14 Manufacturing jobs in Merrillville
Quality Control Technician
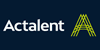
Posted today
Job Viewed
Job Description
The Mold Quality Technician plays a vital role in maintaining the integrity and performance of molds used in the production of concrete and molten steel castings. This hands-on position involves mold inspection, quality control, troubleshooting, and contributing to continuous improvement efforts. The ideal candidate will be highly organized, detail-oriented, and capable of interpreting technical drawings and performing dimensional inspections. This role offers growth opportunities, including potential leadership positions as the department expands and modernizes.
Responsibilities
+ Own the mold quality process from design through production.
+ Perform dimensional and visual inspections to ensure molds meet specifications.
+ Troubleshoot mold-related issues and coordinate maintenance or repairs.
+ Maintain mold identification, tracking, and preventive maintenance programs.
+ Collaborate with engineers, production, and product managers on new mold introductions.
+ Conduct mold audits and manage technical documentation and internal databases.
+ Support safety, quality, delivery, and cost goals.
+ Participate in internal and external audits and continuous improvement initiatives.
+ Operate in both office and production environments, including exposure to heat, noise, and heavy equipment.
Essential Skills
+ Proficient in reading and understanding CAD drawings and technical blueprints.
+ Skilled in using calipers, tape measures, and precision tools for dimensional checks.
+ Experienced in conducting inspections, audits, and standardized tests.
+ Knowledgeable in mold tracking, preventive maintenance, and repair coordination.
+ Actively contributes to continuous improvement initiatives.
+ Comfortable working in industrial environments with adherence to safety protocols.
+ Strong grasp of basic math, including percentages, averages, and algebra.
+ Maintains detailed records of inspections, test results, and mold performance.
Additional Skills & Qualifications
+ High School Diploma or GED required.
+ Associate's or Bachelor's degree in Mechanical Engineering or related field preferred.
+ 3-5 years of experience in manufacturing, tool shop, maintenance, or welding.
+ Familiarity with quality control processes and procedures.
+ Experience using calipers, tape measures, and hand tools.
+ Strong organizational and analytical skills.
+ Ability to read and interpret technical drawings (CAD).
+ Proficient in Microsoft Excel and general office software.
+ Excellent verbal and written communication.
+ Comfortable working independently and under pressure.
+ Positive, diplomatic, and engaging demeanor with leadership potential.
Pay and Benefits
The pay range for this position is $20.00 - $24.00/hr.
Eligibility requirements apply to some benefits and may depend on your job classification and length of employment. Benefits are subject to change and may be subject to specific elections, plan, or program terms. If eligible, the benefits available for this temporary role may include the following:
- Medical, dental & vision - Critical Illness, Accident, and Hospital - 401(k) Retirement Plan - Pre-tax and Roth post-tax contributions available - Life Insurance (Voluntary Life & AD&D for the employee and dependents) - Short and long-term disability - Health Spending Account (HSA) - Transportation benefits - Employee Assistance Program - Time Off/Leave (PTO, Vacation or Sick Leave)
Workplace Type
This is a fully onsite position in Olympia Fields,IL.
Application Deadline
This position is anticipated to close on Jul 28, 2025.
About Actalent
Actalent is a global leader in engineering and sciences services and talent solutions. We help visionary companies advance their engineering and science initiatives through access to specialized experts who drive scale, innovation and speed to market. With a network of almost 30,000 consultants and more than 4,500 clients across the U.S., Canada, Asia and Europe, Actalent serves many of the Fortune 500.
The company is an equal opportunity employer and will consider all applications without regard to race, sex, age, color, religion, national origin, veteran status, disability, sexual orientation, gender identity, genetic information or any characteristic protected by law.
If you would like to request a reasonable accommodation, such as the modification or adjustment of the job application process or interviewing due to a disability, please email (% ) for other accommodation options.
Quality Control Technician
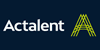
Posted today
Job Viewed
Job Description
+ Own the mold quality process from design through production.
+ Perform dimensional and visual inspections to ensure molds meet specifications.
+ Troubleshoot mold-related issues and coordinate maintenance or repairs.
+ Maintain mold identification, tracking, and preventive maintenance programs.
+ Conduct mold audits and manage technical documentation and internal databases.
+ Participate in internal and external audits and continuous improvement initiatives.
+ Operate in both office and production environments, including exposure to heat, noise, and heavy equipment.
