35 Manufacturing jobs in Puyallup
Manufacturing Manager
Posted 5 days ago
Job Viewed
Job Description
Join to apply for the Manufacturing Manager role at Oldcastle BuildingEnvelope
4 days ago Be among the first 25 applicants
Join to apply for the Manufacturing Manager role at Oldcastle BuildingEnvelope
Get AI-powered advice on this job and more exclusive features.
Direct message the job poster from Oldcastle BuildingEnvelope
Manufacturing Manager Anodizing - Midway, TN
Come Join Us!
From apartments in New York to hospitals and stadiums in Dallas, libraries at prestigious universities to creating modern retail experiences, our teams contribute architectural glass and building products to projects that shape the way people live, work, heal, learn, and play. At OBE, the work of our employees truly matters. With over 6,500 employees, we operate more than 80 manufacturing and distribution facilities in five countries. You can see some of our favorite projects here.
Start your journey with OBE and help us build the future.
What Youll Get to Do
The Manufacturing Manager - Anodizing is focused on monitoring the manufacturing activities in accordance with engineering specifications, time schedules, expense budgets, quality standards, cost goals and employee safety / performance / development and reports to the Assistant General Manager.
This role is perfect for an individual who wants to learn, develop and perform in a safety oriented and team driven environment. A vital member of the Manufacturing Team, this is an opportunity to build a career with an industry leader.
Job responsibilities include:
- Supervise a diverse work group including the racking, unracking/inspecting, tank and crane operation, lab and wastewater
- Monitor and manage production
- Assist in development and maintain process documentation and work
- Facilitate problem solving efforts, identify root causes, implement solutions, audit and report results to the Anodize Manager and Maintenance
- Train employees and facilitate goal oriented continuous improvement processes to reduce waste and improve processes (Processes include, but are not limited to: OpEx, Lean and 5S techniques).
What We Are Looking For
- Strong supervisory and leadership skills
- Have a basic understanding of inorganic chemistry
- Ability to learn and understand the Anodizing process and Crane
- Experience with the Toyota Production System approach.
- Basic understanding of manufacturing and service-oriented business
What OBE Offers You
- Benefits that benefit you industry competitive benefits at the lowest cost to the employee
- Work-life balance PTO and holidays, including floating holidays you can choose
- Compensation that rewards your hard work A pay-for-performance culture with potential for annual raises and bonuses
- Training We will equip you with the knowledge and skills you need to succeed
OBE is an Affirmative Action and Equal Opportunity Employer.
EOE/Vet/Disability--If you want to know more, please click on this link.
Oldcastle BuildingEnvelope is an E-Verify Employer.
Seniority level- Seniority level Associate
- Employment type Full-time
- Job function Manufacturing
- Industries Wholesale Building Materials
Referrals increase your chances of interviewing at Oldcastle BuildingEnvelope by 2x
Inferred from the description for this jobNewport, TN $65,000.00-$0,000.00 2 weeks ago
Mosheim, TN 120,000.00- 170,000.00 1 day ago
Midway, TN 48,000.00- 65,000.00 3 weeks ago
Were unlocking community knowledge in a new way. Experts add insights directly into each article, started with the help of AI.
#J-18808-LjbffrDirector Manufacturing
Posted 12 days ago
Job Viewed
Job Description
Overview At Spacelabs Healthcare, you make a difference. Every member of our worldwide team plays an integral role in improving treatment and helping providers deliver exceptional care to their patients. From newborns to centenarians, more than 60 million people benefit each year from the advancements we make in patient monitoring and management, care coordination and clinical decision support. Driven by the belief that anyone who seeks care could be a member of our own family, our team is dedicated to solving the greatest challenges the healthcare system currently faces, including the need to enhance the patient experience, improve population health, reduce costs, support care team well-being and advance health equity. As part of our mission, we take pride in creating services and technologies that are personalized and tailored to support the needs of healthcare providers anywhere in the world. Because while we may not be at a patient's bedside, their health is still in our hands. Director of Manufacturing leads global manufacturing operations. Directs the development and implementation of activities to meet production and shipping goals while achieving cost and quality objectives. Develops manpower requirements based on forecasts and production guidelines, sets priorities for production schedules based on equipment, efficiency, forecast and materials supply. Ensures that actions are taken to address issues affecting manufacturing goals and quality and champions continuous improvement and lean initiatives. This position is 100% onsite and is based at Spacelabs Healthcare headquarters in Snoqualmie, Washingon Responsibilities Create and implement the strategy for manufacturing solutions to ensure timely and cost-effective production of quality products. Own warehouse, demand planning, production through order fulfillment ensuring OTD indicators. Work closely with R&D and Manufacturing Engineering to support the introduction of new products, configurations and ECOs into manufacturing. Partner with materials management to ensure the right parts are available at the right time to build product to meet customer needs. Ensure qualified processes are in place and maintained supporting test and inspection, including OEM and private labeled products. Prepare the budget; manage manufacturing and labor costs. Drive programs and new methodologies to improve profitability. Develop metrics and visual cues to communicate goals and promote achievement. Use metrics to communicate to management. Manage workforce planning activities, which includes both regular and temporary workers. Develop highly skilled and productive workforce with consistent alignment to processes and QMS / regulatory requirements. Develop procedures for on-boarding and maintaining training of manufacturing workforce, including regular skills assessment of the workforce. Champion awareness of quality standards and requirements. Lead audit preparedness and response. Uphold Spacelabs values of Customer Obsession, Ownership Mindset and Superior Results. Demonstrate behavior consistent with the Company's Code of Ethics and Conduct. Ensure that direct report(s) are trained and evaluated on their knowledge and adherence to the Company's values, Code of Ethics and Conduct, and applicable compliance policies. Manage, evaluate, and develop team of employees to meet functional deliverables and responsibilities. Complete company people management requirements. Exhibit manager core competencies. Participate, Lead and support the safety policies, procedures and the program to ensure a safe working environment for all employees Drive Lean initiatives including 5S, weekly GEMBA, and continuous improvement. Uphold the company's core values of Integrity, Innovation, Accountability, and Teamwork. Demonstrate behavior consistent with the company's Code of Ethics and Conduct. Ensure that direct report(s) are trained and evaluated on their knowledge and adherence to the company's values, Code of Ethics and Conduct, and applicable compliance policies. It is the responsibility of every employee to report to their manager or a member of senior management any quality problems or defects in order for corrective action to be implemented and to avoid recurrence of the problem. Duties may be modified or assigned at any time to meet the needs of the business. Qualifications 15+ years of manufacturing management experience, including at least 3 years in a senior manufacturing management capacity is required. Strong track record of leading successful manufacturing organizations. 