23 Manufacturing jobs in Peekskill
Manufacturing Supervisor
Posted today
Job Viewed
Job Description
We are a leading innovator in the high-tech manufacturing industry, dedicated to producing cutting-edge products with precision and efficiency. Our commitment to quality and innovation drives our success, and we are seeking a skilled Manufacturing Supervisor to join our dynamic team.
Job Overview
We are looking for an experienced Manufacturing Supervisor to oversee production operations across multiple shifts. The ideal candidate will have a strong background in LEAN manufacturing principles and a proven track record of driving operational excellence in a high-tech environment. This role requires leadership, problem-solving, and a commitment to maintaining high standards of safety, quality, and efficiency.
Key Responsibilities
+ Supervise Production Operations: Lead a team of operators and technicians across assigned shifts to ensure production goals are met while maintaining quality standards.
+ Implement LEAN Principles: Drive continuous improvement initiatives using LEAN manufacturing techniques, including 5S, Kaizen, and waste reduction strategies.
+ Ensure Safety and Compliance: Enforce safety protocols and ensure compliance with company policies, industry standards, and regulatory requirements.
+ Monitor Performance Metrics: Track key performance indicators (KPIs) such as output, quality, and downtime, and implement corrective actions as needed.
+ Team Development: Train, mentor, and motivate team members to enhance skills, foster teamwork, and promote a culture of accountability.
+ Collaborate Across Departments: Work with engineering, quality assurance, and supply chain teams to optimize production processes and resolve issues.
+ Shift Management: Oversee scheduling, resource allocation, and workflow to ensure smooth operations across multiple shifts.
Qualifications
+ Experience:
+ Minimum of 5 years of supervisory experience in a manufacturing environment, preferably in high-tech or electronics industries.
+ Extensive experience with LEAN manufacturing principles (certification in LEAN or Six Sigma is highly preferred).
+ Education: Bachelor's degree in engineering, manufacturing, or a related field preferred, or equivalent professional experience.
+ Skills:
+ Strong leadership and team management abilities.
+ Proficiency in problem-solving and root cause analysis.
+ Familiarity with ERP systems and production planning tools.
+ Excellent communication and interpersonal skills.
+ Availability: Willingness to work flexible hours across 1st, 2nd, or 3rd shifts, including weekends as needed.
+ Physical Requirements: Ability to stand, walk, and perform hands-on tasks in a manufacturing environment.
Preferred Qualifications
+ Certification in LEAN manufacturing or Six Sigma (Green Belt or higher).
+ Experience in high-tech industries such as semiconductors, aerospace, or advanced electronics.
+ Knowledge of automated manufacturing systems and Industry 4.0 technologies.
Why Join Us?
+ Competitive Compensation: Attractive salary and comprehensive benefits package, including health, dental, and retirement plans.
+ Career Growth: Opportunities for professional development and advancement within a fast-growing company.
+ Innovative Environment: Work with cutting-edge technology in a collaborative, forward-thinking team.
+ Work-Life Balance: Flexible shift options and a commitment to employee well-being.
Pay and Benefits
The pay range for this position is $7000.00 - $7000.00/yr.
Innovative company offering competitive salaries, comprehensive health plans, generous PTO, 401(k) matching, and a vibrant, inclusive culture.
Workplace Type
This is a fully onsite position in Danbury,CT.
Application Deadline
This position is anticipated to close on Jul 25, 2025.
About Actalent
Actalent is a global leader in engineering and sciences services and talent solutions. We help visionary companies advance their engineering and science initiatives through access to specialized experts who drive scale, innovation and speed to market. With a network of almost 30,000 consultants and more than 4,500 clients across the U.S., Canada, Asia and Europe, Actalent serves many of the Fortune 500.
The company is an equal opportunity employer and will consider all applications without regard to race, sex, age, color, religion, national origin, veteran status, disability, sexual orientation, gender identity, genetic information or any characteristic protected by law.
If you would like to request a reasonable accommodation, such as the modification or adjustment of the job application process or interviewing due to a disability, please email (% ) for other accommodation options.
Manufacturing Supervisor
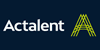
Posted today
Job Viewed
Job Description
We are a leading innovator in the high-tech manufacturing industry, dedicated to producing cutting-edge products with precision and efficiency. Our commitment to quality and innovation drives our success, and we are seeking a skilled Manufacturing Supervisor to join our dynamic team.
