445 Industrial Plants jobs in the United States
Process Engineering
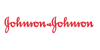
Posted 5 days ago
Job Viewed
Job Description
Supply Chain Engineering
**Job Sub** **Function:**
Process Engineering
**Job Category:**
Scientific/Technology
**All Job Posting Locations:**
Jacksonville, Florida, United States of America
**Job Description:**
Johnson & Johnson is currently seeking a Process Engineer to join Vision (JJV) MedTech located in Jacksonville, Florida.
At Johnson & Johnson, we believe health is everything. Our strength in healthcare innovation empowers us to build a world where complex diseases are prevented, treated, and cured, where treatments are smarter and less invasive, and solutions are personal. Through our expertise in Innovative Medicine and MedTech, we are uniquely positioned to innovate across the full spectrum of healthcare solutions today to deliver the breakthroughs of tomorrow, and profoundly impact health for humanity. Learn more at are seeking an engineer to join our Process Engineering team. The ideal candidate will possess a basic understanding of material properties, process efficiencies, automated high speed manufacturing equipment, and measurement system analysis, with some experience in supporting improvement initiatives in GxP environments.
**Key Role Responsibilities**
+ Identifies key opportunities to develop and implement equipment and/or process enhancements that will improve efficiency, product yield, and safety.
+ Identify, plan, and implement projects related to product and process improvement, ensuring alignment with strategic goals.
+ Design and implement experimental protocols applying statistical tools to enhance manufacturing processes and product performance.
+ Analyze current processes to identify key opportunities for equipment and process enhancements that improve efficiency, yield, and safety.
+ Develop detailed documentation for process validation, project management, business case proposals, and root cause problem solving while ensuring compliance with industry regulations and internal standards.
+ Monitor and analyze production data to identify trends and provide actionable insights for continuous improvement.
+ Lead Six Sigma initiatives to drive process optimization and problem resolution within production environments.
**Qualifications**
+ Bachelor's degree in Engineering or Material Science with 2+ years of relevant experience OR a Master's degree in Engineering with 1+ year of experience.
+ Project management experience in an engineering environment.
+ Strong analytical problem-solving skills with experience in data analysis and visualization.
+ Excellent written and oral communication skills; ability to present complex information clearly and concisely.
+ Strong organizational skills
+ Prior experience using Minitab, JMP, or other analytical tools for statistical analysis and effective data visualization.
+ Demonstrated ability to work collaboratively within multi-functional teams and influence partners at all levels.
**Preferred experience:**
+ 2+ years experience in an engineering function in FDA environment preferred
+ Preferred: Six Sigma certification or extensive experience applying Six Sigma methodologies for analytical problem solving
**Other**
+ This position may require up to 10% of travel
We will ensure that individuals with disabilities are provided reasonable accommodation to participate in the job application or interview process, to perform crucial job functions, and to receive other benefits and privileges of employment. Please contact us to request accommodation.
Johnson & Johnson is an Affirmative Action and Equal Opportunity Employer. All qualified applicants will receive consideration for employment without regard to race, color, religion, sex, sexual orientation, gender identity, age, national origin, or protected veteran status and will not be discriminated against on the basis of disability
Process Engineering
Posted 6 days ago
Job Viewed
Job Description
At Johnson & Johnson, we believe health is everything. Our strength in healthcare innovation empowers us to build a world where complex diseases are prevented, treated, and cured, where treatments are smarter and less invasive, and solutions are personal. Through our expertise in Innovative Medicine and MedTech, we are uniquely positioned to innovate across the full spectrum of healthcare solutions today to deliver the breakthroughs of tomorrow, and profoundly impact health for humanity. Learn more at no-style="text-align:left;">Job Function:
Supply Chain EngineeringJob Sub Function:
Process EngineeringJob Category:
Scientific/TechnologyAll Job Posting Locations:
Jacksonville, Florida, United States of AmericaJob Description:
Johnson & Johnson is currently seeking a Process Engineer to join Vision (JJV) MedTech located in Jacksonville, Florida.
At Johnson & Johnson, we believe health is everything. Our strength in healthcare innovation empowers us to build a world where complex diseases are prevented, treated, and cured, where treatments are smarter and less invasive, and solutions are personal. Through our expertise in Innovative Medicine and MedTech, we are uniquely positioned to innovate across the full spectrum of healthcare solutions today to deliver the breakthroughs of tomorrow, and profoundly impact health for humanity. Learn more at are seeking an engineer to join our Process Engineering team. The ideal candidate will possess a basic understanding of material properties, process efficiencies, automated high speed manufacturing equipment, and measurement system analysis, with some experience in supporting improvement initiatives in GxP environments.