5+ years of experience working in medical device manufacturing (knowledge of CFR Part 820 Quality System Regulation and relevant sub parts). 6+ years of direct people management experience. Ability to manage multiple, complex priorities within demanding timeframes. Strong project management skills. Process driven. Can train and manage an organization to follow processes consistently. Experienced user in Microsoft Office, Power BI, ERP, MES, PLM, eQMS and database usage required. Bilingual preferred. Strong presentation and communication skills. Effective communicator from line employees to external customers. Experience working positively and productively in a team environment. Highly collaborative. Can build trust. Proven ability to deliver results through others, both direct and matrixed. Proven ability to lead, develop, motivate, and hold others accountable. Proven ability to embrace change and to participate in change management in a leadership role. Must be able to work in the U.S. without visa sponsorship (e.g., H-1B visa status). #LI-Onsite Please review our benefits here: Life at OSI The specific programs and options available to any given employee may vary depending on eligibility factors such as geographic location and date of hire. Please note that the salary information shown above is a general guideline only. Salaries are based upon candidate experience and qualifications, as well as market and business considerations. NOTICE TO THIRD PARTY AGENCIES OSI Systems, Inc. and its subsidiaries (collectively "OSI") does not accept unsolicited resumes from recruiters or employment agencies. If any person or entity, including a recruiter or agency, submits any information, including any resume or information regarding any potential candidate, without a signed agreement in place with OSI, OSI explicitly reserves the right to use such information, and pursue and/or hire such candidates, without any financial obligation to the person, recruiter or agency. Any unsolicited information or resumes, including those submitted directly to hiring managers, are considered and deemed to be the property of OSI. Equal Opportunity Employer - Disability and Veteran Know Your Rights Poster Link: OSI Systems, Inc. has three operating divisions: (a) Security, providing security and inspection systems, turnkey security screening solutions and related services; (b) Healthcare, providing patient monitoring, diagnostic cardiology and anesthesia systems; and (c) Optoelectronics and Manufacturing, providing specialized electronic components and electronic manufacturing services for original equipment manufacturers with applications in the defense, aerospace, medical and industrial markets, among others. #J-18808-Ljbffr
Director Manufacturing
Posted 12 days ago
Job Viewed
Job Description
Overview At Spacelabs Healthcare, you make a difference. Every member of our worldwide team plays an integral role in improving treatment and helping providers deliver exceptional care to their patients. From newborns to centenarians, more than 60 million people benefit each year from the advancements we make in patient monitoring and management, care coordination and clinical decision support. Driven by the belief that anyone who seeks care could be a member of our own family, our team is dedicated to solving the greatest challenges the healthcare system currently faces, including the need to enhance the patient experience, improve population health, reduce costs, support care team well-being and advance health equity. As part of our mission, we take pride in creating services and technologies that are personalized and tailored to support the needs of healthcare providers anywhere in the world. Because while we may not be at a patient’s bedside, their health is still in our hands. Director of Manufacturing leads global manufacturing operations. Directs the development and implementation of activities to meet production and shipping goals while achieving cost and quality objectives. Develops manpower requirements based on forecasts and production guidelines, sets priorities for production schedules based on equipment, efficiency, forecast and materials supply. Ensures that actions are taken to address issues affecting manufacturing goals and quality and champions continuous improvement and lean initiatives. This position is 100% onsite and is based at Spacelabs Healthcare headquarters in Snoqualmie, Washingon Responsibilities Create and implement the strategy for manufacturing solutions to ensure timely and cost-effective production of quality products. Own warehouse, demand planning, production through order fulfillment ensuring OTD indicators. Work closely with R&D and Manufacturing Engineering to support the introduction of new products, configurations and ECOs into manufacturing. Partner with materials management to ensure the right parts are available at the right time to build product to meet customer needs. Ensure qualified processes are in place and maintained supporting test and inspection, including OEM and private labeled products. Prepare the budget; manage manufacturing and labor costs. Drive programs and new methodologies to improve profitability. Develop metrics and visual cues to communicate goals and promote achievement. Use metrics to communicate to management. Manage workforce planning activities, which includes both regular and temporary workers. Develop highly skilled and productive workforce with consistent alignment to processes and QMS / regulatory requirements. Develop procedures for on-boarding and maintaining training of manufacturing workforce, including regular skills assessment of the workforce. Champion awareness of quality standards and requirements. Lead audit preparedness and response. Uphold Spacelabs values of Customer Obsession, Ownership Mindset and Superior Results. Demonstrate behavior consistent with the Company’s Code of Ethics and Conduct. Ensure that direct report(s) are trained and evaluated on their knowledge and adherence to the Company’s values, Code of Ethics and Conduct, and applicable compliance policies. Manage, evaluate, and develop team of employees to meet functional deliverables and responsibilities. Complete company people management requirements. Exhibit manager core competencies. Participate, Lead and support the safety policies, procedures and the program to ensure a safe working environment for all employees Drive Lean initiatives including 5S, weekly GEMBA, and continuous improvement. Uphold the company’s core values of Integrity, Innovation, Accountability, and Teamwork. Demonstrate behavior consistent with the company’s Code of Ethics and Conduct. Ensure that direct report(s) are trained and evaluated on their knowledge and adherence to the company’s values, Code of Ethics and Conduct, and applicable compliance policies. It is the responsibility of every employee to report to their manager or a member of senior management any quality problems or defects in order for corrective action to be implemented and to avoid recurrence of the problem. Duties may be modified or assigned at any time to meet the needs of the business. Qualifications 15+ years of manufacturing management experience, including at least 3 years in a senior manufacturing management capacity is required. Strong track record of leading successful manufacturing organizations. 