1,230 Industrial Operations jobs in the United States
INDUSTRIAL OPERATIONS INTERN
Posted 3 days ago
Job Viewed
Job Description
INDUSTRIAL OPERATIONS INTERN Essential Functions/Duties:
Core Skills
- Excellent communication and organizational skills
- Good communication and organizational skills
- Strong computer skills
- Ability to work independently or in a team environment
- Analytical personality
Technical & Industry Knowledge
- Understanding of industrial operations, including common obstacles and effective solutions
- Lean Manufacturing
Workplace Competencies
- Ability to maintain confidentiality
- Ability to work within safety guidelines
- Demonstrated ability to work in a fast-paced environment
- Willingness to work flexible shifts as required
Required Experience/Skills:
- Pursuing a degree in Engineering (Sophmore level)
- Microsoft Office/Excel
- Excellent Attention to Detail
- Reliability
Date: Jul 7, 2025
Location:
Austin-Texas, US
Job Requisition ID: 385022
Other jobs in Manufacturing
INDUSTRIAL OPERATIONS INTERN
Posted 1 day ago
Job Viewed
Job Description
INDUSTRIAL OPERATIONS INTERN Essential Functions/Duties:
Core Skills
- Excellent communication and organizational skills
- Good communication and organizational skills
- Strong computer skills
- Ability to work independently or in a team environment
- Analytical personality
Technical & Industry Knowledge
- Understanding of industrial operations, including common obstacles and effective solutions
- Lean Manufacturing
Workplace Competencies
- Ability to maintain confidentiality
- Ability to work within safety guidelines
- Demonstrated ability to work in a fast-paced environment
- Willingness to work flexible shifts as required
Required Experience/Skills:
- Pursuing a degree in Engineering (Sophmore level)
- Microsoft Office/Excel
- Excellent Attention to Detail
- Reliability
Date: Jul 7, 2025
Location:
Austin-Texas, US
Job Requisition ID: 385022
Other jobs in ManufacturingSenior Process Improvement Engineer, Industrial Operations
Posted 2 days ago
Job Viewed
Job Description
Industrial Operations Technician - 23500

Posted 2 days ago
Job Viewed
Job Description
Required Travel: 0 - 10%
Employment Type: Full Time/Salaried/Exempt
Anticipated Salary Range: $46,095.00 - $70,000.00
Security Clearance: Secret
Level of Experience: Entry Level
This opportunity resides with Warfare Systems (WS), a business group within HII's Mission Technologies division. Warfare Systems comprises cyber and mission IT; electronic warfare; and C5ISR systems.
HII works within our nation's intelligence and cyber operations communities to defend our interests in cyberspace and anticipate emerging threats. Our capabilities in cybersecurity, network architecture, reverse engineering, software and hardware development uniquely enable us to support sensitive missions for the U.S. military and federal agency partners.
Meet HII's Mission Technologies Division
Our team of more than 7,000 professionals worldwide delivers all-domain expertise and advanced technologies in service of mission partners across the globe. Mission Technologies is leading the next evolution of national defense - the data evolution - by accelerating a breadth of national security solutions for government and commercial customers. Our capabilities range from C5ISR, AI and Big Data, cyber operations and synthetic training environments to fleet sustainment, environmental remediation and the largest family of unmanned underwater vehicles in every class. Find the role that's right for you. Apply today. We look forward to meeting you.
To learn more about Mission Technologies, click here for a short video: Description
HII, Mission Technologies has a need for an Industrial Operations Technician who will play a critical role in maintaining and optimizing industrial systems for a wastewater treatment plant located at the Tobyhanna Army Depot.
Essential Job Responsibilities
+ Design, operate, and maintain sophisticated industrial facilities and equipment.
+ Troubleshoot and resolve complex technical challenges in metal plating, pollution control, and wastewater treatment systems.
+ Conduct scientific tests and experiments for mission-related chemical operations.
+ Collaborate with technical experts and contractors to implement facility improvements.
