84 Manufacturing jobs in Canal Winchester
Manufacturing Quality Control Inspector
Posted 15 days ago
Job Viewed
Job Description
Key Responsibilities:
- Perform visual and dimensional inspections of raw materials, in-process components, and finished products using precision measuring tools (e.g., calipers, micrometers, gauges).
- Read and interpret blueprints, engineering drawings, and specifications to ensure product compliance.
- Document inspection results accurately, including identification of non-conformances and recommended corrective actions.
- Collaborate with production teams to address quality issues and implement preventive measures.
- Conduct first-piece, in-process, and final inspections according to established quality procedures.
- Maintain calibration records for inspection equipment and ensure all tools are in proper working order.
- Participate in root cause analysis for quality deviations and support continuous improvement initiatives.
- Generate quality reports and communicate findings to production management and engineering teams.
- Adhere to all company quality management systems (e.g., ISO 9001) and safety regulations.
Qualifications:
- High school diploma or equivalent; associate's degree in a technical field or relevant certification (e.g., ASQ Certified Quality Inspector) is a plus.
- Minimum of 2-4 years of experience in quality control or inspection within a manufacturing environment.
- Proficiency in reading blueprints, schematics, and technical specifications.
- Expertise in using various precision measuring instruments.
- Strong attention to detail and excellent observational skills.
- Basic computer skills for data entry and report generation.
- Ability to work independently and as part of a team in a fast-paced production environment.
- Knowledge of quality management systems (e.g., ISO 9001) and quality tools (e.g., SPC, 5S) is desirable.
- Strong problem-solving skills and a commitment to continuous improvement.
This is a valuable opportunity to join a growing manufacturing company in Columbus, Ohio that prides itself on product excellence. Our client offers a competitive hourly wage, comprehensive benefits, and a stable work environment with opportunities for professional development. If you are a detail-oriented professional with a passion for quality, we encourage you to apply and help our client maintain their reputation for superior products.
Manufacturing - Digital Manufacturing, Manager

Posted 9 days ago
Job Viewed
Job Description
**Industry/Sector:** Not Applicable
**Time Type:** Full time
**Travel Requirements:** Up to 60%
At PwC, our people in operations consulting specialise in providing consulting services on optimising operational efficiency and effectiveness. These individuals analyse client needs, develop operational strategies, and offer guidance and support to help clients streamline processes, improve productivity, and drive business performance.
In product development and manufacturing at PwC, you will specialise in improving product development and manufacturing processes. You will work closely with clients to analyse product development lifecycles, identify bottlenecks, and develop strategies to enhance speed to market, reduce costs, and improve quality. Working in this area, you will also provide guidance on implementing lean manufacturing principles, optimising supply chain integration, and leveraging digital technologies.
Enhancing your leadership style, you motivate, develop and inspire others to deliver quality. You are responsible for coaching, leveraging team member's unique strengths, and managing performance to deliver on client expectations. With your growing knowledge of how business works, you play an important role in identifying opportunities that contribute to the success of our Firm. You are expected to lead with integrity and authenticity, articulating our purpose and values in a meaningful way. You embrace technology and innovation to enhance your delivery and encourage others to do the same.
Examples of the skills, knowledge, and experiences you need to lead and deliver value at this level include but are not limited to:
+ Analyse and identify the linkages and interactions between the component parts of an entire system.
+ Take ownership of projects, ensuring their successful planning, budgeting, execution, and completion.
+ Partner with team leadership to ensure collective ownership of quality, timelines, and deliverables.
+ Develop skills outside your comfort zone, and encourage others to do the same.
+ Effectively mentor others.
+ Use the review of work as an opportunity to deepen the expertise of team members.
+ Address conflicts or issues, engaging in difficult conversations with clients, team members and other stakeholders, escalating where appropriate.
+ Uphold and reinforce professional and technical standards (e.g. refer to specific PwC tax and audit guidance), the Firm's code of conduct, and independence requirements.