Essential Skills
+ Proficient in reading and understanding CAD drawings and technical blueprints.
+ Skilled in using calipers, tape measures, and precision tools for dimensional checks.
+ Experienced in conducting inspections, audits, and standardized tests.
+ Knowledgeable in mold tracking, preventive maintenance, and repair coordination.
+ Actively contributes to continuous improvement initiatives.
+ Comfortable working in industrial environments with adherence to safety protocols.
+ Strong grasp of basic math, including percentages, averages, and algebra.
+ Maintains detailed records of inspections, test results, and mold performance.
Pay and Benefits
The pay range for this position is $20.00 - $24.00/hr.
Eligibility requirements apply to some benefits and may depend on your job classification and length of employment. Benefits are subject to change and may be subject to specific elections, plan, or program terms. If eligible, the benefits available for this temporary role may include the following:
- Medical, dental & vision - Critical Illness, Accident, and Hospital - 401(k) Retirement Plan - Pre-tax and Roth post-tax contributions available - Life Insurance (Voluntary Life & AD&D for the employee and dependents) - Short and long-term disability - Health Spending Account (HSA) - Transportation benefits - Employee Assistance Program - Time Off/Leave (PTO, Vacation or Sick Leave)
Workplace Type
This is a fully onsite position in Chicago Heights,IL.
Application Deadline
This position is anticipated to close on Jul 29, 2025.
About Actalent
Actalent is a global leader in engineering and sciences services and talent solutions. We help visionary companies advance their engineering and science initiatives through access to specialized experts who drive scale, innovation and speed to market. With a network of almost 30,000 consultants and more than 4,500 clients across the U.S., Canada, Asia and Europe, Actalent serves many of the Fortune 500.
The company is an equal opportunity employer and will consider all applications without regard to race, sex, age, color, religion, national origin, veteran status, disability, sexual orientation, gender identity, genetic information or any characteristic protected by law.
If you would like to request a reasonable accommodation, such as the modification or adjustment of the job application process or interviewing due to a disability, please email (% ) for other accommodation options.
Quality Control Technician
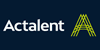
Posted today
Job Viewed
Job Description
The Mold Quality Technician plays a vital role in maintaining the integrity and performance of molds used in the production of concrete and molten steel castings. This hands-on position involves mold inspection, quality control, troubleshooting, and contributing to continuous improvement efforts. The ideal candidate will be highly organized, detail-oriented, and capable of interpreting technical drawings and performing dimensional inspections. This role offers growth opportunities, including potential leadership positions as the department expands and modernizes.
Responsibilities
+ Own the mold quality process from design through production.
+ Perform dimensional and visual inspections to ensure molds meet specifications.
+ Troubleshoot mold-related issues and coordinate maintenance or repairs.
+ Maintain mold identification, tracking, and preventive maintenance programs.
+ Collaborate with engineers, production, and product managers on new mold introductions.
+ Conduct mold audits and manage technical documentation and internal databases.
+ Support safety, quality, delivery, and cost goals.
+ Participate in internal and external audits and continuous improvement initiatives.
+ Operate in both office and production environments, including exposure to heat, noise, and heavy equipment.
Essential Skills
+ Proficient in reading and understanding CAD drawings and technical blueprints.
+ Skilled in using calipers, tape measures, and precision tools for dimensional checks.
+ Experienced in conducting inspections, audits, and standardized tests.
+ Knowledgeable in mold tracking, preventive maintenance, and repair coordination.
+ Actively contributes to continuous improvement initiatives.
+ Comfortable working in industrial environments with adherence to safety protocols.
+ Strong grasp of basic math, including percentages, averages, and algebra.
+ Maintains detailed records of inspections, test results, and mold performance.
Additional Skills & Qualifications
+ High School Diploma or GED required.
+ Associate's or Bachelor's degree in Mechanical Engineering or related field preferred.
+ 3-5 years of experience in manufacturing, tool shop, maintenance, or welding.
+ Familiarity with quality control processes and procedures.
+ Experience using calipers, tape measures, and hand tools.
+ Strong organizational and analytical skills.
+ Ability to read and interpret technical drawings (CAD).
+ Proficient in Microsoft Excel and general office software.
+ Excellent verbal and written communication.
+ Comfortable working independently and under pressure.
+ Positive, diplomatic, and engaging demeanor with leadership potential.