+ Analyze engineering data and make informed decisions to optimize system performance.
+ Work with unique and custom equipment requiring specialized knowledge and adaptability.
Minimum Qualifications
+ 1-3 years experience with Bachelors in related field; or High School Diploma or equivalent and 4 years relevant experience.
+ Experience with industrial facility operations and maintenance.
+ Strong analytical and problem-solving abilities.
+ Proficiency in operating and maintaining specialized industrial equipment.
+ Knowledge of mechanical, electrical, electronic, chemical, and industrial engineering principles.
+ Clearance: An active SECRET security clearance is required.
Physical Requirements
May require working in an industrial or shipboard environment. Normally not required to lift more than 40 pounds higher than three feet above feet/floor level. May encounter extremes of temperature, pollution, humidity, noise, and other environmental factors while collecting data, observing performance of task teams.
The listed salary range for this role is intended as a good faith estimate based on the role's location, expectations, and responsibilities. When extending an offer, HII's Mission Technologies division takes a variety of factors into consideration which include, but are not limited to, the role's function and a candidate's education or training, work experience, and key skills.
Together we are working to ensure a future where everyone can be free and thrive.
All qualified applicants will receive consideration for employment without regard to race, color, religion, gender, gender identity or expression, sexual orientation, national origin, physical or mental disability, age, or veteran status or any other basis protected by federal, state, or local law.
Do You Need Assistance?
If you need a reasonable accommodation for any part of the employment process, please send an e-mail to and let us know the nature of your request and your contact information. Reasonable accommodations are considered on a case-by-case basis. Please note that only those inquiries concerning a request for reasonable accommodation will be responded to from this email address. Additionally, you may also call 1- for assistance. Press #3 for HII Mission Technologies.
Industrial Operations Project Manager 6
Posted 5 days ago
Job Viewed
Job Description
At Northrop Grumman, our employees have incredible opportunities to work on revolutionary systems that impact people's lives around the world today, and for generations to come. Our pioneering and inventive spirit has enabled us to be at the forefront of many technological advancements in our nation's history - from the first flight across the Atlantic Ocean, to stealth bombers, to landing on the moon. We look for people who have bold new ideas, courage and a pioneering spirit to join forces to invent the future, and have fun along the way. Our culture thrives on intellectual curiosity, cognitive diversity and bringing your whole self to work - and we have an insatiable drive to do what others think is impossible. Our employees are not only part of history, they're making history.
Northrop Grumman Defense Systems in Northridge, CA is currently seeking an Industrial Operations Project Manager 6 to support various programs under Advanced Weapons Systems.
Duties And Responsibilities:- Managing and maintaining the daily interfaces and communications between the assigned Program Management Office (PMO), Manufacturing, Test, Manufacturing Resource Planning (MRP), Mission Assurance (MA), and Engineering, from a Digital Transformation perspective.
- Lead a team of cross-functional engineers to stand up various tools but not limited to Sync Manufacturing, Dynamic Production Schedule, data metrics, and SAP ERP.
- Facilitating internal meetings in a way to support design, production, and problem resolutions.
- Develop an operational understanding of the MES platform of choice for the business unit and how it interfaces with the ERP system in terms of data management
- Support NGDS Digital Transformation efforts (HoloLens Augment Reality (AR), assembly process simulation, capacity modeling, and other digital thread efforts).
- Develop an effective understanding of current operations processes across stakeholder departments
- Work across multiple stakeholder departments to facilitate the execution of implementation plans as provided by the business unit's subject matter expert (SME)
- Conduct meetings, trainings, and software demonstrations as required
- Participate in monthly meetings with senior leadership to discuss implementation statuses, challenges, and directions for existing and emergent product lines.