Our Product Development & Manufacturing (PD&M) Team helps our clients leverage advanced strategies, operational approaches and technologies to innovate, develop and manufacture products and services in a manner that significantly increases operational efficiency and drives new levels of enterprise-wide growth in a connected world.
**Job Requirements and Preferences** :
**Basic Qualifications** :
**Minimum Degree Required** :
Bachelor Degree
**Minimum Years of Experience** :
5 year(s)
**Preferred Qualifications** :
**Degree Preferred** :
Master Degree
**Preferred Fields of Study** :
Aerospace Engineering, Automotive Engineering, Biomedical Engineering, Chemical Engineering, Computer Engineering, Engineering, Engineering Mechanics, Engineering Physics, Industrial and Operations Engineering, Industrial Engineering, Materials Science and Engineering, Mechanical Engineering, Production Engineering, Project Engineering & Management, Biomedical Science, Computer and Information Science, Data Processing/Analytics/Science
**Preferred Knowledge/Skills** :
Demonstrates extensive knowledge and experience with and a proven record of success in leading or facilitating project management or client consultations in the areas of product development and manufacturing, preferably for a global network of professional services firms, in one of the following core industry sectors including, but not limited to:
+ Industrial: Automotive; Aerospace; Chemicals; Industrial Manufacturing; or, Construction;
+ Technology: Hardware/Electronics; Systems; Software; Semiconductor; or, Telecommunications;
+ Life Sciences: Pharma, Bio Pharma, & Specialty Pharma; Medical Device, Medical Technology & Diagnostics; Generics; or, Animal Health; and,
+ Consumer Markets: Food & Beverage; Goods; or, Vertically Integrated Retail.
Functional Experience:
Demonstrates extensive knowledge and experience with and a proven record of success to deliver advisory services in the following capability areas:
+ Digital Manufacturing Application (MES, CMMS, QMS) Configuration and/or Deployment;
+ Digital Twin;
+ Digital Manufacturing Strategy Development;
+ Digital Manufacturing Blueprint & Design;
+ Digital Manufacturing Control Systems Design & Deployment;
+ Manufacturing Decision Support & Analytics;
+ Machine Connectivity; and,
+ Industrial IoT and Cloud Solutions.
Demonstrates extensive knowledge and experience with and a proven record of success to deliver advisory services in the following capability areas:
+ Manufacturing Strategy & Operations;
+ Operations Excellence;
+ Maintenance & Reliability Management; and,
+ Digital Automation.
Demonstrates extensive abilities to lead and manage a diverse team including:
+ Demonstrates the ability to build, maintain, and utilize networks of client relationships;
+ Possesses advanced problem solving and analysis skills;
+ Possesses advanced spreadsheet, presentation and document development skills;
+ Possesses detailed value case development skills;
+ Possesses the ability to interpret financial statements;
+ Possesses engaging interpersonal skills;
+ Possesses a collaborative and 'can-do' mindset;
+ Possesses financial modeling skills;
+ Possesses the ability to influence and shape thinking of peer level and Director level client resources;
+ Possesses Program/Project leadership skills - ability to lead complex multi-workstream projects;
+ Effectively manages unstructured situations, anticipating client needs and developing solutions;
+ Possesses the ability to develop/coach resources and guide careers of team members;
+ Possesses client presentation skills; and,
+ Possesses proposal & pricing development skills.
Learn more about how we work: does not intend to hire experienced or entry level job seekers who will need, now or in the future, PwC sponsorship through the H-1B lottery, except as set forth within the following policy: PwC is an?equal opportunity employer, all qualified applicants will receive consideration for employment at PwC without regard to race; color; religion; national origin; sex (including pregnancy, sexual orientation, and gender identity); age; disability; genetic information (including family medical history); veteran, marital, or citizenship status; or, any other status protected by law?