Pay and Benefits
The pay range for this position is $20.00 - $24.00/hr.
Eligibility requirements apply to some benefits and may depend on your job classification and length of employment. Benefits are subject to change and may be subject to specific elections, plan, or program terms. If eligible, the benefits available for this temporary role may include the following:
- Medical, dental & vision - Critical Illness, Accident, and Hospital - 401(k) Retirement Plan - Pre-tax and Roth post-tax contributions available - Life Insurance (Voluntary Life & AD&D for the employee and dependents) - Short and long-term disability - Health Spending Account (HSA) - Transportation benefits - Employee Assistance Program - Time Off/Leave (PTO, Vacation or Sick Leave)
Workplace Type
This is a fully onsite position in Chicago Heights,IL.
Application Deadline
This position is anticipated to close on Jul 25, 2025.
About Actalent
Actalent is a global leader in engineering and sciences services and talent solutions. We help visionary companies advance their engineering and science initiatives through access to specialized experts who drive scale, innovation and speed to market. With a network of almost 30,000 consultants and more than 4,500 clients across the U.S., Canada, Asia and Europe, Actalent serves many of the Fortune 500.
The company is an equal opportunity employer and will consider all applications without regard to race, sex, age, color, religion, national origin, veteran status, disability, sexual orientation, gender identity, genetic information or any characteristic protected by law.
If you would like to request a reasonable accommodation, such as the modification or adjustment of the job application process or interviewing due to a disability, please email (% ) for other accommodation options.
Material Handler- Manufacturing
Posted 3 days ago
Job Viewed
Job Description
With supervision completes Warehousing, Inventory Control, Receiving, Shipping, Product Identification and traceability, and proper material handling and storage tasks. Completes inventory transactions such as transfers, issues, receipts on PC and ba Material Handler, Continuous Improvement, Manufacturing, Production, Inventory Control, Skills
Quality Technician (Manufacturing)
Posted 16 days ago
Job Viewed
Job Description
Location: ON-SITE HAMMOND, INDIANA (no relocation)
Department: Quality
Reports to: Multi-Site Quality Control Manager
Job Summary:
The Refractories QC Technician is responsible for ensuring that refractory materials, products, and processes meet established quality standards in the manufacturing of refractories. This includes conducting regular inspections, testing, and analysis of materials to verify compliance with specifications, identifying areas for improvement, and assisting in the resolution of quality issues.
Key Responsibilities:
Safety & compliance:
- Adhere to all safety protocols and regulations while performing tests and handling materials.
- Ensure that all quality control activities comply with environmental and health standards.
- Perform physical and chemical testing of refractory materials (e.g., bricks, mortars, castables) to ensure conformity with internal and external specifications.
- Conduct tests such as compressive strength, porosity and density.
- Inspect refractory products during various stages of production to ensure quality standards are met.
- Record and document test results, inspection findings, and quality control reports.
- Maintain accurate logs of test results for certification or audits.
- Provide regular updates to the QC Manager and production teams on material quality and performance.
- Identify any deviations from quality standards and report non-conformances to the appropriate departments.
- Assist in investigating root causes of quality issues and recommend corrective actions.
- Support the implementation of corrective actions and follow up on effectiveness.
- Ensure calibration of testing equipment is performed regularly and in accordance with manufacturer specifications.
- Assist with the maintenance and repair of testing equipment when necessary.
- Work closely with the production and procurement teams to communicate material quality issues and improve overall processes.
- Assist in training production staff on quality standards and best practices for refractory materials.
- Familiarity with laboratory testing procedures and equipment.
- Strong attention to detail and ability to identify discrepancies in materials or processes.
- Good problem-solving skills and ability to work under pressure.
- Must be able to handle and safety use testing equipment and tools.
- Occasional lifting of materials and work in high-temperature settings.
- This position may require working in shifts, including night shift or overtime, depending on production schedules and deadlines.
Manufacturing Equipment Technician
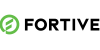
Posted today
Job Viewed
Job Description
**Description** :
We are looking for a reliable, experienced 2 nd shift equipment/facility maintenance technician to perform essential equipment troubleshooting, preventative maintenance, and facility maintenance. In this position, you will be responsible for a wide variety of activities such as repairs, preventative maintenance, and support engineering projects to ensure that our equipment and facilities are both running optimally. Also maintaining production quality by ensuring operation of machinery and mechanical/electrical equipment are running efficiently and trouble-free. You will be a key part of optimizing our processes and working with the operation team to create process improvements along with building a robust preventative maintenance program. Being reliable and self-motivated with a keen eye for detail is essential in this job, as the ideal candidate will have extensive work experience and excellent technical knowledge. You should have the manual dexterity and physical stamina necessary for this work. Excellent communication skills are a requirement as we must make sure everyone is on the same page.