- Manage/generate account requests for the MES platform by interfacing with the Enterprise Systems Group
- Ensure MES user accounts reflect users' roles on the production line
- Train Manufacturing Engineers and production line personnel to use the MES platform per procedures authored by the SME
- Work with the Enterprise Systems Group to document and solve issues encountered with the MES platform
- Work with the business unit's Business Software Analysts and the Enterprise Systems Group to test new features or upgrades to the MES platform
- Author content and provide guidance to Manufacturing Engineers in operation structure, textual, and graphical work instruction formatting in the MES platform to meet implementation milestones and deadlines
- Learn to translate Operations processes and facilitate Test Procedure updates with Engineering and Mission Assurance to enable paperless, automated, digital environments
- Facilitate the acquisition of necessary hardware to ensure product lines can use the MES platform.
- Bachelor's degree in Engineering or Business Management with 14 years of Manufacturing or Engineering experience; Master's degree with 12 years of experience; PhD with 10 years of experience
- Extensive experience with digital transformation efforts and managing cross-function engineers and data scientists within the Defense Industry
- Experience with standing-up the infrastructure for Manufacturing Execution System (MES)
- Experience with cost, schedule, project leadership, and/or process improvement
- Current US Government Secret security clearance adjudicated within the past 5 years
- Experience with bases of estimates, shop order creation, and Earned Value Management Systems (EVMS)
Living in Northridge offers a perfect combination of urban living with the beauty of nature. It is a short drive away from downtown Los Angeles, the Hollywood Hills, or the rest of the San Fernando Valley. Take advantage of your flexible work schedule to enjoy shopping at the local Northridge Fashion Center or spend time at the local Recreation Center as well as easy access to nearby protected natural areas such as the Chatsworth Reservoir, the Santa Susana Pass State Historic Park, Lake Balboa or within driving distance, spend a day at the beach. With Cal State Northridge right in the heart of town, the area has an active college-town energy combined with family-friendly suburban charm. The stunning southern California climate makes for year-round easy living. With an average of 284 sunny days during the year, it is safe to say you'll have plenty of time to enjoy your outdoor activities to the fullest.
The above salary range represents a general guideline; however, Northrop Grumman considers a number of factors when determining base salary offers such as the scope and responsibilities of the position and the candidate's experience, education, skills and current market conditions. Depending on the position, employees may be eligible for overtime, shift differential, and a discretionary bonus in addition to base pay. Annual bonuses are designed to reward individual contributions as well as allow employees to share in company results. Employees in Vice President or Director positions may be eligible for Long Term Incentives. In addition, Northrop Grumman provides a variety of benefits including health insurance coverage, life and disability insurance, savings plan, Company paid holidays and paid time off (PTO) for vacation and/or personal business.
Northrop Grumman is an Equal Opportunity Employer, making decisions without regard to race, color, religion, creed, sex, sexual orientation, gender identity, marital status, national origin, age, veteran status, disability, or any other protected class. U.S. Citizenship is required for all positions with a government clearance and certain other restricted positions.
Industrial Operations Project Manager 6

Posted 5 days ago
Job Viewed
Job Description
CLEARANCE TYPE: Secret
TRAVEL: Yes, 10% of the Time
**Description**
At Northrop Grumman, our employees have incredible opportunities to work on revolutionary systems that impact people's lives around the world today, and for generations to come. Our pioneering and inventive spirit has enabled us to be at the forefront of many technological advancements in our nation's history - from the first flight across the Atlantic Ocean, to stealth bombers, to landing on the moon. We look for people who have bold new ideas, courage and a pioneering spirit to join forces to invent the future, and have fun along the way. Our culture thrives on intellectual curiosity, cognitive diversity and bringing your whole self to work - and we have an insatiable drive to do what others think is impossible. Our employees are not only part of history, they're making history.
Northrop Grumman Defense Systems in **Northridge, CA** is currently seeking a **Industrial Operations Project Manager 6** to support various programs under **Advanced Weapons Systems.**
**Duties and Responsibilities:**
+ Managing and maintaining the daily interfaces and communications between the assigned Program Management Office (PMO), Manufacturing, Test, Manufacturing Resource Planning (MRP), Mission Assurance (MA), and Engineering, from a Digital Transformation perspective.