For only those qualified applicants that are impacted by the Los Angeles County Fair Chance Ordinance for Employers, the Los Angeles' Fair Chance Initiative for Hiring Ordinance, the San Francisco Fair Chance Ordinance, San Diego County Fair Chance Ordinance, and the California Fair Chance Act, where applicable, arrest or conviction records will be considered for Employment in accordance with these laws. At PwC, we recognize that conviction records may have a direct, adverse, and negative relationship to responsibilities such as accessing sensitive company or customer information, handling proprietary assets, or collaborating closely with team members. We evaluate these factors thoughtfully to establish a secure and trusted workplace for all.
Applications will be accepted until the position is filled or the posting is removed, unless otherwise set forth on the following webpage. Please visit this link for information about anticipated application deadlines: salary range for this position is: $99,000 - $232,000, plus individuals may be eligible for an annual discretionary bonus. For roles that are based in Maryland, this is the listed salary range for this position. Actual compensation within the range will be dependent upon the individual's skills, experience, qualifications and location, and applicable employment laws. PwC offers a wide range of benefits, including medical, dental, vision, 401k, holiday pay, vacation, personal and family sick leave, and more. To view our benefits at a glance, please visit the following link:
Buyer - Manufacturing
Posted 19 days ago
Job Viewed
Job Description
Job Description:Overview:We are looking for an experienced Buyer for Manufacturing in our Columbus, OH headquarters. The Buyer - Manufacturing is directly responsible for the supplier relationship management process related to Rogue Fitness's manufacturing operations. Procurement of raw materials, components, subassemblies and services are the core responsibilities.The Buyer - Manufacturing is a fully onsite role in Columbus, Ohio. Remote work is not available.Applicants must be authorized to work in the United States for any employer.Responsibilities:Analyze Rogue inventory and demand for manufacturing components to drive and execute purchasing decisionsIdentify and evaluate potential suppliersSourcing for multiple commodities (i.e. Plastics, Steel, Aluminum, Services, Etc)Ensures products and services are secured at cost, quality, and competitive delivery levels consistent with performance expectations.Develop and maintain strong supplier relationships.Resolve quality, delivery, and financial issues with suppliersEvaluates forecast and inventory levelsDesign and implement methods to gather and manage manufacturing supply chain dataAbility to expedite and adapt to a changing scheduleContribute to and implement procurement strategies to optimize cost, quality and efficiencyQualifications:Bachelor's degree in a business or engineering related field, or comparable experienceExperience analyzing and improving supply chain data, information and processesSupply Chain Management (APICS, CSCP, CPIM etc) certification is not necessary though strongly preferredPurchasing in a manufacturing environmentStrong Excel / Google Doc skills, MRP experience and ERP (preferably Microsoft Dynamics) system knowledgeStrong documentation, reporting, and organizational skills.Proven ability to multitaskGood communication skillsAbility to solve problems and resolve issues quicklyStrong comprehension skillsMinimum 2 years experience in Purchasing, MRP, Procurement, Planning or similar functionBy applying to Rogue, regardless of the platform you choose to use, you are agreeing to Rogue's preferred methods of communication (i.e. text message). Submitting an application, through whatever online forum is ultimately used, constitutes a knowing and voluntary agreement to send and receive text messages during the recruitment process.
Buyer - Manufacturing
Posted 22 days ago
Job Viewed
Job Description
Overview:
We are looking for an experienced Buyer for Manufacturing in our Columbus, OH headquarters. The Buyer - Manufacturing is directly responsible for the supplier relationship management process related to Rogue Fitness's manufacturing operations. Procurement of raw materials, components, subassemblies and services are the core responsibilities.
The Buyer - Manufacturing is a fully onsite role in Columbus, Ohio. Remote work is not available.
Applicants must be authorized to work in the United States for any employer.
Responsibilities:
- Analyze Rogue inventory and demand for manufacturing components to drive and execute purchasing decisions
- Identify and evaluate potential suppliers
- Sourcing for multiple commodities (i.e. Plastics, Steel, Aluminum, Services, Etc)
- Ensures products and services are secured at cost, quality, and competitive delivery levels consistent with performance expectations.