**Primary Responsibilities:**
+ Evaluate equipment issues and be able to resolve issues in a timely manner.
+ Evaluate building systems to ensure compliance with health and safety regulations.
+ Conduct daily inspections of facility premises and equipment.
+ Conduct preventative maintenance and assist with engineering projects.
+ Perform hands-on repairs and maintenance on facility and manufacturing equipment, fixtures, and tools.
+ Respond promptly to emergencies, notifying the appropriate personnel and following safety protocols.
+ Provide daily reports to the maintenance manager on resolved issues, those requiring attention, and ongoing projects.
+ Develop annual performance and growth plans, reviewing them with the manager quarterly.
+ Prepare and submit production and quality improvement reports to the manager and team.
+ Collaborate with engineers, maintenance technicians, and production technicians to meet monthly on-time delivery targets.
**Qualifications:**
+ 3-5 years of experience in industrial maintenance with production equipment (electrical background preferred).
+ Strong understanding of equipment troubleshooting with the ability to think outside the box.
+ Understanding of electrical circuits with the ability to read schematics, PLC logic. Programming experience is a plus.
+ Experience working with vision systems is also a plus.
+ Physical ability to walk, stand, climb stairs, and lift heavy objects (over 40 lbs) for extended periods.
+ Experience with manual and electrical power tools, including machining equipment (end milling, power hand tools, and drilling presses).
+ 3-5 years of experience operating or maintaining various industrial assembly manufacturing equipment.
+ Capability to read and utilize technical manuals, mechanical drawings, and electrical schematics for independent troubleshooting of facility equipment and instruments.
+ Strong communication and interpersonal skills for effective teamwork.
+ Organized and detail-oriented, with a focus on 5S principles.
+ Willingness to work overtime, weekends, holidays, and shifts as needed to support production, both in-person and on-call.
+ Proficient in Microsoft Office (Outlook, Excel, Word).
+ Experience with robotics, vision systems, NI devices/software, and 3D CAD modeling is a plus.
+ Familiarity with documentation control, Kaizen, PSP, SW, 5S, and Six Sigma methodologies is preferred.
+ Experience with motor systems, sensors, barcode scanners/cameras, and understanding of safety protocols and OSHA requirements is a plus.
Fortive Corporation Overview:
Fortive is a diversified industrial growth company comprised of global businesses that are recognized leaders in attractive markets. With more than $7 billion in annual revenues, Fortive's well-known brands hold leading positions in field instrumentation, transportation, sensing, product realization, automation and specialty, and franchise distribution.
Fortive is headquartered in Everett, Washington and employs a team of more than 24,000 research and development, manufacturing, sales, distribution, service and administrative employees in more than 40 countries around the world. Our team grows by tackling challenges that accelerate progress and further their careers. With a culture rooted in continuous improvement, the core of our company's operating model is the Fortive Business System. For more information please visit: Corporation Overview**
Fortive's essential technology makes the world stronger, safer, and smarter. We accelerate transformation across a broad range of applications including environmental, health and safety compliance, industrial condition monitoring, next-generation product design, and healthcare safety solutions.
We are a global industrial technology innovator with a startup spirit. Our forward-looking companies lead the way in software-powered workflow solutions, data-driven intelligence, AI-powered automation, and other disruptive technologies. We're a force for progress, working alongside our customers and partners to solve challenges on a global scale, from workplace safety in the most demanding conditions to groundbreaking sustainability solutions.
We are a diverse team 17,000 strong, united by a dynamic, inclusive culture and energized by limitless learning and growth. We use the proven Fortive Business System (FBS) to accelerate our positive impact.
At Fortive, we believe in you. We believe in your potential-your ability to learn, grow, and make a difference.
At Fortive, we believe in us. We believe in the power of people working together to solve problems no one could solve alone.
At Fortive, we believe in growth. We're honest about what's working and what isn't, and we never stop improving and innovating.
Fortive: For you, for us, for growth.