Job Overview
We are looking for an experienced Manufacturing Supervisor to oversee production operations across multiple shifts. The ideal candidate will have a strong background in LEAN manufacturing principles and a proven track record of driving operational excellence in a high-tech environment. This role requires leadership, problem-solving, and a commitment to maintaining high standards of safety, quality, and efficiency.
Key Responsibilities
+ Supervise Production Operations: Lead a team of operators and technicians across assigned shifts to ensure production goals are met while maintaining quality standards.
+ Implement LEAN Principles: Drive continuous improvement initiatives using LEAN manufacturing techniques, including 5S, Kaizen, and waste reduction strategies.
+ Ensure Safety and Compliance: Enforce safety protocols and ensure compliance with company policies, industry standards, and regulatory requirements.
+ Monitor Performance Metrics: Track key performance indicators (KPIs) such as output, quality, and downtime, and implement corrective actions as needed.
+ Team Development: Train, mentor, and motivate team members to enhance skills, foster teamwork, and promote a culture of accountability.
+ Collaborate Across Departments: Work with engineering, quality assurance, and supply chain teams to optimize production processes and resolve issues.
+ Shift Management: Oversee scheduling, resource allocation, and workflow to ensure smooth operations across multiple shifts.
Qualifications
+ Experience:
+ Minimum of 5 years of supervisory experience in a manufacturing environment, preferably in high-tech or electronics industries.
+ Extensive experience with LEAN manufacturing principles (certification in LEAN or Six Sigma is highly preferred).
+ Education: Bachelor's degree in engineering, manufacturing, or a related field preferred, or equivalent professional experience.
+ Skills:
+ Strong leadership and team management abilities.
+ Proficiency in problem-solving and root cause analysis.
+ Familiarity with ERP systems and production planning tools.
+ Excellent communication and interpersonal skills.
+ Availability: Willingness to work flexible hours across 1st, 2nd, or 3rd shifts, including weekends as needed.
+ Physical Requirements: Ability to stand, walk, and perform hands-on tasks in a manufacturing environment.
Preferred Qualifications
+ Certification in LEAN manufacturing or Six Sigma (Green Belt or higher).
+ Experience in high-tech industries such as semiconductors, aerospace, or advanced electronics.
+ Knowledge of automated manufacturing systems and Industry 4.0 technologies.
Why Join Us?
+ Competitive Compensation: Attractive salary and comprehensive benefits package, including health, dental, and retirement plans.
+ Career Growth: Opportunities for professional development and advancement within a fast-growing company.
+ Innovative Environment: Work with cutting-edge technology in a collaborative, forward-thinking team.
+ Work-Life Balance: Flexible shift options and a commitment to employee well-being.
Pay and Benefits
The pay range for this position is $7000.00 - $7000.00/yr.
Innovative company offering competitive salaries, comprehensive health plans, generous PTO, 401(k) matching, and a vibrant, inclusive culture.
Workplace Type
This is a fully onsite position in Danbury,CT.
Application Deadline
This position is anticipated to close on Jul 18, 2025.
About Actalent
Actalent is a global leader in engineering and sciences services and talent solutions. We help visionary companies advance their engineering and science initiatives through access to specialized experts who drive scale, innovation and speed to market. With a network of almost 30,000 consultants and more than 4,500 clients across the U.S., Canada, Asia and Europe, Actalent serves many of the Fortune 500.
The company is an equal opportunity employer and will consider all applications without regard to race, sex, age, color, religion, national origin, veteran status, disability, sexual orientation, gender identity, genetic information or any characteristic protected by law.
If you would like to request a reasonable accommodation, such as the modification or adjustment of the job application process or interviewing due to a disability, please email (% ) for other accommodation options.