+ Lead a team of cross-functional engineers to stand up various tools but not limited to Sync Manufacturing, Dynamic Production Schedule, data metrics, and SAP ERP.
+ Facilitating internal meetings in a way to support design, production, and problem resolutions.
+ Develop an operational understanding of the MES platform of choice for the business unit and how it interfaces with the ERP system in terms of data management
+ Support NGDS Digital Transformation efforts (HoloLens Augment Reality (AR), assembly process simulation, capacity modeling, and other digital thread efforts).
+ Develop an effective understanding of current operations processes across stakeholder departments
+ Work across multiple stakeholder departments to facilitate the execution of implementation plans as provided by the business unit's subject matter expert (SME)
+ Conduct meetings, trainings, and software demonstrations as required
+ Participate in monthly meetings with senior leadership to discuss implementation statuses, challenges, and directions for existing and emergent product lines.
+ Manage/generate account requests for the MES platform by interfacing with the Enterprise Systems Group
+ Ensure MES user accounts reflect users' roles on the production line
+ Train Manufacturing Engineers and production line personnel to use the MES platform per procedures authored by the SME
+ Work with the Enterprise Systems Group to document and solve issues encountered with the MES platform
+ Work with the business unit's Business Software Analysts and the Enterprise Systems Group to test new features or upgrades to the MES platform
+ Author content and provide guidance to Manufacturing Engineers in operation structure, textual, and graphical work instruction formatting in the MES platform to meet implementation milestones and deadlines
+ Learn to translate Operations processes and facilitate Test Procedure updates with Engineering and Mission Assurance to enable paperless, automated, digital environments
+ Facilitate the acquisition of necessary hardware to ensure product lines can use the MES platform.
**Basic Qualifications:**
+ Bachelor's degree in Engineering or Business Management with 14 years of Manufacturing or Engineering experience; Master's degree with 12 years of experience; PhD with 10 years of experience
+ Extensive experience with digital transformation efforts and managing cross-function engineers and data scientists within the Defense Industry
+ Experience with standing-up the infrastructure for Manufacturing Execution System (MES)
+ Experience with cost, schedule, project leadership, and/or process improvement
+ Current US Government Secret security clearance adjudicated within the past 5 years
**Preferred Qualifications:**
+ Experience with bases of estimates, shop order creation, and Earned Value Management Systems (EVMS)
Living in Northridge offers a perfect combination of urban living with the beauty of nature. It is a short drive away from downtown Los Angeles, the Hollywood Hills, or the rest of the San Fernando Valley. Take advantage of your flexible work schedule to enjoy shopping at the local Northridge Fashion Center or spend time at the local Recreation Center as well as easy access to nearby protected natural areas such as the Chatsworth Reservoir, the Santa Susana Pass State Historic Park, Lake Balboa or within driving distance, spend a day at the beach. With Cal State Northridge right in the heart of town, the area has an active college-town energy combined with family-friendly suburban charm. The stunning southern California climate makes for year-round easy living. With an average of 284 sunny days during the year, it is safe to say you'll have plenty of time to enjoy your outdoor activities to the fullest.
For more information, please click on this link below:
Northrop Grumman in Northridge-California - Northrop Grumman ( Range: $171,000.00 - $256,400.00
The above salary range represents a general guideline; however, Northrop Grumman considers a number of factors when determining base salary offers such as the scope and responsibilities of the position and the candidate's experience, education, skills and current market conditions.
Depending on the position, employees may be eligible for overtime, shift differential, and a discretionary bonus in addition to base pay. Annual bonuses are designed to reward individual contributions as well as allow employees to share in company results. Employees in Vice President or Director positions may be eligible for Long Term Incentives. In addition, Northrop Grumman provides a variety of benefits including health insurance coverage, life and disability insurance, savings plan, Company paid holidays and paid time off (PTO) for vacation and/or personal business.
The application period for the job is estimated to be 20 days from the job posting date. However, this timeline may be shortened or extended depending on business needs and the availability of qualified candidates.