**About Fluke Health Solutions**
Comprised of four industry leaders-Fluke Biomedical, LANDAUER, RaySafe, and Victoreen - Fluke Health Solutions (FHS) leads the biomedical and radiation detection markets with innovative products and services that help keep customers, patients, and clients safe.
Fluke Biomedical leads the world in manufacturing biomedical test equipment like defibrillator analyzers and digital pressure meters. LANDAUER measures radiation exposure with dosimeter and radiation monitoring badges. RaySafe is the worldwide leader of X-ray test equipment, real-time staff dosimetry, and radiation survey meters. And Victoreen instruments are the trusted source for radiation monitoring systems and quality assurance for nuclear power professionals.
At FHS, we believe in your potential - your ability to learn, grow and contribute in meaningful ways. And we believe in giving you the opportunity, accountability, and visibility to do just that.
We Are an Equal Opportunity Employer. Fortive Corporation and all Fortive Companies are proud to be equal opportunity employers. We value and encourage diversity and solicit applications from all qualified applicants without regard to race, color, national origin, religion, sex, age, marital status, disability, veteran status, sexual orientation, gender identity or expression, or other characteristics protected by law. Fortive and all Fortive Companies are also committed to providing reasonable accommodations for applicants with disabilities. Individuals who need a reasonable accommodation because of a disability for any part of the employment application process, please contact us at
**Pay Range**
The salary range for this position (in local currency) is 47,500.00 - 88,100.00
The salary range for this position (in local currency) is 47,500.00 - 88,100.00
We are an Equal Opportunity Employer
Fortive Corporation and all Fortive Companies are proud to be equal opportunity employers. We value and encourage diversity and solicit applications from all qualified applicants without regard to race, color, national origin, religion, sex, age, marital status, disability, veteran status, sexual orientation, gender identity or expression, or other characteristics protected by law. Fortive and all Fortive Companies are also committed to providing reasonable accommodations for applicants with disabilities. Individuals who need a reasonable accommodation because of a disability for any part of the employment application process, please contact us at
Materials Purchasing Manager - Manufacturing
Posted 3 days ago
Job Viewed
Job Description
Fast growing employee owned companyNewly created position due to company growthAbout Our ClientMy client is a fast growing family and employee owned company that has been in business for over 100 years. They are in high growth and have doubled in size over the past 10 years. My client is very dedicated to their company culture and have a strong track record of employee retention. If you are looking for a company that values their employees, rapidly growing and employee owned this is a great opportunity!Job DescriptionManage and oversee the procurement and supply chain operations.Develop and implement purchasing strategies.Negotiate with suppliers to ensure cost-effectiveness.Monitor supplier performance to assess ability to meet quality and delivery requirements.Identify and research potential new suppliers.Collaborate with team members on procurement needs and specifications.Manage and control all procurement activities including order placement, supplier follow-up, and supplier evaluations.Ensure compliance with company procurement policies and quality standards.MPI does not discriminate on the basis of race, color, religion, sex, sexual orientation, gender identity or expression, national origin, age, disability, veteran status, marital status, or based on an individual's status in any group or class protected by applicable federal, state or local law. MPI encourages applications from minorities, women, the disabled, protected veterans and all other qualified applicants. MPI does not discriminate on the basis of race, color, religion, sex, sexual orientation, gender identity or expression, national origin, age, disability, veteran status, marital status, or based on an individual's status in any group or class protected by applicable federal, state or local law. MPI encourages applications from minorities, women, the disabled, protected veterans and all other qualified applicants. The Successful ApplicantA successful Purchasing Manager should have:Bachelor's degree in Supply Chain, Business, or a related field preferred.5+ years of procurement experience with a focus on direct materials; 2+ years in a leadership or management role.Strong negotiation and contract management skills.Experience with ERP/MRP systems such as SAP, Oracle, or JD Edwards.Excellent analytical, communication, and organizational skills.Ability to manage multiple priorities in a fast-paced environment.What's on OfferAn attractive salary package ranging from $110,000 - $125,000 + Bonus.Opportunities for professional development and growth within the company.A supportive and collaborative work environment.Competitive benefits package.A chance to work in one of the leading companies in the Industrial/Manufacturing sector.We encourage all eligible candidates to apply and look forward to welcoming a new member to our team in Chesterton.ContactClayton HamiltonQuote job refJN-052025-6753460
Be The First To Know
About the latest Manufacturing Jobs in Merrillville !