Quality Control Inspector
Posted 14 days ago
Job Viewed
Job Description
If you've inquired to HumanEdge in the past, please use the same email to help shorten the inquiry process. If you've never inquired or don't remember, you may use any valid email address. Email Apply with Indeed Application Process Upon completing the application process, one of our representatives will contact you shortly. This initial phone conversation is an important opportunity for you to get all of your questions answered and for us to meet your needs as quickly and efficiently as possible. Quality Control Inspector Ref: 311625 Type: Contract Location: Yonkers, NY Job Level: Experienced Non-Manager Pay: $24.00 - $27.00 Opportunity Description Performs Quality Control (QC) inspection on parts and sub-assemblies of rail cars. Performs visual inspection of parts and equipment to ensure conformance to quality standards and to identify non-conformance where it occurs. Performs all work according to engineering drawings, written work procedures, and verbal and written instructions. Company Information Rail Infrastructure Management Services Job Duties Uses scales, tape, calipers, micrometers, combination-square and other measuring equipment to inspect parts, equipment, and their proper installation to rail car body. Has the capability of using English and Metric systems of measurement. Records data and findings from inspections in inspection reports and related documentation with a high degree of accuracy, completeness, and attention to detail. Demonstrates an excellent mechanical aptitude. The QC Inspector must be able to read and interpret all engineering drawings and blueprints, and has a demonstrated proficiency in all inspection phases listed below: Receiving Part Fabrication Metal Matching Sub assembly Shell Assembly Truck Assembly & Test Interior and Cab Exterior Under-floor Source Experience & Skills Required Must have, at minimum, two (2) years work experience in a QC Inspection field. Must be able to work independently and to conduct the final inspection of an entire rail car. Must be capable of using measuring instruments including, but not limited to, tape measures, calipers, micrometers, etc. Must read, write, and speak English and know how to read engineering drawings (blueprints). Must be proficient in the English measurement system and be able to learn the Metric system of measurement within a specified period of time. Must be capable of working in an active manufacturing environment. #J-18808-Ljbffr
Quality Control Engineer
Posted today
Job Viewed
Job Description
The Quality Control Engineer operates as the quality partner with manufacturing engineering, focusing on incoming materials inspection processes, root cause analysis of production issues to enhance yield improvements, and revising documentation to support quality engineering.
Responsibilities
+ Conduct inspections of purchased parts and subassemblies using standard inspection tools such as calipers and hard gages.
+ Accurately document the results of quality control inspections and testing.
+ Maintain all controlled document files and test records.
+ Assist in creating and updating inspection templates and tools.
+ Evaluate problems and make initial recommendations within quality engineering and manufacturing engineering.
+ Demonstrate experience as a Change Agent by successfully implementing process improvements and SPC metrics in a technical manufacturing environment.
Essential Skills
+ Quality control
+ Inspection
+ Quality engineering
+ Quality assurance
+ Root cause analysis
+ Electronics manufacturing
+ Quality management system
+ Use of inspection equipment like calipers and gages
Additional Skills & Qualifications
+ Degree in engineering or physical sciences preferred: electrical, industrial, manufacturing, materials science, or mechanical engineering, or electrical technology
+ Minimum of five years of technical experience in Manufacturing and Quality Control
+ Practical competence in Six Sigma analytical tools and Lean Manufacturing methods
+ Experience working in an electronics manufacturing facility strongly preferred
+ Knowledge of MIL-Specs and MIL-STDs is a plus
+ Strong analytical ability and computer skills
+ Strong MS Office skills, specifically Word, Excel, PowerPoint, and Outlook
Work Environment
This position is based in Stony Point, NY, and is fully onsite. The role follows a business casual dress code with an 8 am start time.
Pay and Benefits
The pay range for this position is $6000.00 - $8000.00/yr.
Direct Hire - Growing lighting/electronics company. Small engineering team; lots of development and collaboration across teams. Great benefits and employee offerings including medical, dental, visiion benefits, and paid holidays and PTO.
Workplace Type
This is a fully onsite position in Stony Point,NY.
Application Deadline
This position is anticipated to close on Jul 30, 2025.
About Actalent
Actalent is a global leader in engineering and sciences services and talent solutions. We help visionary companies advance their engineering and science initiatives through access to specialized experts who drive scale, innovation and speed to market. With a network of almost 30,000 consultants and more than 4,500 clients across the U.S., Canada, Asia and Europe, Actalent serves many of the Fortune 500.
The company is an equal opportunity employer and will consider all applications without regard to race, sex, age, color, religion, national origin, veteran status, disability, sexual orientation, gender identity, genetic information or any characteristic protected by law.
If you would like to request a reasonable accommodation, such as the modification or adjustment of the job application process or interviewing due to a disability, please email (% ) for other accommodation options.
Quality Control Engineer
Posted today
Job Viewed
Job Description
The Quality Control Engineer operates as the quality partner with manufacturing engineering, focusing on incoming materials inspection processes, root cause analysis of production issues to enhance yield improvements, and revising documentation to support quality engineering.
Responsibilities
+ Conduct inspections of purchased parts and subassemblies using standard inspection tools such as calipers and hard gages.
+ Accurately document the results of quality control inspections and testing.