- Develop and maintain strong supplier relationships.
- Resolve quality, delivery, and financial issues with suppliers
- Evaluates forecast and inventory levels
- Design and implement methods to gather and manage manufacturing supply chain data
- Ability to expedite and adapt to a changing schedule
- Contribute to and implement procurement strategies to optimize cost, quality and efficiency
- Bachelor's degree in a business or engineering related field, or comparable experience
- Experience analyzing and improving supply chain data, information and processes
- Supply Chain Management (APICS, CSCP, CPIM etc) certification is not necessary though strongly preferred
- Purchasing in a manufacturing environment
- Strong Excel / Google Doc skills, MRP experience and ERP (preferably Microsoft Dynamics) system knowledge
- Strong documentation, reporting, and organizational skills.
- Proven ability to multitask
- Good communication skills
- Ability to solve problems and resolve issues quickly
- Strong comprehension skills
- Minimum 2 years experience in Purchasing, MRP, Procurement, Planning or similar function
By applying to Rogue, regardless of the platform you choose to use, you are agreeing to Rogue's preferred methods of communication (i.e. text message). Submitting an application, through whatever online forum is ultimately used, constitutes a knowing and voluntary agreement to send and receive text messages during the recruitment process.
Manufacturing Engineer

Posted 9 days ago
Job Viewed
Job Description
**Allied Mineral Products** is a leading manufacturer of monolithic refractories worldwide. We are seeking a **Manufacturing** **Engineer** in our Columbus, Ohio location. This position is responsible to dentify, design, and implement engineering solutions to increase efficiency, lower costs, improve environmental, health, safety, and quality, or reduce downtime of production and facility equipment.
Focus area for the Manufacturing Engineer is to support the organization in continuous improvement efforts, leveraging expertise in project management, equipment design, operations, and maintenance. Will work closely with other engineering disciplines in development of new systems or refinement of existing equipment and processes.
**Key Duties:**
+ Using continuous improvement and problem-solving methodologies, identify opportunities to advance manufacturing operations tools and technology.
+ Conduct process reviews, perform root cause analyses, develop improvement plans implementing lean manufacturing principles.
+ Design improvement solutions for equipment and systems to manufacture and handle all materials produced by Allied Mineral Products.
+ Support Allied's manufacturing operations around the world. Occasional travel to US or international locations may be required.
+ Produce accurate mechanical and electrical drawings for layout, assembly, fabrication, and erection of equipment and facilities.
+ Prepare specifications for bidding and purchasing of equipment, materials, supplies, and services.
+ Manage all types of plant engineering projects, from beginning to end. This may include defining requirements, developing a series of designs, obtaining buy in from other parties, planning and supervising installations, tracking revisions, and producing final documentation.
+ Coordinate outside contractors, as needed, to complete any assigned projects.
+ Identify and recommend preventive maintenance procedures and spare parts requirements on new equipment.
+ Provide engineering support on major breakdowns, equipment rebuilds, and reoccurring maintenance problem areas.
+ Provide training and instruction to Maintenance and other Allied employees on new equipment, safety, and other topics.
+ Troubleshoot and identify issues with facilities equipment. Make simple repairs, when necessary.
+ Maintain excellent lines of communication with Maintenance, Production, other Allied departments, and our affiliates.
**Qualifications:**
+ Requires a Bachelor of Science degree in Mechanical Engineering, or other similar technical field, or equivalent work experience.
+ At least five years of related work experience and significant prior project management experience preferred.
+ Strong experience in industrial equipment, such as dust collection, material handling, desired.
+ Knowledge of mechanical and electrical design principles required.
+ Requires excellent troubleshooting skills and a practical approach to problem solving.
+ Ability to use a computer for CAD and other tasks.
+ Excellent written and verbal communication, and human relations skills required.
+ Must be able to work independently.