Manufacturing Quality Associate - 2nd Shift
Posted 10 days ago
Job Viewed
Job Description
The Manufacturing Quality Associate is responsible for ensuring quality and compliance during the day-to-day operations in the manufacturing environment by partnering with operations, supply chain, engineering, quality control, or other functions to support product quality. This role provides GMP oversight through guidance against internal SOPs, WI, Protocols and Records as it pertains to manufacturing activities for development and commercial manufacturing.
Responsibilities:
- Monitors all operations pertaining to manufacturing to ensure adherence to AQST policies and procedures and provides guidance and clarity to colleagues to ensure consistent approaches to product quality are applied.
- Conducts routine internal audits and facility walkthroughs to ensure compliance with internal quality system requirements and to maintain a state of audit readiness.
- Initiates and investigates nonconformances, project managing to resolve quality issues by partnering with other functions.
- Author and review Forms, Batch Records, WI, SOPs, Protocols in electronic document management system
- Investigates assigned product quality complaints utilizing knowledge of the manufacturing and quality processes at Aquestive
- Owns CAPA records and action item implementation, partnering with operations, supply chain, engineering, and QC staff to ensure corrective actions are implemented according to approved timelines and ensuring their effectiveness post-implementation.
- Coordinates the Environmental Monitoring program including scheduling of third-party water testing, sampling, and report generation
- Short to medium term (3-12 months) project owner for quality projects to improve efficiency or compliance profile
- Understands the manufacturing schedule and provides quality support to ensure business continuity and seamless transitions between manufacturing stages.
- Operates with a sense of urgency in a fast-paced environment.
- Performs real time review of operational records, including Batch Records, and assists in obtaining any required corrections.
- Performs AQL Testing on finished product by verifying various attributes such as product appearance, product and packaging dimensions, presence and accuracy of printing on strip and pouch, and seal integrity.
- Performs line clearances for all steps of the manufacturing process.
- Reviews, assesses, and archives pest control documents.
- Maintains QA Retain Program, including sampling, inventory management and inspections required per internal SOPs.
- Leads process for ensuring manufacturing environment is in a state of control through the evaluation of the building automated system software, in partnership with Maintenance.
- Determines, documents and communicates when facility may be released back to cGMP operations after a shutdown, environmental excursion, etc.
- Performs other duties as instructed by quality management.
- Acknowledges that this position requires off-hours and weekend work from time to time to assure adequate QA floor support.
- BS degree required preferably in chemistry, biochemistry, or related science field.
- 5+ years of related experience in the pharmaceutical, biotechnology, or medical device industry responsibility preferred.
- Demonstrated knowledge of quality systems, GMPs, industry standards, and regulatory requirements for the manufacture, testing, and release of pharmaceutical products.
- Formal training in Quality disciplines (auditing, engineering, process improvement) as demonstrated through certification (ASQ, Lean Six Sigma, etc) highly preferred
- Technical proficiency at reviewing/auditing production records, reports and/or GMP related documentation.
- Ability to work within a team environment and willingness to contribute to the overall goals of the company.
- Ability to lead project teams
- Ability to handle multiple assignments and projects with competing priorities while independently managing time is critical.
- Good organizational skills, high level of attention to detail, excellent oral and written communication skills with the ability to interact at all levels.
- Ability to lift up to 35lbs.
- Must be willing to work off hour shifts and weekends as necessary.
The above statements are intended to describe the general nature and level of the work being performed by colleagues assigned to this position. This is not intended to be an exhaustive list of all responsibilities, duties, and skills required. Aquestive reserves the right to make changes to the job description whenever necessary.
As part of Aquestive's employment process, final candidate will be required to complete a drug test and background check prior to employment commencing. Please Note: Aquestive is a drug-free workplace and has a drug free workplace policy in place.
Aquestive provides equal employment opportunities to all colleagues and applicants for employment and prohibits discrimination and harassment of any type without regard to race, color, religion, age, sex, national origin, disability status, genetics, protected veteran status, sexual orientation, gender identity or expression, or any other characteristic protected by federal, state or local laws.
Equal Opportunity Employer
This employer is required to notify all applicants of their rights pursuant to federal employment laws. For further information, please review the Know Your Rights notice from the Department of Labor.