5+ years of experience working in medical device manufacturing. 6+ years of direct people management experience. Ability to manage multiple, complex priorities within demanding timeframes. Strong project management skills. Process driven. Can train and manage an organization to follow processes consistently. Experienced user in Microsoft Office, Power BI, ERP, MES, PLM, eQMS and database usage required. Bilingual preferred. Strong presentation and communication skills. Effective communicator from line employees to external customers. Experience working positively and productively in a team environment. Highly collaborative. Can build trust. Proven ability to deliver results through others, both direct and matrixed. Proven ability to lead, develop, motivate, and hold others accountable. Proven ability to embrace change and to participate in change management in a leadership role. Must be able to work in the U.S. without visa sponsorship (e.g., H-1B visa status). #LI-Onsite Please review our benefits here: Life at OSI The specific programs and options available to any given employee may vary depending on eligibility factors such as geographic location and date of hire. Please note that the salary information shown above is a general guideline only. Salaries are based upon candidate experience and qualifications, as well as market and business considerations. NOTICE TO THIRD PARTY AGENCIES OSI Systems, Inc. and its subsidiaries (collectively “OSI”) does not accept unsolicited resumes from recruiters or employment agencies. If any person or entity, including a recruiter or agency, submits any information, including any resume or information regarding any potential candidate, without a signed agreement in place with OSI, OSI explicitly reserves the right to use such information, and pursue and/or hire such candidates, without any financial obligation to the person, recruiter or agency. Any unsolicited information or resumes, including those submitted directly to hiring managers, are considered and deemed to be the property of OSI. Equal Opportunity Employer - Disability and Veteran Know Your Rights Poster Link: OSI Systems, Inc. has three operating divisions: (a) Security, providing security and inspection systems, turnkey security screening solutions and related services; (b) Healthcare, providing patient monitoring, diagnostic cardiology and anesthesia systems; and (c) Optoelectronics and Manufacturing, providing specialized electronic components and electronic manufacturing services for original equipment manufacturers with applications in the defense, aerospace, medical and industrial markets, among others. 15+ years of manufacturing management experience, including at least 3 years in a senior manufacturing management capacity is required. Strong track record of leading successful manufacturing organizations. 5+ years of experience working in medical device manufacturing. 6+ years of direct people management experience. Ability to manage multiple, complex priorities within demanding timeframes. Strong project management skills. Process driven. Can train and manage an organization to follow processes consistently. Experienced user in Microsoft Office, Power BI, ERP, MES, PLM, eQMS and database usage required. Bilingual preferred. Strong presentation and communication skills. Effective communicator from line employees to external customers. Experience working positively and productively in a team environment. Highly collaborative. Can build trust. Proven ability to deliver results through others, both direct and matrixed. Proven ability to lead, develop, motivate, and hold others accountable. Proven ability to embrace change and to participate in change management in a leadership role. Must be able to work in the U.S. without visa sponsorship (e.g., H-1B visa status). #LI-Onsite Please review our benefits here: Life at OSI The specific programs and options available to any given employee may vary depending on eligibility factors such as geographic location and date of hire. Please note that the salary information shown above is a general guideline only. Salaries are based upon candidate experience and qualifications, as well as market and business considerations. NOTICE TO THIRD PARTY AGENCIES OSI Systems, Inc. and its subsidiaries (collectively “OSI”) does not accept unsolicited resumes from recruiters or employment agencies. If any person or entity, including a recruiter or agency, submits any information, including any resume or information regarding any potential candidate, without a signed agreement in place with OSI, OSI explicitly reserves the right to use such information, and pursue and/or hire such candidates, without any financial obligation to the person, recruiter or agency. Any unsolicited information or resumes, including those submitted directly to hiring managers, are considered and deemed to be the property of OSI. Equal Opportunity Employer - Disability and Veteran Know Your Rights Poster Link: OSI Systems, Inc. has three operating divisions: (a) Security, providing security and inspection systems, turnkey security screening solutions and related services; (b) Healthcare, providing patient monitoring, diagnostic cardiology and anesthesia systems; and (c) Optoelectronics and Manufacturing, providing specialized electronic components and electronic manufacturing services for original equipment manufacturers with applications in the defense, aerospace, medical and industrial markets, among others. Create and implement the strategy for manufacturing solutions to ensure timely and cost-effective production of quality products. Own warehouse, demand planning, production through order fulfillment ensuring OTD indicators. Work closely with R&D and Manufacturing Engineering to support the introduction of new products, configurations and ECOs into manufacturing. Partner with materials management to ensure the right parts are available at the right time to build product to meet customer needs. Ensure qualified processes are in place and maintained supporting test and inspection, including OEM and private labeled products. Prepare the budget; manage manufacturing and labor costs. Drive programs and new methodologies to improve profitability. Develop metrics and visual cues to communicate goals and promote achievement. Use metrics to communicate to management. Manage workforce planning activities, which includes both regular and temporary workers. Develop highly skilled and productive workforce with consistent alignment to processes and QMS / regulatory requirements. Develop procedures for on-boarding and maintaining training of manufacturing workforce, including regular skills assessment of the workforce. Champion awareness of quality standards and requirements. Lead audit preparedness and response. Uphold