+ Willingness to work flexible hours as needed.
+ Additional skills useful to this position include knowledge of industrial electrical controls and PLC programming, prior experience working with HVAC and facilities equipment, or experience with burner or combustion systems.
**Working Environment**
+ Office work environment.
+ Frequent exposure to Allied's manufacturing facilities, which may include dusty, hot, or cold conditions.
+ Required to follow Allied Mineral Products' Safety & Health policy and wear Personal Protective Equipment (PPE) as appropriate.
**Allied Mineral Products offers competitive wages, health, dental, STD, LTD, ESOP retirement plan and profit sharing. Passing a drug screen is required prior to starting work should an offer be made.**
**Allied Mineral Products Holding, Inc. is an Equal Opportunity Employer/Veterans/Disabled.**
Manufacturing Engineer
Posted 15 days ago
Job Viewed
Job Description
As a Manufacturing Engineer, you will be responsible for designing, developing, and optimizing manufacturing processes to ensure high-quality production, cost efficiency, and timely delivery. You will work closely with design, quality, and production teams to implement best practices, resolve production issues, and introduce new technologies. This role is crucial in driving operational excellence and supporting the overall manufacturing strategy.
Key Responsibilities:
- Designing, developing, and implementing new manufacturing processes and equipment.
- Optimizing existing production lines for efficiency, yield, and quality improvements.
- Conducting time studies, process mapping, and value stream mapping to identify bottlenecks and areas for improvement.
- Developing and maintaining manufacturing documentation, including work instructions, process specifications, and standard operating procedures (SOPs).
- Collaborating with product design teams to ensure manufacturability (DfM) and assembly (DfA) considerations are integrated early in the design cycle.
- Troubleshooting production issues, performing root cause analysis, and implementing corrective actions.
- Implementing Lean manufacturing and Six Sigma methodologies to reduce waste and variability.
- Selecting, specifying, and justifying new manufacturing equipment and tooling.
- Ensuring compliance with safety regulations, environmental standards, and quality management systems (e.g., ISO).
- Providing technical support and training to production operators and technicians.
- Participating in cross-functional teams for new product introductions (NPI).
- Analyzing production data to identify trends and drive data-driven decisions.
- Managing small to medium-sized capital projects related to manufacturing improvements.
Qualifications:
- Bachelor's degree in Manufacturing Engineering, Mechanical Engineering, Industrial Engineering, or a related field.
- Minimum of 3-5 years of experience as a Manufacturing Engineer in a production environment.
- Strong understanding of Lean manufacturing principles and Six Sigma methodologies.
- Proficiency in CAD software (e.g., AutoCAD, SolidWorks) and process simulation tools.
- Experience with various manufacturing processes (e.g., machining, assembly, automation, welding).
- Excellent problem-solving, analytical, and critical thinking skills.
- Strong written and verbal communication skills, with the ability to communicate technical information effectively.
- Ability to work independently and collaboratively in a fast-paced manufacturing setting.
- Experience with ERP/MRP systems is a plus.
- Commitment to safety and continuous improvement.
Our client offers a competitive salary, comprehensive benefits, and a dynamic work environment with significant opportunities for professional growth and impact. Join a team dedicated to manufacturing excellence and innovation.
Manufacturing Engineer
Posted 15 days ago
Job Viewed
Job Description
Key Responsibilities:
- Design, develop, and optimize manufacturing processes, equipment, and tooling to improve efficiency, reduce costs, and enhance product quality.
- Conduct thorough analysis of existing production lines, identifying bottlenecks, inefficiencies, and areas for improvement.
- Implement Lean manufacturing principles, Six Sigma methodologies, and other continuous improvement techniques to streamline operations.
- Collaborate with R&D, Design, and Production teams to ensure manufacturability of new products and smooth transitions from design to production.
- Develop and maintain detailed standard operating procedures (SOPs), work instructions, and process documentation.