Manufacturing Technician- Tool & Die Designer
Posted 21 days ago
Job Viewed
Job Description
Your Job
As a Manufacturing Technician- Tool and Die Design you will be responsible for developing, implementing, and improving manufacturing processes to achieve optimal efficiency, quality, and cost-effectiveness. You will work closely in a cross-functional team to ensure that our manufacturing operations run smoothly and meet our high standards.
Our Team
Molex creates connections for life by enabling technologies that transform the future and improve lives. We are seeking a skilled Manufacturing Technician- Tool and Die Design to be a core member and technical expert/liaison within the assigned new product development team to contribute to our ongoing success.
What You Will Do
- Responsible for designing and developing stamping dies and tooling for metal fabrication processes
- Work with tooling designers to develop new and more efficient dies to replace aging tooling
- Develop prototypes and oversee testing to ensure designs meet specifications and performance standards
- Collaborate with manufacturing and production teams to ensure designs are optimized for production efficiency and cost-effectiveness
- Create detailed designs for metal stamping dies and tooling using CAD software (e.g., SolidWorks, AutoCAD)
- Lead or participate in design for manufacturability (DFM) reviews to improve product design efficiency
- Ensure production tools operate at peak efficiency to meet customer requirements
- Design, develop, and fabricate test fixtures for the purposes of manufacture and inspection
- Build, repair, and troubleshoot production tooling and single hit stamping dies
- Complete automation machine builds by assembling components and sub-assemblies
Who You Are (Basic Qualifications)
- Completion of a technical school program, such as Tool & Die Apprenticeship, or 3 years of relevant experience in progressive die design.
- Previous experience in progressive die design and fabrication within a manufacturing environment.
- Proficient with manufacturing design software (Siemens NX, CAD/CAM, SolidWorks, etc.)
- Experience in creating blueprints and technical drawings
- Working knowledge of GD&T
- In order to comply with U.S. export control laws and regulations, this position requires applicants to either provide proof of U.S. citizenship or lawful permanent resident status or be eligible to receive an export authorization (a license) under the International Traffic in Arms Regulations and/or the Export Administration Regulations.
What Will Put You Ahead
- Bachelor's degree in applied science or mechanical engineering or industrial engineering
- Able to operate mills, lathes, surface grinders, and vertical machining centers
- Previous experience working with manufacturing plants and performing feasibility and process capabilities as part of New Product development
- Extensive knowledge of die protection sensors and other safety methods to protect tooling and quality of parts
- 3+ years of experience in CNC programming of vertical machining centers using Mastercam
- Good understanding and practical knowledge of Six Sigma quality development tools and principles (DOE, FMEA, etc.)
- Understanding and application of sound project management techniques managing projects to timelines, due dates and deadlines
At Koch companies, we are entrepreneurs. This means we openly challenge the status quo, find new ways to create value and get rewarded for our individual contributions. Any compensation range provided for a role is an estimate determined by available market data. The actual amount may be higher or lower than the range provided considering each candidate's knowledge, skills, abilities, and geographic location. If you have questions, please speak to your recruiter about the flexibility and detail of our compensation philosophy.
Hiring Philosophy
All Koch companies value diversity of thought, perspectives, aptitudes, experiences, and backgrounds. We are Military Ready and Second Chance employers. Learn more about our hiring philosophy here.
Who We Are
As a Koch company, Molex is a leading supplier of connectors and interconnect components, driving innovation in electronics and supporting industries from automotive to health care and consumer to data communications. The thousands of innovators who work for Molex have made us a global electronics leader. Our experienced people, groundbreaking products and leading-edge technologies help us deliver a wider array of solutions to more markets than ever before.
At Koch, employees are empowered to do what they do best to make life better. Learn how our business philosophy helps employees unleash their potential while creating value for themselves and the company.
Our Benefits
Our goal is for each employee, and their families, to live fulfilling and healthy lives. We provide essential resources and support to build and maintain physical, financial, and emotional strength - focusing on overall wellbeing so you can focus on what matters most. Our benefits plan includes - medical, dental, vision, flexible spending and health savings accounts, life insurance, ADD, disability, retirement, paid vacation/time off, educational assistance, and may also include infertility assistance, paid parental leave and adoption assistance. Specific eligibility criteria is set by the applicable Summary Plan Description, policy or guideline and benefits may vary by geographic region. If you have questions on what benefits apply to you, please speak to your recruiter.
Additionally, everyone has individual work and personal needs. We seek to enable the best work environment that helps you and the business work together to produce superior results.