Spacelabs values of Customer Obsession, Ownership Mindset and Superior Results. Demonstrate behavior consistent with the Company’s Code of Ethics and Conduct. Ensure that direct report(s) are trained and evaluated on their knowledge and adherence to the Company’s values, Code of Ethics and Conduct, and applicable compliance policies. Manage, evaluate, and develop team of employees to meet functional deliverables and responsibilities. Complete company people management requirements. Exhibit manager core competencies. Participate, Lead and support the safety policies, procedures and the program to ensure a safe working environment for all employees Drive Lean initiatives including 5S, weekly GEMBA, and continuous improvement. Uphold the company’s core values of Integrity, Innovation, Accountability, and Teamwork. Demonstrate behavior consistent with the company’s Code of Ethics and Conduct. Ensure that direct report(s) are trained and evaluated on their knowledge and adherence to the company’s values, Code of Ethics and Conduct, and applicable compliance policies. It is the responsibility of every employee to report to their manager or a member of senior management any quality problems or defects in order for corrective action to be implemented and to avoid recurrence of the problem. Duties may be modified or assigned at any time to meet the needs of the business. #J-18808-Ljbffr
Manufacturing Director
Posted 12 days ago
Job Viewed
Job Description
Our Client Due to continued investment, growth and expansion, an opportunity has become available for a Manufacturing Director to have responsibility for overseeing all manufacturing operations to ensure efficient production, quality control, and cost-effective processes to keep the company at the forefront of their industry. This role will drive manufacturing excellence through inspiring teams and building a culture of quality, innovation, and continuous improvement across the Engineering and Manufacturing departments. The role would suit an ambitious Operations / Manufacturing leader who wants to join a fast growth niche manufacturing company where upon success there is a clear opportunity in time to develop to become the Managing Director. You will be joining a stable, well-invested, and growing company with a Managing Director who will offer excellent mentoring and support to help develop your career. Job Description Lead, mentor and develop the production, production engineering and quality teams (circa 60 employees). You will also have responsibility for the health and safety function. Continue to develop the operational strategy and approach to optimise operational efficiency/effectiveness and ensure compliance/certification within a safety critical industry. Drive a culture of customer experience and continuous improvement across all areas of responsibility. Ensure development opportunities for the teams through qualifications, skills development and mentoring providing guidance and an environment in which they can thrive and achieve their potential. Optimise efficiencies through cutting edge factory layout and to maximise operational productivity performance. Be a key member of the leadership team encouraging a culture of continuous improvement throughout the business. The Successful Applicant Engineering degree/equivalent qualification. A wealth of experience in manufacturing operations and leading successful teams. Leading abilities to inspire teams to achieve through mentoring, coaching, and support. Experience in implementing and driving through a culture of lean processing to optimise manufacturing processes. Project delivery experience optimising manufacturing processes through factory automation. Working in a high precision industry where compliance and certifications are essential. Knowledge of Safe Management of Manufacturing Operations (Safe Systems of Work). Located within commuting distance of Head Office in Kent or ability to relocate. What’s on Offer You will receive a competitive salary with broader benefits and the business. #J-18808-Ljbffr
Manufacturing Planner
Posted 7 days ago
Job Viewed
Job Description
Job Description
The Manufacturing Planner is responsible for creating comprehensive manufacturing plans that provide production operators with all necessary instructions and specifications to fabricate quality parts effectively. This role serves as the primary liaison regarding technical issues and involves interpreting customer specifications, blueprints, and visual aids for basic and complex planning. The planner will research and incorporate engineering changes into manufacturing plans, develop planning for new jobs, and modify existing jobs promptly. Collaboration with production teams to resolve manufacturing issues is essential, and the planner acts as a liaison between product lines and customer service cells.
Responsibilities
+ Create detailed manufacturing plans for production operators.
+ Serve as the primary liaison for technical issues.
+ Interpret customer specifications and blueprints.
+ Incorporate engineering changes into manufacturing plans.
+ Develop planning for new jobs and modify existing jobs.
+ Collaborate with production to resolve manufacturing issues.
+ Assist in identifying substitutes for raw materials.
+ Initiate and assist with changes to manufacturing plans.
+ Prioritize work to meet customer requirements and ensure on-time delivery.
+ Oversee document control to ensure electronic files are current.
+ Work within the JobBoss ERP system.
Essential Skills
+ Understanding of aerospace specifications.
+ Experience in blueprint reading.
+ 1-3 years of experience in production and manufacturing planning.
+ ITAR compliance.
Additional Skills & Qualifications
+ Familiarity in military specifications and drawings.
+ Cross-training and support for other team positions.
+ Knowledge of customer drawings and specs.
+ Ability to read measuring equipment such as micrometers and calipers.
+ Excellent organizational skills.
+ Fluency in English, both written and oral.
Work Environment
The role requires standing and using hands frequently to manipulate objects. Walking and standing are regular activities, with lifting requirements of up to 10 pounds regularly and 25 pounds occasionally. Vision abilities needed include close vision, distance vision, color vision, and depth perception. The work hours are from 4:30 AM to 1 PM, Monday through Friday. The position involves reading technical drawings and customer specifications, and communicating technical manufacturing processes to machinists and assemblers.
Pay and Benefits
The pay range for this position is $35.00 - $42.00/hr.
Eligibility requirements apply to some benefits and may depend on your job classification and length of employment. Benefits are subject to change and may be subject to specific elections, plan, or program terms. If eligible, the benefits available for this temporary role may include the following:
- Medical, dental & vision - Critical Illness, Accident, and Hospital - 401(k) Retirement Plan - Pre-tax and Roth post-tax contributions available - Life Insurance (Voluntary Life & AD&D for the employee and dependents) - Short and long-term disability - Health Spending Account (HSA) - Transportation benefits - Employee Assistance Program - Time Off/Leave (PTO, Vacation or Sick Leave)
Workplace Type
This is a fully onsite position in Auburn,WA.
Application Deadline
This position is anticipated to close on Jul 19, 2025.