- Evaluate and select new manufacturing technologies, machinery, and automation solutions, overseeing their integration into production.
- Troubleshoot and resolve complex manufacturing issues, working closely with production supervisors and maintenance teams.
- Design and conduct experiments (DOE) to validate process changes and optimize parameters.
- Conduct cost analysis and feasibility studies for new projects and process improvements.
- Ensure compliance with safety regulations, environmental standards, and quality management systems (e.g., ISO 9001).
Qualifications:
- Bachelor's degree in Manufacturing Engineering, Mechanical Engineering, Industrial Engineering, or a related field.
- 3+ years of progressive experience as a Manufacturing Engineer in a high-volume or precision manufacturing environment.
- Strong knowledge of various manufacturing processes, such as machining, assembly, welding, automation, and material handling.
- Proficiency in CAD software (e.g., SolidWorks, AutoCAD) for designing fixtures, tooling, and layouts.
- Demonstrated experience with Lean Manufacturing, Six Sigma, or other continuous improvement methodologies.
- Excellent analytical, problem-solving, and root cause analysis skills.
- Strong communication and interpersonal skills, with the ability to collaborate effectively across departments.
- Ability to interpret technical drawings, blueprints, and specifications.
Preferred Skills:
- Experience with robotics and industrial automation.
- Knowledge of statistical process control (SPC).
- Certification in Lean Six Sigma (Green Belt or Black Belt).
Our client offers a challenging and rewarding career, competitive salary, comprehensive benefits, and opportunities for professional growth in an environment that fosters innovation. Join a team committed to manufacturing excellence.
Be The First To Know
About the latest Manufacturing Jobs in Canal Winchester !
Manufacturing Engineer
Posted 15 days ago
Job Viewed
Job Description
Our client, a well-established manufacturing company known for its innovative products, is seeking a highly skilled and experienced Manufacturing Engineer to join their operations team in Columbus, Ohio, US . This crucial role involves optimizing production processes, improving efficiency, and implementing lean manufacturing principles to enhance overall operational performance. The ideal candidate will be a proactive problem-solver with a strong background in process improvement, automation, and industrial engineering methodologies. Our client is committed to continuous improvement and technological advancement, providing a dynamic environment where your expertise will directly contribute to streamlining production lines and reducing costs. This position offers an exciting opportunity to apply your technical skills to real-world manufacturing challenges, driving tangible results and fostering a culture of operational excellence. We are looking for someone who is detail-oriented, analytical, and possesses excellent communication skills to collaborate effectively with cross-functional teams and drive successful projects from conception to completion.
Key Responsibilities:
- Analyze existing manufacturing processes to identify areas for improvement in efficiency, quality, cost reduction, and safety.
- Design, develop, and implement new manufacturing processes, equipment, and tooling to optimize production flow and enhance productivity.
- Conduct time studies, process mapping, and value stream mapping to identify bottlenecks and eliminate waste within the production system.
- Implement and champion Lean Manufacturing and Six Sigma methodologies to drive continuous improvement initiatives.
- Collaborate with product design, quality assurance, and production teams to ensure manufacturability of new products and seamless transition from design to production.
- Develop and maintain standard operating procedures (SOPs), work instructions, and process documentation.
- Troubleshoot manufacturing issues, provide technical support to production lines, and resolve root causes of defects or downtime.
- Perform cost analysis and justification for new equipment, process changes, and automation projects.
- Ensure compliance with relevant industry standards, safety regulations, and environmental guidelines in all manufacturing processes.
- Train production staff on new processes, equipment, and quality control procedures.
Qualifications:
- Bachelor's degree in Manufacturing Engineering, Industrial Engineering, Mechanical Engineering, or a related engineering discipline.
- Minimum of 3-5 years of experience in a manufacturing engineering role within a production environment.
- Proven experience with Lean Manufacturing, Six Sigma, or other continuous improvement methodologies; certification (e.g., Green Belt, Black Belt) is a plus.