Equal Opportunities
Equal Opportunity Employer, including disability and protected veteran status. Except where prohibited by state law, some offers of employment are conditioned upon successfully passing a drug test. This employer uses E-Verify. Please click here for additional information.
#J-18808-LjbffrManufacturing Quality Associate - 2nd Shift
Posted today
Job Viewed
Job Description
Job Summar y:
The Manufacturing Quality Associate is responsible for ensuring quality and compliance during the day-to-day operations in the manufacturing environment by partnering with operations, supply chain, engineering, quality control, or other functions to support product quality. This role provides GMP oversight through guidance against internal SOPs, WI, Protocols and Records as it pertains to manufacturing activities for development and commercial manufacturing.
Responsibilities:- Monitors all operations pertaining to manufacturing to ensure adherence to AQST policies and procedures and provides guidance and clarity to colleagues to ensure consistent approaches to product quality are applied.
- Conducts routine internal audits and facility walkthroughs to ensure compliance with internal quality system requirements and to maintain a state of audit readiness.
- Initiates and investigates nonconformances, project managing to resolve quality issues by partnering with other functions.
- Author and review Forms, Batch Records, WI, SOPs, Protocols in electronic document management system
- Investigates assigned product quality complaints utilizing knowledge of the manufacturing and quality processes at Aquestive
- Owns CAPA records and action item implementation, partnering with operations, supply chain, engineering, and QC staff to ensure corrective actions are implemented according to approved timelines and ensuring their effectiveness post-implementation.
- Coordinates the Environmental Monitoring program including scheduling of third-party water testing, sampling, and report generation
- Short to medium term (3-12 months) project owner for quality projects to improve efficiency or compliance profile
- Understands the manufacturing schedule and provides quality support to ensure business continuity and seamless transitions between manufacturing stages.
- Operates with a sense of urgency in a fast-paced environment.
- Performs real time review of operational records, including Batch Records, and assists in obtaining any required corrections.
- Performs AQL Testing on finished product by verifying various attributes such as product appearance, product and packaging dimensions, presence and accuracy of printing on strip and pouch, and seal integrity.
- Performs line clearances for all steps of the manufacturing process.
- Reviews, assesses, and archives pest control documents.
- Maintains QA Retain Program, including sampling, inventory management and inspections required per internal SOPs.
- Leads process for ensuring manufacturing environment is in a state of control through the evaluation of the building automated system software, in partnership with Maintenance.
- Determines, documents and communicates when facility may be released back to cGMP operations after a shutdown, environmental excursion, etc.
- Performs other duties as instructed by quality management.
- Acknowledges that this position requires off-hours and weekend work from time to time to assure adequate QA floor support.
Qualifications:
- BS degree required preferably in chemistry, biochemistry, or related science field.
- 5+ years of related experience in the pharmaceutical, biotechnology, or medical device industry responsibility preferred.
- Demonstrated knowledge of quality systems, GMPs, industry standards, and regulatory requirements for the manufacture, testing, and release of pharmaceutical products.
- Formal training in Quality disciplines (auditing, engineering, process improvement) as demonstrated through certification (ASQ, Lean Six Sigma, etc) highly preferred
- Technical proficiency at reviewing/auditing production records, reports and/or GMP related documentation.
- Ability to work within a team environment and willingness to contribute to the overall goals of the company.
- Ability to lead project teams
- Ability to handle multiple assignments and projects with competing priorities while independently managing time is critical.
- Good organizational skills, high level of attention to detail, excellent oral and written communication skills with the ability to interact at all levels.
- Ability to lift up to 35lbs.
- Must be willing to work off hour shifts and weekends as necessary.
The above statements are intended to describe the general nature and level of the work being performed by colleagues assigned to this position. This is not intended to be an exhaustive list of all responsibilities, duties, and skills required. Aquestive reserves the right to make changes to the job description whenever necessary.
As part of Aquestive’s employment process, final candidate will be required to complete a drug test and background check prior to employment commencing. Please Note: Aquestive is a drug-free workplace and has a drug free workplace policy in place.
Aquestive provides equal employment opportunities to all colleagues and applicants for employment and prohibits discrimination and harassment of any type without regard to race, color, religion, age, sex, national origin, disability status, genetics, protected veteran status, sexual orientation, gender identity or expression, or any other characteristic protected by federal, state or local laws.