About Aston Carter:
Aston Carter provides world-class corporate talent solutions to thousands of clients across the globe. Specialized in accounting, finance, human resources, talent acquisition, procurement, supply chain and select administrative professions, we extend the capabilities of industry-leading companies. We draw on our deep recruiting expertise and expansive network to meet the evolving needs of our clients and talent community with agility and excellence. With offices across the U.S., Canada, Asia Pacific and Europe, Aston Carter serves many of the Fortune 500. We are proud to be a ClearlyRated Best of Staffing® double diamond winner for both client and talent service.
The company is an equal opportunity employer and will consider all applications without regard to race, sex, age, color, religion, national origin, veteran status, disability, sexual orientation, gender identity, genetic information or any characteristic protected by law.
If you would like to request a reasonable accommodation, such as the modification or adjustment of the job application process or interviewing process due to a disability, please email (% ) for other accommodation options.
Manager - Stage Manufacturing
Posted 2 days ago
Job Viewed
Job Description
A thriving economy in space is needed to make life on Earth more vibrant, sustainable, and equitable. Space technology will enable global access to information, solutions to climate change, answers to global food security, products that transform healthcare, clean energy production, and more. Today, rocket launch options are slow, expensive, and unreliable. Stoke is building the worlds most efficient fully and rapidly reusable rocket designed to fly daily that will radically increase access to space and open up the space economy to safeguard our precious home, Earth.
Description
We are seeking a full-time Manager to join our dynamic team. This purpose of this role is to design, build, and operate a prototype production line within the factory in Kent. You will be responsible for developing processes, designing tooling, and driving system level thinking into the product to enable the production of a fully reuseable rocket that is simple to produce. A qualified candidate will take a first principles approach to complex problems to move decisively through an iterative production line design from cutting sheet metal through shipping a fully integrated stage. This position will lead a team of technicians and engineers to create a product unlike any other in a timeline that cannot be matched. You must be ready to stay focused, move fast, self-direct, and learn on the fly.
Responsibilities
- Own the manufacturing of Nova Stage 1 and Stage 2 inclusive of primary structure fabrication through engine integration and shipping
- Hire and lead technicians (welders, fabricators, integrators) and engineers (process and tooling design)
- Own facility and tooling design, capital equipment purchases, and process development initiatives
- Maintain a culture of high integrity, high reliability execution
Qualifications
- Bachelors degree in mechanical, aerospace, or electrical engineering, or similar
- Exposure to new product introduction from design to implementation inclusive of hiring, training, building, and testing
- A system level understanding of integrated assemblies expertise in fluids, structures, or electrical systems
- Hands on time with technicians with a proven track record of motivating and inspiring creative thinking at the individual level
- Project management experience including developing budgets and schedules, and managing resources
- Demonstrated understanding of configuration management and change control
- 5+ years experience in a manufacturing environment
- Proficiency in process development and research
- Ability to lead
- Ability to follow
- Excellent written and verbal communication
- Willing to relocate to Seattle, WA
Benefits
- Medical, dental, vision and basic life insurance
- 401(k) match
- Paid time off
- Flexible scheduling
- Equity
Compensation
Target Levels:
- Level 3 Range: $123,000 - $84,000
- Level 4 Range: 144,100 - 240,100
- Level 5 Range: 168,100 - 312,200
Our job posts are intentionally written to attract a wide variety of experience levels, and we make decisions about the right fit on a per-candidate basis.
Your actual level and base salary will be decided based on your specific experience and skill level.
Equal Opportunity
The Company is an Equal Opportunity Employer, including with respect to disability and veteran status. It is committed to compliance with all equal opportunity laws, including the Immigration and Nationality Act (INA) and Title VII. It does not discriminate on the basis of nationality, race, citizenship, immigration status, or any other protected class when it comes to employment practices, including hiring.
Employment at the Company is contingent upon satisfactory completion of reference and backgroundchecks, and on your ability to prove your identity and authorization to work in the U.S. for the Company. Employees must comply with the United States Citizenship and Immigration Services employment verification requirements, and, therefore, they must complete an Employment Eligibility Verification Form I-9 at the start of employment and re-verify authorization to work periodically.
Separate from this I-9 process, this position entails access to certain technology and technical data that is restricted under U.S. export control laws and regulations. Employment or continued employment may be conditioned on your legal authorization to work with or have access to export control materials as necessary to perform your job.
#J-18808-LjbffrProgram Manager, Manufacturing
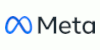
Posted 12 days ago
Job Viewed
Job Description
Manufacturing is a pillar within Meta's Delivery Team supporting data center construction. We exist to support the predictable delivery of capacity at scale through manufactured solutions.The Manufacturing Team's primary focus is supply chain engagement and optimization. We accept Manufacturing Informed Designed (MID) components and orchestrate their detailing and prototyping to optimum manufacturability then work with our partners in Delivery to plan logistics and integration to avoid challenges in construction.This team is comprised of strategic designers, strategic builders, tactical specialists, plus internal and external subject matter experts (SME) including preconstruction managers, contractors, schedulers, equipment reliability engineers, and sourcing specialists. This position will lead program management of all manufactured components in support of Meta's RPL project. This mega-project is of such scale that it requires a high-performing PM to drive strategic and tactical aspects of first-of-kind prototyping, logistics, and integration. Never before have we relied so heavily on offsite construction; a necessity here to deliver a project of this magnitude on an aggressive timeline. The successful candidate will be instrumental in ensuring the timely delivery of this capacity on what will be the largest project in Meta's history and one of a few of the largest data centers in the world.