- Strong analytical and problem-solving skills, with a data-driven approach to decision-making.
- Proficiency in CAD software (e.g., AutoCAD, SolidWorks) and manufacturing simulation tools.
- Knowledge of automation, robotics, and advanced manufacturing technologies is highly desirable.
- Excellent written and verbal communication skills, with the ability to clearly articulate technical concepts.
- Ability to work effectively in a team environment and collaborate with various departments.
- Experience with ERP systems and manufacturing execution systems (MES) is a plus.
What We Offer:
Our client offers a competitive salary, a comprehensive benefits package including health, dental, and vision insurance, a 401(k) retirement plan with company match, and generous paid time off. You will have opportunities for continuous professional development, exposure to cutting-edge manufacturing technologies, and a challenging role in a supportive environment where your contributions are valued and directly impact operational excellence.
Quality Control Technician
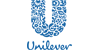
Posted 9 days ago
Job Viewed
Job Description
In 2011, we didn't just disrupt the entire shaving industry; we revolutionized it, shattering conventions with a viral video sensation that became the gold standard for humor in advertising. Our trailblazing direct-to-consumer model didn't just pave new paths-it bulldozed age old industry giants, minting us as a force to be reckoned with.
Dollar Shave Club crafted not just products, but experiences. We made shaving not suck by cutting out all the unnecessary BS that's been upsold to guys for decades. We continued to make great f**king blades and also became the geniuses behind tons of dude-centric products like Ball Spray, offering solutions to problems men didn't know they needed.
Today we continue to expand our international grooming arsenal, and hold fast to the disruptive DNA and irreverent humor that catapulted us to fame. Our global expansion and presence in tens of thousands of retail stores are testaments to our commitment to make the hairy globe a little smoother.
Stop wasting time not working for us and come join the club!
**ROLE SUMMARY:**
We're excited to bring on a qualified Quality Control Technician with hands-on experience in both packing and formulation product evaluations. The ideal candidate will have a strong understanding of quality standards and be confident in reviewing products against established guidelines. This role plays a key part in auditing products throughout their life cycle within the fulfillment center, helping ensure our customers receive only the highest quality items. You should be comfortable working in a warehouse environment and will be responsible for performing in-line quality inspections as part of the fulfillment process.
When non-conformances occur, you must be able to escalate issues appropriately and thoroughly document all key details. In addition, this role will be responsible for collecting and reporting quality performance data from the production floor on a monthly basis. We're looking for someone who is organized, capable of working with minimal supervision, and committed to maintaining high quality standards throughout the operation.
**RESPONSIBILITIES:**
+ Conduct quality control inspections of incoming products and packaging items
+ Review incoming paperwork (inc. trailer inspections, CoAs, etc.) and release product to production in our warehouse management system
+ In the case of non-conformances, collect data and samples to support in the investigation
+ Provide oversight into the rework process for the quality function
+ Conduct in-line product quality checks throughout the fulfillment process
+ Manage and organize product retains
+ Support the Quality Control Manager in executing quality programs throughout the site
+ Support the site Inventory Clerks in traceability management
**REQUIREMENTS:**
+ 3+ years experience in an operations environment (manufacturing, fulfillment, etc.)
+ 3+ years experience within consumer packaged goods, personal care items, pharmaceutical, food industry, or a similar industry
+ Experience with WMS Softwares (SAP, HighJump, Korber, JDA, etc.)
**POSITION TYPE:**
This is a full-time hourly position.
