatives.
+ Minimizes churn and maximizes retention in assigned accounts.
+ Drives client satisfaction throughout the entire lifecycle of the clients' buying process.
+ Generates demand by assisting clients to identify current needs and then effectively articulate how the company can add value through its services and solutions.
+ Influences and works closely with vendors/partners to achieve required results.
+ Uses company sales tools and methodology to effectively manage accounts, opportunities, pipelines and forecast.
+ Develops open and effective channels of communication in with each client within the assigned account.
+ Encourages revenue growth by inspiring clients to additional services.
+ Becomes the reliable point of contact for clients that is required to establish a strong business relationship.
+ Takes ownership of a range of accounts within the assigned segments.
+ Determines the best solution requirements for each client that can be deployed by other departments.
+ Builds enduring relationships and display an understanding of the client industry, business environment and strategy to identify current and future opportunities for the organization.
+ Develops and/or aligns governance and compliance policies in own practice area to identify and manage risk exposure liability.
+ Monitors and controls financial governance and compliance throughout an area of specialization in order to manage financial cost.
**This role is perfect for you if you:**
+ Sales business acumen. The skills supporting successful selling through organizational and business outcome mindset. Success will require focusing on planning, leveraging tools and data, and concentrating on company business requirements. Developing the skills to understand the client's business (including commercial and financial aspects) in order to bring value to them from the company's portfolio of services.
+ Sales client engagement and management. The skills used to effectively manage and analyze the client throughout the client lifecycle, with the goal of improving client relationships and driving sales growth. Success will require detailed understanding of client needs, effective sales planning, and building trust, all while managing to client expectations. Developing the skills required to know the client, building effective and lasting relationships with them and to be seen as a trusted advisor.
+ Sales solution skills. The knowledge of the company's offerings, client applications, use cases and market trends and the skill to apply them to individual client and prospect situations that positions the sales team member as an expert client advisor. Success will require the ability to link company offerings, including high-value services to specific client and prospect needs and outcomes.
+ Sales pursuit. The skills and knowledge that enable a sales team member to create success by identifying and advancing opportunities at assigned prospects and clients. Success will require both individual ownership as well as accountability for coordinating internal and external resources in order to close sales opportunities.
+ Bachelor's degree or equivalent in business or a sales related field.
+ Relevant vendor certifications would be advantageous.
+ Advanced experience in a global partner management role.
+ Advanced experience in a sales environment and/or customer service role.
+ Advanced experience in the IT or professional services industry with a focus on business development and/or sales.
+ Advanced experience in driving alignment to a common vision and working across multiple stakeholders to achieve sales growth.
+ Advanced sales orientation with experience working with clients and business teams to create sales-orientated solutions and services.
+ Advanced experience gained in a similar client manager role.
+ Advanced experience working with Salesforce.com contact platform.
**Workplace type** **:**
Remote Working
**About NTT DATA**
NTT DATA is a $30+ billion trusted global innovator of business and technology services. We serve 75% of the Fortune Global 100 and are committed to helping clients innovate, optimize and transform for long-term success. We invest over $3.6 billion each year in R&D to help organizations and society move confidently and sustainably into the digital future. As a Global Top Employer, we have diverse experts in more than 50 countries and a robust partner ecosystem of established and start-up companies. Our services include business and technology consulting, data and artificial intelligence, industry solutions, as well as the development, implementation and management of applications, infrastructure, and connectivity. We are also one of the leading providers of digital and AI infrastructure in the world. NTT DATA is part of NTT Group and headquartered in Tokyo.
**Equal Opportunity Employer**
NTT DATA is proud to be an Equal Opportunity Employer with a global culture that embraces diversity. We are committed to providing an environment free of unfair discrimination and harassment. We do not discriminate based on age, race, colour, gender, sexual orientation, religion, nationality, disability, pregnancy, marital status, veteran status, or any other protected category. Join our growing global team and accelerate your career with us. Apply today.
Manufacturing Engineering Program Manager

Posted 10 days ago
Job Viewed
Job Description
As part of our Manufacturing Engineering Project team, the primary function of this position will be to drive the development and execution of corporate strategy and innovation capital projects for Keurig Dr Pepper manufacturing locations. This position will build and manage relationships of internal and external resources to effectively implement project initiatives that drive productivity results, optimize value, and promote growth. This role interacts with individuals from Strategy, Operations, Engineering, Commercial, Beverage Initiatives, and other key Business Units within Keurig Dr Pepper. This role will also work directly with manufacturing sites to develop, modify, and implement plans for capacity and program initiatives.
The ideal candidate will have a bachelor's degree in Mechanical, Electrical, Industrial, or a related Engineering discipline. This individual will also have experience in developing and executing capital projects in a manufacturing environment. A candidate with Food and Beverage or CPG (Consumer Package Goods) and plant production line experience is considered a plus. Knowledge of high-speed filling, packaging technologies are ideal areas of expertise. PMP Certified, lean methodologies, TPM, and knowledge of key standard work processes are also essential qualities.