**Required Skills:**
Program Manager, Manufacturing Responsibilities:
1. Program Management - Lead coordination, document, and anticipate program needs to ensure cost, schedule, and quality in concert with the mega-project construction
2. Primary Interface with the Manufacturing CAPs (Component Accountable PMs) - to coordinate on Supplier production (manufacturing execution) including configuring supply chain, production, scheduling, strategic inventory, logistics, and integration in collaboration with our delivery and quality teams
3. Interface with mega-project MOFE (Manufactured Owner Furnished Equipment) Onsite Logistics PM for logistical planning
4. Interface with mega-project MOFE Onsite Integration / Testing PM for planning and coordination
5. Manage GC (General Contractor) MOFE Coordinators for logistics, planning, coordination, reporting, lessons learned, etc.
6. Risk Matrix development, maintenance, and related reporting
7. Cost & Change Coordination with mega-project Meta designees including CM/PCA, ISCE, & MOFE CAPs
8. Schedule Development with Engineering/Scheduling, GCs, CAPs, & Suppliers
9. Regular Debriefs / Lessons Learned development, summary and communication to Engineering, Leadership, & XFNs (cross-functional partners)
10. Partner with cross functional teams on related efforts to ensure alignment and transparency across Design, Engineering, & Construction (DEC)
11. Partner closely with Sourcing Team for strategy and deployment of owner furnished equipment.
12. Partner with Global QA/QC Team to identify and strategically shift to the vendors and manufacturers, appropriate elements of the multi-trade integration and commissioning efforts to reduce onsite efforts. Your objective is to embed as much trade work and commissioning as is appropriate at the optimum points of fabrication from start through to the final point of integration.
13. Support team learning by bring lessons learned, vendors, new technology, and other topics to the group for exploration.
14. Travel approximately 40% Domestic Travel to construction and fabrication sites required (including minimal international travel as required)
**Minimum Qualifications:**
Minimum Qualifications:
15. Bachelor's degree or equivalent work experience in program management
16. 10+ years' experience in construction, manufacturing, and/or project planning
17. Experience in large scale construction management and/or scalable manufacturing
18. Manufacturing-for-construction background with understanding of lean manufacturing and supply-chain management plus knowledge of production machinery, processes, and standards in the field or industry experience with developing workflows and their associated flowcharts, schedules, and action plans
19. Experience building consensus and communicate effectively with a wide range of audiences (stakeholders to executive leadership).
20. Proven track record of adaptability and problem-solving in a dynamic work environment
21. Proficient working knowledge of Google Workspace and Bluebeam
**Preferred Qualifications:**
Preferred Qualifications:
22. Experience with off-site fabrication, pre-assembly and/or modularization of complex elements for construction (or off-shore) projects
23. Mission Critical, infrastructure, and/or data center construction experience
24. Experience working with blended architecture, engineering, manufacturing/assembly and construction teams
25. Software experience with eBuilder, Procore, Solidworks, Autodesk modeling software, Primavera P6, and/or BIM 360
26. Experience with LEAN tools (such as Choosing by Advantage, Last Planner/Pull Planning, Gemba, Kanban)
27. Experience working with Statistical Process Control (SPC), Just In Time (JIT) strategizing, and manufacturing data analytics.
28. PMP Certification
**Public Compensation:**
$144,000/year to $201,000/year + bonus + equity + benefits
**Industry:** Internet
**Equal Opportunity:**
Meta is proud to be an Equal Employment Opportunity and Affirmative Action employer. We do not discriminate based upon race, religion, color, national origin, sex (including pregnancy, childbirth, or related medical conditions), sexual orientation, gender, gender identity, gender expression, transgender status, sexual stereotypes, age, status as a protected veteran, status as an individual with a disability, or other applicable legally protected characteristics. We also consider qualified applicants with criminal histories, consistent with applicable federal, state and local law. Meta participates in the E-Verify program in certain locations, as required by law. Please note that Meta may leverage artificial intelligence and machine learning technologies in connection with applications for employment.
Meta is committed to providing reasonable accommodations for candidates with disabilities in our recruiting process. If you need any assistance or accommodations due to a disability, please let us know at
Be The First To Know
About the latest Manufacturing Jobs in Puyallup !
Manufacturing Quality Engineer
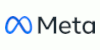
Posted 12 days ago
Job Viewed
Job Description
Meta Platforms, Inc. (Meta), formerly known as Facebook Inc., builds technologies that help people connect, find communities, and grow businesses. When Facebook launched in 2004, it changed the way people connect. Apps and services like Messenger, Instagram, and WhatsApp further empowered billions around the world. Now, Meta is moving beyond 2D screens toward immersive experiences like augmented and virtual reality to help build the next evolution in social technology. To apply, click "Apply to Job" online on this web page.
**Required Skills:**
Manufacturing Quality Engineer Responsibilities:
1. Develop the manufacturing and quality plans for cabling products for Meta's data centers, including copper, single mode fibre, and multimode fibre cabling, patch panels, cable runways, cable enclosures, and connectors.
2. Develop the manufacturing and quality plans for, IDC products such as Gen sets, Hot Aisle, Racks, UPS, PDUs, Busways, Load banks.
3. Evaluate manufacturing processes by applying knowledge of design, fabrication, assembly, tooling, and materials.
4. Participate in design reviews and provide feedback for DFM (design for manufacturability), DFT (design for testability), yield improvements, and quality control, and audit manufacturing sites to assess supplier's capabilities and implement manufacturing and quality best practices.
5. Drive Lean projects to improve manufacturing and data center processes to eliminate waste, reduce cost, and improve yield, and provide technical leadership and expertise within the supply chain teams during the hardware product lifecycle.
6. Ensure product and process quality targets are met by working with engineering to design test methods, establishing standards, and driving continuous improvement with manufacturers and equipment providers.
7. Improve manufacturing efficiency by analyzing and planning workflows, space requirements, and equipment layout, and prepare product and process reports by collecting, analyzing, and summarizing information and trends in manufacturing, field, and RMA data.
8. Knowledge of quality control techniques, including statistical process control (SPC), measurement system analysis (MSA), and failure mode and effects analysis (FMEA).