**SCHEDULE:**
Sunday through Wednesday - 7:00 am to 5:30 pm **OR** Wednesday through Saturday - 7:00 am to 5:30 pm
**SALARY:**
$17/hr
**BENEFITS (NON-EXEMPT):**
+ Comprehensive benefit plans with low premium options, including medical, dental and vision coverage, along with supplemental coverage options
+ Free life insurance, short term disability and long term disability
+ 401(k) plan with a company match of 100% of the first 2%, and 50% of up to an additional 4% with no vesting period
+ Generous accrued vacation time and sick time
+ 12 weeks of fully paid parental leave
+ 4 weeks of fully paid disability leave
+ Free Dollar Shave Club Products
**APPLICATION PROCESS:**
All applications must be submitted via our Applicant Tracking System, Greenhouse, in order to be considered. Once you submit your application, the recruiting team will review your submission and will reach out if your skill sets and/or qualifications match our needs. If selected, you'll be invited to an initial phone screening interview with a recruiter before meeting with various members of the team. Candidates will be notified if they are not selected for the position. The position will remain open and we'll be accepting applications until the role is filled.
Dollar Shave Club is an Equal Opportunity employer. All qualified applicants will receive consideration for employment without regard to age, race, color, religion, gender, sexual orientation, gender identification, national origin, disability, or protected veteran status.
Reasonable Accommodation: Dollar Shave Club provides reasonable accommodation so that qualified applicants with a disability may participate in the selection process. Please advise us of any accommodations you request in order to express interest in a position by e-mailing:
Please state your request for assistance in your message. Only reasonable accommodation requests related to applying for a specific position within Dollar Shave Club will be reviewed at the e-mail address supplied.
Dollar Shave Club will consider for employment qualified applicants with criminal histories in a manner consistent with the requirements of the Los Angeles Fair Chance Initiative for Hiring (Ban the Box) Ordinance.
Thank you for considering a career with Dollar Shave Club
Privacy Notice for California Job Applicants ( Shave Club participates in the E-Verify program. Please click the links for more information:
+ E-Verify Participation ( Right to Work
#LI-MK1
Quality Control Inspector
Posted 15 days ago
Job Viewed
Job Description
About Our Client: Our client has a long-standing reputation for producing high-quality, reliable components using advanced manufacturing techniques. They are committed to operational excellence, continuous improvement, and maintaining the highest product quality standards. Their culture emphasizes teamwork, precision, and a commitment to safety, offering a stable and professional environment for skilled quality professionals.
Key Responsibilities:
- Perform visual and dimensional inspections of raw materials, in-process components, and finished products using various measuring tools (e.g., calipers, micrometers, gauges).
- Ensure all products comply with engineering drawings, specifications, and quality standards (e.g., ISO, IATF).
- Identify, document, and report non-conforming materials or products, initiating corrective actions as necessary.
- Conduct first-piece, in-process, and final inspections according to control plans and sampling procedures.
- Maintain accurate and detailed inspection records, quality logs, and test reports.
- Collaborate with production personnel and engineers to troubleshoot quality issues and implement preventive measures.
- Assist in the calibration and maintenance of inspection equipment.
- Participate in root cause analysis for recurring defects and support continuous improvement initiatives.
- Adhere to all safety protocols and maintain a clean and organized work area.
- Contribute to the overall quality management system of the facility.
Qualifications:
- High school diploma or GED equivalent; Associate's degree or technical certification in Quality Control, Manufacturing, or a related field is a plus.
- 2+ years of experience in quality control or inspection within a manufacturing environment, preferably automotive or precision machining.
- Proficiency in using various measuring instruments and reading blueprints/technical drawings.
- Strong understanding of quality control principles and methodologies (e.g., SPC, 8D, FMEA).
- Excellent attention to detail and strong observational skills.
- Ability to identify and document defects accurately.
- Strong communication skills, both verbal and written.
- Ability to work independently and as part of a team.
- Basic computer proficiency for data entry and reporting.
- Knowledge of ISO 9001 or IATF 16949 standards is highly desirable.
What We Offer:
- Competitive salary and comprehensive benefits package.
- A stable and professional work environment.
- Opportunities for professional development and continuous learning.
- Direct impact on product quality and customer satisfaction.
- A collaborative and supportive team.
If you are a meticulous and experienced Quality Control Inspector passionate about ensuring product excellence, our client invites you to apply. Join their commitment to quality. Apply today!