Join our flexible team at Keurig Dr Pepper and make a difference by being a part of the safest, most sustainable, agile, and productive value chain in the beverage industry!
**Responsibilities -**
Technical Services:
+ Collaborate and drive network and plant strategies for capacity growth, productivity, and innovation
+ Approval of equipment design, development, and execution
+ Define performance criteria, develop timelines, and estimate capital budgets
+ Define key process parameters and testing methods with the Packaging Engineering team
+ Write and execute equipment specification; provide input on specification platform/management
+ Write and execute SAT's and FAT's
+ Provide technical project assistance to project managers and plant personnel
+ Must have strong knowledge management and communication skills
+ Ability to perform statistical analysis is a plus
+ Familiarity with 2D & 3D cad is a plus
Project Management:
+ Capital project process design, development, and execution from concept through closure
+ Provide regular project communication to KDP Leadership and project stakeholders
+ Drive optimization of vertical startup methodology on all projects
+ Ownership of project budget development and execution
+ Ownership of project timelines
+ Ownership and execution of project change management
+ Ownership and storage of all project/knowledge-based information
+ Drive TOB and SOT development with Procurement and Legal
+ Assist with FAT/SAT development and execution
+ Make methodical fact-based, data driven decisions to ensure project success
+ Identify, develop, and execute cost savings programs to support business productivity metrics
+ Drive lean and standard work principles to ensure team/department efficiencies
+ Build strategic relationships and communications with internal customers, stakeholders, and external Partners
**Travel -** This individual will travel primarily to U.S. operations and possibly internationally for equipment FAT's - up to 50% maximum. We work hard to operate remotely as much as possible and to reduce unnecessary travel.
**Ensure high performance results of your team by:**
+ Fostering a culture of trust and wellbeing that prioritizes the team and values employee contributions
+ Driving a shared vision with clear goals and accountability, supported by regular conversations to maximize talent
+ Embracing diverse perspectives to foster innovation, learning from both successes and failures
+ Establishing a safe environment where team members are motivated, heard, and aligned with clear expectations
It is unlawful in Massachusetts to require or administer a lie detector test as a condition of employment or continued employment. An employer who violates this law shall be subject to criminal penalties and civil liability.
**Total Rewards:**
+ Salary Range: $91,300- $150,000 / year.
+ Actual placement within the compensation range may vary depending on experience, skills, and other factors
+ Benefits, subject to election and eligibility: Medical, Dental, Vision, Disability, Paid Time Off (including paid parental leave, vacation, and sick time), 401k with company match, Tuition Reimbursement, and Mileage Reimbursement
+ Annual bonus based on performance and eligibility
**Requirements:**
+ Bachelor's Degree in Mechanical, Electrical, Industrial, or related engineering discipline required
+ Master's degree is a plus
+ 5+ years of capital engineering project-based experience required
+ Knowledge of primary packaging equipment and materials/processes (fillers, plastics, aluminum, bottles, cans, caps/closures) required
+ Knowledge of secondary/tertiary packaging equipment (cartoners, case packers, palletizers) required
+ Knowledge of plant infrastructure and operations required
+ Experience with technologies including CSD, Juices and Teas, Aseptic, hot fill highly preferred
+ Strong leadership skills and self-motivation; ability to work independently
+ Strong process and communications skills
**Company Overview:**
Keurig Dr Pepper (NASDAQ: KDP) is a leading beverage company in North America, with a portfolio of more than 125 owned, licensed and partners brands and powerful distribution capabilities to provide a beverage for every need, anytime, anywhere. We operate with a differentiated business model and world-class brand portfolio, powered by a talented and engaged team that is anchored in our values. We work with big, exciting beverage brands and the #1 single-serve coffee brewing system in North America at KDP, and we have fun doing it!
Together, we have built a leading beverage company in North America offering hot and cold beverages together at scale. Whatever your area of expertise, at KDP you can be a part of a team that's proud of its brands, partnerships, innovation, and growth. Will you join us?
We strive to be an?employer of choice ( , providing a culture and opportunities that empower our team of ~29,000 employees to grow and develop. We offer robust benefits to support your health and wellness as well as your personal and financial well-being. We also provide employee programs designed to enhance your professional growth and development, while ensuring you feel valued, inspired and appreciated at work.
Keurig Dr Pepper is an equal opportunity employer and affirmatively seeks diversity in its workforce. Keurig Dr Pepper recruits qualified applicants and advances in employment its employees without regard to race, color, religion, gender, sexual orientation, gender identity, gender expression, age, disability or association with a person with a disability, medical condition, genetic information, ethnic or national origin, marital status, veteran status, or any other status protected by law.
Keurig Dr Pepper is an equal opportunity employer and affirmatively seeks diversity in its workforce. Keurig Dr Pepper recruits qualified applicants and advances in employment its employees without regard to race, color, religion, gender, sexual orientation, gender identity, gender expression, age, disability or association with a person with a disability, medical condition, genetic information, ethnic or national origin, marital status, veteran status, or any other status protected by law.