+ Maintain all controlled document files and test records.
+ Assist in creating and updating inspection templates and tools.
+ Evaluate problems and make initial recommendations within quality engineering and manufacturing engineering.
+ Demonstrate experience as a Change Agent by successfully implementing process improvements and SPC metrics in a technical manufacturing environment.
Essential Skills
+ Quality control
+ Inspection
+ Quality engineering
+ Quality assurance
+ Root cause analysis
+ Electronics manufacturing
+ Quality management system
+ Use of inspection equipment like calipers and gages
Additional Skills & Qualifications
+ Degree in engineering or physical sciences preferred: electrical, industrial, manufacturing, materials science, or mechanical engineering, or electrical technology
+ Minimum of five years of technical experience in Manufacturing and Quality Control
+ Practical competence in Six Sigma analytical tools and Lean Manufacturing methods
+ Experience working in an electronics manufacturing facility strongly preferred
+ Knowledge of MIL-Specs and MIL-STDs is a plus
+ Strong analytical ability and computer skills
+ Strong MS Office skills, specifically Word, Excel, PowerPoint, and Outlook
Work Environment
This position is based in Stony Point, NY, and is fully onsite. The role follows a business casual dress code with an 8 am start time.
Pay and Benefits
The pay range for this position is $6000.00 - $8000.00/yr.
Direct Hire - Growing lighting/electronics company. Small engineering team; lots of development and collaboration across teams. Great benefits and employee offerings including medical, dental, visiion benefits, and paid holidays and PTO.
Workplace Type
This is a fully onsite position in Stony Point,NY.
Application Deadline
This position is anticipated to close on Jul 28, 2025.
About Actalent
Actalent is a global leader in engineering and sciences services and talent solutions. We help visionary companies advance their engineering and science initiatives through access to specialized experts who drive scale, innovation and speed to market. With a network of almost 30,000 consultants and more than 4,500 clients across the U.S., Canada, Asia and Europe, Actalent serves many of the Fortune 500.
The company is an equal opportunity employer and will consider all applications without regard to race, sex, age, color, religion, national origin, veteran status, disability, sexual orientation, gender identity, genetic information or any characteristic protected by law.
If you would like to request a reasonable accommodation, such as the modification or adjustment of the job application process or interviewing due to a disability, please email (% ) for other accommodation options.
Manufacturing Maintenance Manager
Posted 3 days ago
Job Viewed
Job Description
POSITION PURPOSE
The Maintenance Manager is responsible for leading the maintenance team across three shifts, ensuring equipment reliability, and implementing preventive and predictive maintenance programs to minimize downtime and maximize efficiency. This role involves overseeing personnel, budgeting for maintenance operations, and developing strategies to enhance asset performance while maintaining compliance with safety and regulatory standards.
*No calls or emails from third-party vendors or agencies will be accepted.*
ESSENTIAL FUNCTIONS AND BASIC DUTIES
Services Orangeburg, NY Production Department. Utilizes engineering as a resource for technical training, spare parts manufacturing and equipment upgrades. Budgetary responsibility for spare parts.
Maintenance Operations Management:
- Ensure minimal equipment downtime through efficient maintenance planning.
- Oversee spare parts inventory and procurement.
Personnel Management:
- Supervise, train, and develop maintenance staff.
- Assign work schedules and ensure productivity within the team.
- Promote a culture of safety, accountability, and continuous improvement.
- Conduct performance evaluations and provide coaching to employees.
Compliance & Safety:
- Ensure all maintenance activities comply with safety regulations and industry standards.
- Implement and enforce OSHA and environmental health and safety (EHS) standards.
- Develop and maintain documentation for audits and regulatory inspections.
Budgeting & Cost Control:
- Manage the maintenance department's budget and control operational costs.
- Identify opportunities for cost savings while maintaining quality standards.
- Negotiate contracts with service providers and equipment suppliers.
Continuous Improvement & Strategy:
- Implement best practices in maintenance management, including TPM (Total Productive Maintenance) and Lean methodologies.
- Work with production and quality teams to improve overall equipment efficiency (OEE).
- Stay updated on technological advancements and recommend improvements.
PERFORMANCE MEASUREMENTS
Workforce Development & Training:
- Identify skill gaps within the maintenance team and provide targeted training.
- Implement cross-training programs to enhance workforce flexibility.
- Encourage professional development through certifications and workshops.
Performance Management & Leadership Development:
- Set clear expectations and key performance indicators (KPIs) for staff.