Northrop Grumman is an Equal Opportunity Employer, making decisions without regard to race, color, religion, creed, sex, sexual orientation, gender identity, marital status, national origin, age, veteran status, disability, or any other protected class. For our complete EEO and pay transparency statement, please visit U.S. Citizenship is required for all positions with a government clearance and certain other restricted positions.
Industrial Engineer (Operations Process Improvement)
Posted today
Job Viewed
Job Description
Join us and discover a work experience where diverse ideas are met with enthusiasm, and where you can learn and grow to your full potential. We're looking for individuals who thrive in an entrepreneurial environment and who enjoy working as a team to deliver unparalleled service and solutions to our customers.
The salary range posted represents the low and high end of OSI's salary range for this position. Salaries will vary based on various factors, including but not limited to, location, education, skills, experience and performance. Base salary is one component of OSI's overall total rewards package. Other components may include bonuses, special pay programs, comprehensive time off, 401k with match and a full suite of benefit offerings for you and your family.
This role is responsible for designing, developing, testing, and evaluating integrated systems for managing industrial production processes including human work factors, quality control, cost systems integration, inventory control, logistics, process flow, material flow, cost analysis, and production coordination. Increase production efficiency and process yield through people management, technology, and business organization.
Job Responsibilities
- Job is an individual contributor and has no direct reports.
- Develop control systems that help in the analysis of costs and planning of finances for investments.
- Upgrade processing systems and determine how best to use the workforce to achieve optimum cost advantages.
- Learn product requirements and ensure that they are met.
- Solve production problems that arise within the organization and facilities.
- Design information as well as manufacturing systems to integrate cost and processing design.
- Review and develop optimum cost-efficient processes.
- Monitor general flow of operations.
- Establish programs of work measurement to guarantee fulfillment of targets and deadlines.
- Determine how best to utilize the workforce to achieve maximum productivity.
- Coordinate quality objectives with manufacturing solutions to maximize product reliability and minimize cost.
- Confer with vendors, staff, and management personnel regarding processing equipment purchases, product specifications, manufacturing capabilities, and project status.
- Draft and design layout of equipment, materials, and workspace to illustrate maximum efficiency using drafting tools and computer aids.
- Estimate product costs and effect of product design changes for management review, action, and control.
- Formulate sampling procedures and designs to measure key performance indicators (KPI's), reporting yields, efficiencies, quality, and reliability data.
- Analyze statistical data and product specifications to determine standards and establish cost objectives.
- Develop manufacturing methods, labor utilization standards, and cost analysis systems to promote efficient staff and facility utilization.
- This role has the responsibility to understand and place in practice appropriate safety procedures. This responsibility is achieved through education, training, use of protective equipment (as applicable) and by following safety policies, regulations, standards, and laws.
- Perform other duties as assigned.
Experience & Skills
- 3-5 years of experience in related field is preferred.
- Excellent proficiency in all Microsoft Office Suite Products.
- Experience in the food industry is a plus.
- Production and processing knowledge of raw materials, production processes, quality control, costs, systems (SAP), and techniques to maximize the effective manufacture and distribution of goods.
- Knowledge of mathematics, statistics, and their applications.
- Knowledge of business and management principles involved in strategic planning, resource allocation, modeling production methods, and coordination of people and resources.
- Working skills on computer and basic application programming.
- Excellent communication skills both written and oral with the ability to communicate effectively across vertical and horizontal lines.
- Demonstrated analytical, problem-solving, and decision-making skills with the ability to drive results.
- Ability to operate on tight deadlines with multiple priorities that are subject to frequent changes.
- Advanced Excel and the MS suite of products is required.
- Knowledge of design techniques for processes, technical plans, blueprints, drawings, and models.
- Administrative and accounting skills.
Education
- BA/BS or equivalent is preferred.
- Industrial Engineering and/or Operations Management would be a plus.
- We do NOT sponsor.
Work Environment
- Work can be performed within a manufacturing plant environment with noise, extreme temperatures, and significant movement of powered equipment, people and conveyor (may depend on the role).