9. Knowledge of quality control techniques, including statistical process control (SPC), measurement system analysis (MSA), and failure mode and effects analysis (FMEA).
10. Familiarity with product lifecycle management (PLM) systems and enterprise resource planning (ERP) systems.
11. Experience in working with suppliers to ensure compliance to UL listing and EHS regulations.
12. Familiarity with quality management systems, such as ISO 9001 or similar standards.
13. Strong communication and negotiation skills to work with suppliers on resolving quality issues and improving performance.
14. Lead XFN Meta team and Manage supplier team for product delivery.
15. Telecommute from anywhere in the US permitted.
**Minimum Qualifications:**
Minimum Qualifications:
16. Requires a Master's degree in Computer Science, Electrical Engineering, Mechanical Engineering, or related field and 24 months of work experience in job offered or in a quality engineering-related occupation.
17. Requires 24 months of experience in the following:
18. 1. Driving root cause and corrective action for failures during manufacturing and operation
19. 2. Assisting in implementing failure analysis tools and processes
20. 3. Creating and maintaining all product process, quality, and technical training documentation, and BOMs
21. 4. Engineering change notifications, and manufacturing process changes through product lifecycle management tools
22. 5. PCBA assembly and test processes
23. 6. Conduct product quality reviews on all first of kind equipment
24. 7. Perform Supplier Quality management system Audit and manage the Supplier quality improvement plan and ensure corrective/preventive action implementation.
**Public Compensation:**
$215,433/year to $231,110/year + bonus + equity + benefits
**Industry:** Internet
**Equal Opportunity:**
Meta is proud to be an Equal Employment Opportunity and Affirmative Action employer. We do not discriminate based upon race, religion, color, national origin, sex (including pregnancy, childbirth, or related medical conditions), sexual orientation, gender, gender identity, gender expression, transgender status, sexual stereotypes, age, status as a protected veteran, status as an individual with a disability, or other applicable legally protected characteristics. We also consider qualified applicants with criminal histories, consistent with applicable federal, state and local law. Meta participates in the E-Verify program in certain locations, as required by law. Please note that Meta may leverage artificial intelligence and machine learning technologies in connection with applications for employment.
Meta is committed to providing reasonable accommodations for candidates with disabilities in our recruiting process. If you need any assistance or accommodations due to a disability, please let us know at
Program Manager, Manufacturing

Posted 12 days ago
Job Viewed
Job Description
Manufacturing is a pillar within Meta's Delivery Team supporting data center construction. We exist to support the predictable delivery of capacity at scale through manufactured solutions.The Manufacturing Team's primary focus is supply chain engagement and optimization. We accept Manufacturing Informed Designed (MID) components and orchestrate their detailing and prototyping to optimum manufacturability then work with our partners in Delivery to plan logistics and integration to avoid challenges in construction.This team is comprised of strategic designers, strategic builders, tactical specialists, plus internal and external subject matter experts (SME) including preconstruction managers, contractors, schedulers, equipment reliability engineers, and sourcing specialists. This position will lead program management of all manufactured components in support of Meta's RPL project. This mega-project is of such scale that it requires a high-performing PM to drive strategic and tactical aspects of first-of-kind prototyping, logistics, and integration. Never before have we relied so heavily on offsite construction; a necessity here to deliver a project of this magnitude on an aggressive timeline. The successful candidate will be instrumental in ensuring the timely delivery of this capacity on what will be the largest project in Meta's history and one of a few of the largest data centers in the world.
**Required Skills:**
Program Manager, Manufacturing Responsibilities:
1. Program Management - Lead coordination, document, and anticipate program needs to ensure cost, schedule, and quality in concert with the mega-project construction
2. Primary Interface with the Manufacturing CAPs (Component Accountable PMs) - to coordinate on Supplier production (manufacturing execution) including configuring supply chain, production, scheduling, strategic inventory, logistics, and integration in collaboration with our delivery and quality teams
3. Interface with mega-project MOFE (Manufactured Owner Furnished Equipment) Onsite Logistics PM for logistical planning
4. Interface with mega-project MOFE Onsite Integration / Testing PM for planning and coordination
5. Manage GC (General Contractor) MOFE Coordinators for logistics, planning, coordination, reporting, lessons learned, etc.
6. Risk Matrix development, maintenance, and related reporting
7. Cost & Change Coordination with mega-project Meta designees including CM/PCA, ISCE, & MOFE CAPs
8. Schedule Development with Engineering/Scheduling, GCs, CAPs, & Suppliers
9. Regular Debriefs / Lessons Learned development, summary and communication to Engineering, Leadership, & XFNs (cross-functional partners)
10. Partner with cross functional teams on related efforts to ensure alignment and transparency across Design, Engineering, & Construction (DEC)
11. Partner closely with Sourcing Team for strategy and deployment of owner furnished equipment.
12. Partner with Global QA/QC Team to identify and strategically shift to the vendors and manufacturers, appropriate elements of the multi-trade integration and commissioning efforts to reduce onsite efforts. Your objective is to embed as much trade work and commissioning as is appropriate at the optimum points of fabrication from start through to the final point of integration.
13. Support team learning by bring lessons learned, vendors, new technology, and other topics to the group for exploration.
14. Travel approximately 40% Domestic Travel to construction and fabrication sites required (including minimal international travel as required)
**Minimum Qualifications:**
Minimum Qualifications:
15. Bachelor's degree or equivalent work experience in program management
16. 10+ years' experience in construction, manufacturing, and/or project planning
17. Experience in large scale construction management and/or scalable manufacturing
18. Manufacturing-for-construction background with understanding of lean manufacturing and supply-chain management plus knowledge of production machinery, processes, and standards in the field or industry experience with developing workflows and their associated flowcharts, schedules, and action plans
19. Experience building consensus and communicate effectively with a wide range of audiences (stakeholders to executive leadership).