- Conduct regular performance reviews and provide constructive feedback.
- Develop leadership programs to prepare high-potential employees for future management roles.
Succession Planning:
- Identify key roles within the maintenance department that require succession planning across three shifts and execute plan to support and develop company growth.
QUALIFICATIONS
EDUCATION/CERTIFICATION:
- B.S. in Engineering or equivalent work experience.
REQUIRED KNOWLEDGE:
- Must have general knowledge of packaging equipment principles.
- Basic understanding of electronics.
- Knowledge of computerized parts inventory systems and preventive maintenance programs.
EXPERIENCE REQUIRED:
- Five to ten years managing converting/packaging maintenance in a mechanically intense operation
- Prior experience in parts management, calibration, and purchasing required.
- Flexible packaging experience required.
SKILLS/ABILITIES:
- Ability to excel in a fast paced, 24 hour environment
- Ability to hire, train, and evaluate performance of reports
WORKING CONDITIONS:
- Manufacturing & Utility Environment - Regular work in plant, production, and utility areas, with exposure to equipment noise, humidity, and temperature variations.
- Physical Requirements - Requires standing, walking, climbing ladders, kneeling, and bending to inspect and maintain equipment. Must be able to lift up to 50 lbs. as needed.
- Protective Equipment (PPE) - Compliance with safety protocols, including PPE use (e.g., gloves, safety glasses, lab coat, or hearing protection) as required.
- Emergency & On-Call Situations - may be required based on business needs; availability to respond to urgent operational issues may be required.
- Fast-Paced, Regulated Environment - Work involves adherence to FDA, cGMP, and internal quality and safety protocols in a high-compliance setting.
SALARY RANGE
- $100,000 - $120,000 annually, plus bonus
PDI is pleased to offer a comprehensive and affordable benefits program to our associates, which includes:
- Medical & prescription drug coverage
- Dental / Vision plan
- 401(k) savings plan with company match
- Basic and supplemental life insurance
- Flexible Spending Accounts (FSAs)
- Short- and long-term disability benefits
- Health Advocacy Program / Employee Assistance Program (EAP)
Many other voluntary benefit plans such as: Legal assistance, critical illness, hospital indemnity and accident coverage, discounted home/auto/rental insurance, employee discounts and pet insurance
At PDI, we are also committed to helping our associates maintain a healthy and sustainable work/life balance and are proud to provide: Sick leave, generous vacation and holiday time, paid parental leave, summer hours, flex place/flex time options
Equal Opportunity Employer/Protected Veterans/Individuals with DisabilitiesThis employer is required to notify all applicants of their rights pursuant to federal employment laws.
For further information, please review the Know Your Rights notice from the Department of Labor.
Manufacturing Maintenance Manager
Posted 3 days ago
Job Viewed
Job Description
Description
Driven by a commitment to research, quality, and service, PDI provides innovative products, educational resources, training, and support to prevent infection transmission and promote health and wellness. Encompassing three areas, our Healthcare, Sani Professional and Contract manufacturing divisions, we develop, manufacture, and distribute leading edge products for North America and the world. We have several locations across the US and are looking for new Associates to join our team!
POSITION PURPOSE
The Maintenance Manager is responsible for leading the maintenance team across three shifts, ensuring equipment reliability, and implementing preventive and predictive maintenance programs to minimize downtime and maximize efficiency. This role involves overseeing personnel, budgeting for maintenance operations, and developing strategies to enhance asset performance while maintaining compliance with safety and regulatory standards.
No calls or emails from third-party vendors or agencies will be accepted.
ESSENTIAL FUNCTIONS AND BASIC DUTIES
Services Orangeburg, NY Production Department. Utilizes engineering as a resource for technical training, spare parts manufacturing and equipment upgrades. Budgetary responsibility for spare parts.
Maintenance Operations Management:
-
Ensure minimal equipment downtime through efficient maintenance planning.
-
Oversee spare parts inventory and procurement.
Personnel Management:
-
Supervise, train, and develop maintenance staff.
-
Assign work schedules and ensure productivity within the team.
-
Promote a culture of safety, accountability, and continuous improvement.
-
Conduct performance evaluations and provide coaching to employees.
Compliance & Safety:
-
Ensure all maintenance activities comply with safety regulations and industry standards.
-
Implement and enforce OSHA and environmental health and safety (EHS) standards.
-
Develop and maintain documentation for audits and regulatory inspections.