- Work conditions are typical of a food manufacturing facility.
- This role requires 30% domestic travel.
- Position may require the physical agility of lifting up to 50 pounds.
- Position may require frequent and/or infrequent of bending, squatting, pushing, pulling, stretching/reaching, use hands or fingers, talk, hear, feel objects, tools, controls and standing/walking on concrete flooring.
- Position may require the physical ability to stand/walk for Greater than 4 hours.
Be The First To Know
About the latest Industrial operations Jobs in United States !
Industrial Engineer & Operations Analyst
Posted 12 days ago
Job Viewed
Job Description
If you want to learn about the intersection of technology, innovation, and good old-fashioned teamwork, we might be a good fit for you. Wherever you start in the company, our hope is that it is a launching point to higher achievement. At ThriftBooks, your success is up to you.
We are growing & looking for an Industrial Engineer to join our Innovations Team. This person will focus on processing center design, process engineering, and automation solutions that support and improve our nationwide ecommerce operations. This individual will lead the design and implementation of systems and processes across our warehouse network, with a strong emphasis on industrial automation and material handling systems. They will also work closely with our software development group to implement tools that enable scalable operations, reduce inefficiencies, and improve reporting and performance monitoring.
What You'll Do
- Optimize processing center workflows, and automation systems.
- Develop cost benefit analyses and financial models to support the processing center's requirements, designs, and alternative selections to existing systems.
- Act as the primary contact for the software development (Operations Engineering) to design, test, schedule, and implement projects within the processing centers.
- Support indirect procurement activities related to capital improvement projects, including vendor selection, RFP preparation, and contract evaluation.
- Develop and maintain labor standards and the productivity monitoring system for the processing center as needed.
- Manage capital improvement projects, including the development and execution of plans to support additional product lines or increased store volume and the development of estimates for the equipment, systems, and personnel needed to complete various projects.
- Assist with the preparation of job performance instructions.
- Research ergonomic and safety issues in the facility; make improvements as needed.
- Provide technical support to the Maintenance, Operations, and Information Services groups located in the processing center.
- Degree in Industrial Engineering, Manufacturing Engineering, or similar field.
- Experience with financial analysis, financial modeling, profitability analysis and/or auditing techniques.
- Experience with analyzing and reporting data to identify issues, trends, or exceptions to drive improvement of results and find solutions.
- SQL and Advanced Excel skills (pivot tables, lookups, modeling).
- Familiarity with Agile project management and collaborative software development cycles.
- Experience using time management skills such as prioritizing/organizing and tracking details and meeting aggressive deadlines of multiple projects with varying completion dates.
- Proficiency in Microsoft Word, Outlook, and PowerPoint.
- Strong communication, documentation, and cross-functional collaboration skills.
- Self-motivated to learn new concepts and participate in new projects.
Location: This position is hybrid, working in our Processing Centers & remote. You must reside in a one of these states where a processing center is located (AZ, TX, IL, or GA).
Why You'll Love It Here
- Competitive compensation package
- Earn Paid Time Off at Accrual Rate of 15-days per year
- 6 Paid Holidays per calendar year
- Medical & Vision Insurance
- Dental Insurance
- Company paid STD/LTD
- Company paid Life Insurance
- Annual bonus incentive
- 401k match program
- Professional development & growth opportunities
- Work with nice, fun people
- FREE BOOKS!
All candidates must be willing to authorize a pre-employment background check. All applicants agree to the ThriftBooks Privacy Notice for Employment-Related Personal Data: #COR80
If you are ready for your next big challenge, we would love to hear from you!
Flexible work from home options available.
Director of Industrial Maintenance Operations
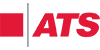
Posted 5 days ago
Job Viewed
Job Description
Fundada en 1985, ATS es una empresa con presencia en los Estados Unidos, México y el Reino Unido. Somos profesionales en mantenimiento industrial y hacemos que las fábricas funcionen mejor.