20. Proven track record of adaptability and problem-solving in a dynamic work environment
21. Proficient working knowledge of Google Workspace and Bluebeam
**Preferred Qualifications:**
Preferred Qualifications:
22. Experience with off-site fabrication, pre-assembly and/or modularization of complex elements for construction (or off-shore) projects
23. Mission Critical, infrastructure, and/or data center construction experience
24. Experience working with blended architecture, engineering, manufacturing/assembly and construction teams
25. Software experience with eBuilder, Procore, Solidworks, Autodesk modeling software, Primavera P6, and/or BIM 360
26. Experience with LEAN tools (such as Choosing by Advantage, Last Planner/Pull Planning, Gemba, Kanban)
27. Experience working with Statistical Process Control (SPC), Just In Time (JIT) strategizing, and manufacturing data analytics.
28. PMP Certification
**Public Compensation:**
$144,000/year to $201,000/year + bonus + equity + benefits
**Industry:** Internet
**Equal Opportunity:**
Meta is proud to be an Equal Employment Opportunity and Affirmative Action employer. We do not discriminate based upon race, religion, color, national origin, sex (including pregnancy, childbirth, or related medical conditions), sexual orientation, gender, gender identity, gender expression, transgender status, sexual stereotypes, age, status as a protected veteran, status as an individual with a disability, or other applicable legally protected characteristics. We also consider qualified applicants with criminal histories, consistent with applicable federal, state and local law. Meta participates in the E-Verify program in certain locations, as required by law. Please note that Meta may leverage artificial intelligence and machine learning technologies in connection with applications for employment.
Meta is committed to providing reasonable accommodations for candidates with disabilities in our recruiting process. If you need any assistance or accommodations due to a disability, please let us know at
Manufacturing Quality Engineer

Posted 12 days ago
Job Viewed
Job Description
Meta Platforms, Inc. (Meta), formerly known as Facebook Inc., builds technologies that help people connect, find communities, and grow businesses. When Facebook launched in 2004, it changed the way people connect. Apps and services like Messenger, Instagram, and WhatsApp further empowered billions around the world. Now, Meta is moving beyond 2D screens toward immersive experiences like augmented and virtual reality to help build the next evolution in social technology. To apply, click "Apply to Job" online on this web page.
**Required Skills:**
Manufacturing Quality Engineer Responsibilities:
1. Develop the manufacturing and quality plans for cabling products for Meta's data centers, including copper, single mode fibre, and multimode fibre cabling, patch panels, cable runways, cable enclosures, and connectors.
2. Develop the manufacturing and quality plans for, IDC products such as Gen sets, Hot Aisle, Racks, UPS, PDUs, Busways, Load banks.
3. Evaluate manufacturing processes by applying knowledge of design, fabrication, assembly, tooling, and materials.
4. Participate in design reviews and provide feedback for DFM (design for manufacturability), DFT (design for testability), yield improvements, and quality control, and audit manufacturing sites to assess supplier's capabilities and implement manufacturing and quality best practices.
5. Drive Lean projects to improve manufacturing and data center processes to eliminate waste, reduce cost, and improve yield, and provide technical leadership and expertise within the supply chain teams during the hardware product lifecycle.
6. Ensure product and process quality targets are met by working with engineering to design test methods, establishing standards, and driving continuous improvement with manufacturers and equipment providers.
7. Improve manufacturing efficiency by analyzing and planning workflows, space requirements, and equipment layout, and prepare product and process reports by collecting, analyzing, and summarizing information and trends in manufacturing, field, and RMA data.
8. Knowledge of quality control techniques, including statistical process control (SPC), measurement system analysis (MSA), and failure mode and effects analysis (FMEA).
9. Knowledge of quality control techniques, including statistical process control (SPC), measurement system analysis (MSA), and failure mode and effects analysis (FMEA).
10. Familiarity with product lifecycle management (PLM) systems and enterprise resource planning (ERP) systems.
11. Experience in working with suppliers to ensure compliance to UL listing and EHS regulations.
12. Familiarity with quality management systems, such as ISO 9001 or similar standards.
13. Strong communication and negotiation skills to work with suppliers on resolving quality issues and improving performance.
14. Lead XFN Meta team and Manage supplier team for product delivery.
15. Telecommute from anywhere in the US permitted.
**Minimum Qualifications:**
Minimum Qualifications:
16. Requires a Master's degree in Computer Science, Electrical Engineering, Mechanical Engineering, or related field and 24 months of work experience in job offered or in a quality engineering-related occupation.
17. Requires 24 months of experience in the following:
18. 1. Driving root cause and corrective action for failures during manufacturing and operation
19. 2. Assisting in implementing failure analysis tools and processes
20. 3. Creating and maintaining all product process, quality, and technical training documentation, and BOMs
21. 4. Engineering change notifications, and manufacturing process changes through product lifecycle management tools
22. 5. PCBA assembly and test processes
23. 6. Conduct product quality reviews on all first of kind equipment
24. 7. Perform Supplier Quality management system Audit and manage the Supplier quality improvement plan and ensure corrective/preventive action implementation.
**Public Compensation:**
$215,433/year to $231,110/year + bonus + equity + benefits
**Industry:** Internet
**Equal Opportunity:**
Meta is proud to be an Equal Employment Opportunity and Affirmative Action employer. We do not discriminate based upon race, religion, color, national origin, sex (including pregnancy, childbirth, or related medical conditions), sexual orientation, gender, gender identity, gender expression, transgender status, sexual stereotypes, age, status as a protected veteran, status as an individual with a disability, or other applicable legally protected characteristics. We also consider qualified applicants with criminal histories, consistent with applicable federal, state and local law. Meta participates in the E-Verify program in certain locations, as required by law. Please note that Meta may leverage artificial intelligence and machine learning technologies in connection with applications for employment.
Meta is committed to providing reasonable accommodations for candidates with disabilities in our recruiting process. If you need any assistance or accommodations due to a disability, please let us know at