Budgeting & Cost Control:
-
Manage the maintenance department’s budget and control operational costs.
-
Identify opportunities for cost savings while maintaining quality standards.
-
Negotiate contracts with service providers and equipment suppliers.
Continuous Improvement & Strategy:
-
Implement best practices in maintenance management, including TPM (Total Productive Maintenance) and Lean methodologies.
-
Work with production and quality teams to improve overall equipment efficiency (OEE).
-
Stay updated on technological advancements and recommend improvements.
PERFORMANCE MEASUREMENTS
Workforce Development & Training:
-
Identify skill gaps within the maintenance team and provide targeted training.
-
Implement cross-training programs to enhance workforce flexibility.
-
Encourage professional development through certifications and workshops.
Performance Management & Leadership Development:
-
Set clear expectations and key performance indicators (KPIs) for staff.
-
Conduct regular performance reviews and provide constructive feedback.
-
Develop leadership programs to prepare high-potential employees for future management roles.
Succession Planning:
- Identify key roles within the maintenance department that require succession planning across three shifts and execute plan to support and develop company growth.
QUALIFICATIONS
EDUCATION/CERTIFICATION:
- B.S. in Engineering or equivalent work experience.
REQUIRED KNOWLEDGE:
-
Must have general knowledge of packaging equipment principles.
-
Basic understanding of electronics.
-
Knowledge of computerized parts inventory systems and preventive maintenance programs.
EXPERIENCE REQUIRED:
-
Five to ten years managing converting/packaging maintenance in a mechanically intense operation
-
Prior experience in parts management, calibration, and purchasing required.
-
Flexible packaging experience required.
SKILLS/ABILITIES:
-
Ability to excel in a fast paced, 24 hour environment
-
Ability to hire, train, and evaluate performance of reports
WORKING CONDITIONS:
-
Manufacturing & Utility Environment – Regular work in plant, production, and utility areas, with exposure to equipment noise, humidity, and temperature variations.
-
Physical Requirements – Requires standing, walking, climbing ladders, kneeling, and bending to inspect and maintain equipment. Must be able to lift up to 50 lbs. as needed.
-
Protective Equipment (PPE) – Compliance with safety protocols, including PPE use (e.g., gloves, safety glasses, lab coat, or hearing protection) as required.
-
Emergency & On-Call Situations – may be required based on business needs; availability to respond to urgent operational issues may be required.
-
Fast-Paced, Regulated Environment – Work involves adherence to FDA, cGMP, and internal quality and safety protocols in a high-compliance setting.
SALARY RANGE
- $100,000 - $120,000 annually, plus bonus
PDI is pleased to offer a comprehensive and affordable benefits program to our associates, which includes:
-
Medical & prescription drug coverage
-
Dental / Vision plan
-
401(k) savings plan with company match
-
Basic and supplemental life insurance
-
Flexible Spending Accounts (FSAs)
-
Short- and long-term disability benefits
-
Health Advocacy Program / Employee Assistance Program (EAP)
Many other voluntary benefit plans such as: Legal assistance, critical illness, hospital indemnity and accident coverage, discounted home/auto/rental insurance, employee discounts and pet insurance
At PDI, we are also committed to helping our associates maintain a healthy and sustainable work/life balance and are proud to provide: Sick leave, generous vacation and holiday time, paid parental leave, summer hours, flex place/flex time options
Equal Opportunity Employer/Protected Veterans/Individuals with Disabilities
This employer is required to notify all applicants of their rights pursuant to federal employment laws. For further information, please review the Know Your Rights ( notice from the Department of Labor.
Be The First To Know
About the latest Manufacturing Jobs in Peekskill !