**Principal Duties/Responsibilities** **:**
**_To_** **_Live and Lead Safety_**
+ Drives a culture of safety and wellness through personal example and through actively engaging sites in the achievement of safety objectives.
+ Fosters preventive measures, encourages education, and completes auditing activity to create an environment for zero incidents.
+ Leads and deploys ATS's safety initiatives and employee health and wellness in support of our Beyond Zero initiatives.
+ Engages and leads all safety investigations for incidents involving CLSRs/LOTO and accidents.
**_To_** **_Inspire and Provide Clarity on Vision and Strategy_**
+ Is accountable for his/her actions andbehaviors, driving accountability to priorities and goals through clear communication of what needs to be done and why.
+ Demonstrates a thorough understanding of the vision,executing both long-term and short-term strategies, enabling direct reports to understand the value of site-level initiatives to the achievement of company-wide objectives.
+ Acts as a champion for positive change, and coaches direct reports in the effective communication and implementation of new/revised processes and procedures.
**_To_** **_Own Our ATS Culture_**
+ Provides leadership in formulating and administering company policies and best practices, including role modeling as well as teaching and setting expectations for ATS Culture behaviors.
+ Observes team interactions to monitor engagement and identify potential concerns. Investigates for root cause issues when there are engagement gaps. Actively supports engagement surveys, working with the Site Manager to develop corrective action plans and to ensure completion of identified actions.
+ Models the key competencies for ATS leaders, promoting the competency model and coaching others in the consistent demonstration of leadership behaviors.
+ Builds a culture of engaged, high performing employees by setting clear expectations, providing opportunities for growth and development, and giving ongoing performance feedback.
_T_ **_o Support Our Employees' Learning and Growth_**
+ Ensures that site technician skills assessments, training and development plans are in place and are actively used for development, promotion, and performance management purposes.
+ Recognizes employees' contributions to the organization and encourages best practice sharing across the organization.
+ Collaborates with HR Business Partners to resolve people-related issues and to share business updates as well asfuture actions/opportunities to ensure proactive people support plans are in place.
**_To_** **_Ensure and Drive our Business Results_**
+ Ensures that the Operating System is fully understood, frequently reinforced, and embedded across all locations.
+ Ensures that all sites develop and execute a site-specific maintenance plan per ATS standards.
+ Monitors service level KPIs, Balanced Scorecard and customer dashboards.
+ Delivers quarter by quarter financial resultsacross the portfolio of business within the area of responsibility.
+ Accountable for improving efficiency and effectiveness of workforce through the management of labor hours, labor utilization, backlog hours, PM optimization, and the implementation of tools and processes designed to improve labor productivity across their portfolio of business.
+ Hires new employees with an eye to future potential; identifies current strong performers with growth potential; and executes succession planning to ensure bench strength for critical positions.
+ Builds strong relationships with site and division customers in the context ofcustomer expectations and ATS commitments. Promotes customer loyalty via customer surveys,effective communication, and responsive actions.
+ Supports the Site Manager where contract changes or interpretation is required.
+ Ensures customer satisfaction by understanding the unique needs of each customer, facilitating solution development, following up on progress, and assisting managers with taking corrective actions as needed.
+ Reviews operational metrics with customers to measure, illustrate, and communicate ATS's value.
+ Executesorganizational support and growth strategies for area.
+ Collaborates withthe team and with existing customers to expand ATS's business, including opportunities for cost savings, quality improvements, and new ways to leverage the ATS relationship.
+ Engages the sales team on new business opportunities throughcollaborating on assessments, developing new contract solutions, and creating models to support the scope of the potential new contract.
**Knowledge, Skills, Abilities (KSAs), & Competencies** **:**
**Essential** **KSAs** **:**
+ Bachelor's degree in business, engineering, operations management, or a related field and eight years of experience with business / operational management in a related industry or an equivalent combination of education and experience.
+ Strong understanding of manufacturing work environment.
+ Demonstrated leadership ability.
+ High emotional intelligence quotient with ability to effectively interact with multiple stakeholders, i.e., technicians, site leadership, ATS senior leadership, and customers.