Project Manager- Manufacturing
Posted today
Job Viewed
Job Description
Job Type Full-timeDescriptionJob PurposeThe Project Manager is responsible for supporting the management of both internal and external projects. This includes but is not limited to assisting with customer interfaces, internal & external qualifications, execution of project deliverables, and project tracking. Duties and ResponsibilitiesManage all aspects of both internal and external projects to ensure timely and successful project completion.Have a working understanding of the technical aspects of projects in order to foster project development and advancement.Interface and build relationships with team members across multiple disciplines through the design, building, installation, qualification, and verification of equipment.Actively listen, probe, and identify concerns. Develop credibility, loyalty, trust, and commitment.Manage changes to the project scope, project schedule, and project costs using appropriate verification techniques.Ensure that all projects are delivered on-time, within scope and within budget.Lead team meetings from project kickoff through completion.Monitor resource availability and allocation.Develop a detailed project plan to monitor and track progress.Measure project performance using appropriate tools.Report and escalate to management as needed.Other duties as assigned. RequirementsB.S. in Engineering or equivalent technical field.Years Experience: 5+ years in project management.Experience in a manufacturing environment a plus.Pay: $90,000-$140,000/yearBenefits:Eligible after 1st day: Paid holidays Employee Assistance ProgramEligible after 90-day probation period:Medical, Dental, Vision, Basic Life/AD&D Insurance, Voluntary Term Life/AD&D InsuranceHealth Savings Account (HSA), Flexible Spending Account (FSA), Dependent Care Account, Commuter Transportation Management Account Vacation timeSick timeEligible after 1 year of service: 401(k) with Employer MatchPotential for discretionary bonusThe final pay offered to a successful candidate will be dependent on several factors that may include but are not limited to the type and years of experience within the job, the type of years and experience within the industry, education, etc.We're proud to be an equal opportunity employer. This means we actively pursue ways to celebrate our differences and don't discriminate based on an individual's race (including traits historically associated with race, such as hair texture, hair type, and protective hairstyles including braids, locks, and twists), creed, national origin, nationality, religion, ancestry, age (40 or over), sex (including pregnancy), familial status, marital status, civil union or domestic partnership status, affectional or sexual orientation, gender identity or expression, mental or physical disability (including perceived disability, AIDS, and HIV status), atypical hereditary cellular or blood trait, genetic information, because of liability for service in military, status as a smoker or non-smoker, status as a registered medical marijuana user, or any unlawful criterion existing under applicable federal, state, or local laws. If you need assistance or an accommodation due to a disability, contact us at
Senior Manufacturing Engineer

Posted 10 days ago
Job Viewed
Job Description
Location: Orangeburg, NY
Type: Contract (1 year)
Compensation: $55 hourly
Contractor Work Model: Onsite
Hours : Monday through Friday (8AM to 430PM)
SENIOR MANUFACTURING ENGINEER
RESPONSIBILITIES
+ Responsible for the resolution of production process issues utilizing problem solving techniques to analyze, identify root cause(s), develop and implement solutions. (lead Remediation Efforts)
+ May be required to act as Product Champion for a specific product or product line with the following leadership responsibilities: The focal point in operations for the products which they have responsibility for.
+ Leads the resolution of production process issues utilizing problem solving techniques to analyze, identify root cause(s), develop and implement solutions.
+ Leads the process engineering and production support activities required for the manufacture of a product line.
+ Provides technical support and leadership for continuous improvement team efforts focused on process improvement and improvements to product manufacturability. (Lead on Projects)
+ Provides technical leadership and hands-on engineering support, including specification and implementation of assembly/test methods and process optimization.
+ Provides technical support for continuous improvement efforts conducting root cause analysis then formulating and implementing corrective action proposals.
+ Responsible for establishing the Manufacturing Quality Plan (MQP) for a product or product line including process flow, production floor layout, equipment, line balancing, etc.
+ Writes process procedures, change orders, equipment specifications, validation plans, and reports.
+ Performs research on technology, equipment and tooling to improve process quality, yield or cost; Generates proposals for purchase and implementation, including cost of ownership, ROI and benefit analysis.
+ Performs engineering design of test equipment, assembly equipment, fixtures and tools; Performs IQ/OQ/PQ validation activities.
+ Participates in the introduction of new products into manufacturing; Collaborate with R&D and suppliers to improve product robustness and manufacturability both pre- and post-release.
+ Supervises (as assigned) personnel in classifications below that of Senior Mfg. Engineer.
+ May lead or participate in Lean Six Sigma projects of significant scope and complexity
QUALIFICATIONS
+ Chemical Engineering or Mechanical Engineering Degree
+ 10+ years of experience in IVD Diagnostic Medical Device or Pharmaceutical Exp. Leading Remediation Efforts
+ Experienced in performing GAP Assessments related to production discrepancies in production documentation
+ Extensive experience working with SPMs (Standard Production Methods) and SOPs within an SAP environment
+ Open to adapting to other ERP systems; currently proficient in SAP for retrieving and updating SOPs and SPMs
+ Skilled in executing corrective actions and initiating/documenting change orders
System One, and its subsidiaries including Joulé, ALTA IT Services, and Mountain Ltd., are leaders in delivering outsourced services and workforce solutions across North America. We help clients get work done more efficiently and economically, without compromising quality. System One not only serves as a valued partner for our clients, but we offer eligible employees health and welfare benefits coverage options including medical, dental, vision, spending accounts, life insurance, voluntary plans, as well as participation in a 401(k) plan.