+ Solid financial acumen and experience managing P&Ls and financial forecasting.
+ Experience leading change management in an organization.
+ Demonstrated capability to think strategically and to articulate strategic plans.
+ Extensive travel required.
**Desirable** **KSAs** **:**
+ Maintenance management experiencepreferred.
+ Experience leading managers across multiple locationspreferred.
+ Proven experience with operational excellence & continuous improvement methodologies.
+ Experience with new customer integrations or startup activities.
**Leadership** **Core** **Competencies** **:**
**_Business and Company Acumen_**
Lead with honesty and integrity
Build bold and relevant strategies
Welcome and motivate change
Recognize the right outcomes and how they were achieved
Role model safety and wellness
**_Emotional Intelligence_**
Provide psychological safety
Be self-aware
Build relationships
Ask for and act on feedback
Respect diverse background and viewpoints
**_Lead in the Present; Eye to the Future_**
Commit to accountability
Coach people to their potential
Own talent development and placement
Turn problems into opportunities
Be resilient and flexible
**_Communicate, Communicate, Communicate_**
Practice transparency
Build relationships through respect
Be a curious learner and credible teacher
Influence in a proactive, positive way
Ensure cross functional awareness/decisions
**Physical Demands and Working Conditions:** While performing the duties of this job, the employee is regularly required to stand; walk; use hands/fingers to handle, or feel; reach with hands and arms; climb, ascend/descend or balance to heights that may require a ladder or lift; stoop, kneel, crouch, or crawl in confined spaces; and talk or hear? The employee is occasionally required to sit? The employee must occasionally lift and/or move more than 50 pounds? The employee is regularly required to use close vision and color vision? The employee is occasionally exposed to outside weather conditions and risk of electrical shock? Work is typically performed in a factory environment and is usually very loud. In the factory environment, the employee may be exposed to hazardous materials and/or greasy or slippery factory floors.
ATS believes in fair and equitable pay. Please note that actual salaries may vary within the range, or be above or below the range, based on factors including, but not limited to, education, training, experience, professional achievement, business need, and location.
Pay Range
$140,552.59-$187,403.47 USD
ATS is committed to providing equal employment opportunities in all aspects of employment to all applicants and employees without regard to age, color, race, religion, national origin, disability, veteran status, genetic information, or other legally protected status. Review the privacy policy here. ( se compromete a brindar igualdad de oportunidades de empleo en todos los aspectos del empleo a todos los solicitantes y empleados, independientemente de su edad, color, raza, religión, sexo (incluido el embarazo, identidad de género y orientación sexual), origen nacional, discapacidad, estatus de veterano, información genética u otro estatus legalmente protegido. Revisión de la política de privacidad aquí here. ( is committed to providing equal employment opportunity in all aspects of employment to all applicants and employees, regardless of age, color, race, religion, sex (including pregnancy, gender identity, and sexual orientation), national origin, disability, veteran status, genetic information or other legally protected status.
Principal Industrial Engineer - Operations Optimization
Posted 2 days ago
Job Viewed
Job Description
- Leading the design and implementation of process improvements, lean manufacturing initiatives, and operational excellence programs.
- Conducting in-depth analysis of existing workflows, supply chains, and production processes to identify areas for optimization.
- Developing and utilizing advanced modeling and simulation techniques to evaluate proposed changes and predict outcomes.
- Implementing Lean Six Sigma methodologies to reduce waste, improve quality, and increase throughput.
- Designing and optimizing facility layouts, material flow, and workstation ergonomics.
- Developing and maintaining key performance indicators (KPIs) to measure operational performance and drive continuous improvement.
- Collaborating with cross-functional teams, including operations, engineering, quality, and IT, to ensure successful implementation of solutions.
- Developing business cases and justifying investments in new technologies and process improvements.
- Mentoring and guiding junior industrial engineers and providing technical expertise.
- Staying current with industry best practices and emerging technologies in operations management and industrial engineering.