System One is an Equal Opportunity Employer. All qualified applicants will receive consideration for employment without regard to race, color, religion, sex (including pregnancy, childbirth, or related medical conditions), sexual orientation, gender identity, age, national origin, disability, family care or medical leave status, genetic information, veteran status, marital status, or any other characteristic protected by applicable federal, state, or local law.
#M1
#LI-JJ1
Ref: #558-Scientific
System One, and its subsidiaries including Joulé, ALTA IT Services, CM Access, TPGS, and MOUNTAIN, LTD., are leaders in delivering workforce solutions and integrated services across North America. We help clients get work done more efficiently and economically, without compromising quality. System One not only serves as a valued partner for our clients, but we offer eligible full-time employees health and welfare benefits coverage options including medical, dental, vision, spending accounts, life insurance, voluntary plans, as well as participation in a 401(k) plan.
System One is an Equal Opportunity Employer. All qualified applicants will receive consideration for employment without regard to race, color, religion, sex (including pregnancy, childbirth, or related medical conditions), sexual orientation, gender identity, age, national origin, disability, family care or medical leave status, genetic information, veteran status, marital status, or any other characteristic protected by applicable federal, state, or local law.
Senior Manufacturing Engineer

Posted 10 days ago
Job Viewed
Job Description
Hours: 8:00am-4:30pm
Onsite: 100% onsite
Duration: 1+ year contract
Location: Orangeburg NY
Requirements:
+ 10+ years of experience in IVD Diagnostic Medical Device or Pharmaceutical Exp.
+ Chemical Engineering or Mechanical Engineering Degree
Responsibilities:
+ Responsible for the resolution of production process issues utilizing problem solving techniques to analyze, identify root cause(s), develop and implement solutions. (lead Remediation Efforts)
+ May be required to act as Product Champion for a specific product or product line with the following leadership responsibilities: The focal point in operations for the products which they have responsibility for.
+ Leads the resolution of production process issues utilizing problem solving techniques to analyze, identify root cause(s), develop and implement solutions.
+ Leads the process engineering and production support activities required for the manufacture of a product line.
+ Provides technical support and leadership for continuous improvement team efforts focused on process improvement and improvements to product manufacturability. (Lead on Projects)
+ Provides technical leadership and hands-on engineering support, including specification and implementation of assembly/test methods and process optimization.
+ Provides technical support for continuous improvement efforts conducting root cause analysis then formulating and implementing corrective action proposals.
+ Responsible for establishing the Manufacturing Quality Plan (MQP) for a product or product line including process flow, production floor layout, equipment, line balancing, etc.
+ Writes process procedures, change orders, equipment specifications, validation plans, and reports.
+ Performs research on technology, equipment and tooling to improve process quality, yield or cost; Generates proposals for purchase and implementation, including cost of ownership, ROI and benefit analysis.
+ Performs engineering design of test equipment, assembly equipment, fixtures and tools; Performs IQ/OQ/PQ validation activities.
+ Participates in the introduction of new products into manufacturing; Collaborate with R&D and suppliers to improve product robustness and manufacturability both pre- and post-release.
+ Supervises (as assigned) personnel in classifications below that of Senior Mfg. Engineer.
+ May lead or participate in Lean Six Sigma projects of significant scope and complexity
#M-3
#LI-DS1
Ref: #558-Scientific
System One, and its subsidiaries including Joulé, ALTA IT Services, CM Access, TPGS, and MOUNTAIN, LTD., are leaders in delivering workforce solutions and integrated services across North America. We help clients get work done more efficiently and economically, without compromising quality. System One not only serves as a valued partner for our clients, but we offer eligible full-time employees health and welfare benefits coverage options including medical, dental, vision, spending accounts, life insurance, voluntary plans, as well as participation in a 401(k) plan.
System One is an Equal Opportunity Employer. All qualified applicants will receive consideration for employment without regard to race, color, religion, sex (including pregnancy, childbirth, or related medical conditions), sexual orientation, gender identity, age, national origin, disability, family care or medical leave status, genetic information, veteran status, marital status, or any other characteristic protected by applicable federal, state, or local law.