Key Role Responsibilities
- Identifies key opportunities to develop and implement equipment and/or process enhancements that will improve efficiency, product yield, and safety.
- Identify, plan, and implement projects related to product and process improvement, ensuring alignment with strategic goals.
- Design and implement experimental protocols applying statistical tools to enhance manufacturing processes and product performance.
- Analyze current processes to identify key opportunities for equipment and process enhancements that improve efficiency, yield, and safety.
- Develop detailed documentation for process validation, project management, business case proposals, and root cause problem solving while ensuring compliance with industry regulations and internal standards.
- Monitor and analyze production data to identify trends and provide actionable insights for continuous improvement.
- Lead Six Sigma initiatives to drive process optimization and problem resolution within production environments.
Qualifications
- Bachelor’s degree in Engineering or Material Science with 2+ years of relevant experience OR a Master’s degree in Engineering with 1+ year of experience.
- Project management experience in an engineering environment.
- Strong analytical problem-solving skills with experience in data analysis and visualization.
- Excellent written and oral communication skills; ability to present complex information clearly and concisely.
- Strong organizational skills
- Prior experience using Minitab, JMP, or other analytical tools for statistical analysis and effective data visualization.
- Demonstrated ability to work collaboratively within multi-functional teams and influence partners at all levels.
Preferred experience:
- 2+ years experience in an engineering function in FDA environment preferred
- Preferred: Six Sigma certification or extensive experience applying Six Sigma methodologies for analytical problem solving
Other
- This position may require up to 10% of travel
We will ensure that individuals with disabilities are provided reasonable accommodation to participate in the job application or interview process, to perform crucial job functions, and to receive other benefits and privileges of employment. Please contact us to request accommodation.
Johnson & Johnson is an Affirmative Action and Equal Opportunity Employer. All qualified applicants will receive consideration for employment without regard to race, color, religion, sex, sexual orientation, gender identity, age, national origin, or protected veteran status and will not be discriminated against on the basis of disability
Industrial Engineering Leader (plant and process engineering)

Posted 2 days ago
Job Viewed
Job Description
At Entrust, we're shaping the future of identity centric security solutions. From our comprehensive portfolio of solutions to our flexible, global workplace, we empower careers, foster collaboration, and build solutions that help keep the world moving safely?
**Get to Know Us?**
Headquartered in Minnesota, Entrust is an industry leader in identity-centric security solutions, serving over 150 countries with cutting-edge, scalable technologies. But our secret weapon? Our people. It's the curiosity, dedication, and innovation that drive our success and help us anticipate the future?
Industrial Engineering Leader (plant and process engineering)
Industrial Engineering Leader is responsible for leading and overseeing the data analytics service offering. Initially, this role will support the global sales team in selling analytics solutions to Entrust's Central Issuance and Bureau customers while delivering analysis, findings, and recommendations based on customer-specific data. As the solution and customer base expand, the specialist will assess global business needs and contribute to the strategic growth of Business Solution Consulting resources.
This role involves implementing and utilizing data collection tools to provide customers with valuable insights into their system efficiency, operational effectiveness, and opportunities for improvement. Additionally, the specialist will contribute to Entrust's Professional Services business opportunities in the Americas, as the consulting solution evolves including projects delivery and solution integration services.
Are you ready to take on a dynamic, high-impact role that will take you across the globe? As an Industrial Engineering Leader you will balance working from home and travelling internationally, engage with diverse customers, and help transform factories and manufacturing facilities using cutting-edge data analytics. This is not a routine desk job-every day brings new challenges, from uncovering inefficiencies in industrial operations to designing innovative solutions that revolutionize how businesses operate.
In this role, you will be at the forefront of expanding a business consulting practice, helping to grow a global customer base for an advanced in-house analytics tool. You'll gain deep insights into creative problem-solving approaches across a unique industry, while collaborating with clients to enhance efficiency and optimize performance.
This role is ideal for a data-driven consultant with strong business acumen, the ability to translate analytics into actionable business strategies, and a passion for improving operational efficiency for clients worldwide. Think "Industrial/Business Engineer" meets "Data Scientist".
Your work will not only drive real-world improvements but will also earn recognition on a larger stage. You'll have opportunities to present your insights and findings at industry conferences, industry events, and executive meetings, showcasing your expertise to influential audiences. If you're passionate about analytics, technology, and making a tangible impact on industrial operations, this role is for you.
**Responsibilities:**
**Customer-Facing Value Consulting (70%)**
+ Prepare and present customer-specific reports using the Entrust Analytics platform, providing insights into root causes of inefficiencies and areas for improvement.
+ Develop customer-specific strategies to improve quality, efficiency, and resource utilization.
+ Maintain a portfolio of case studies covering diverse customer-use scenarios.
+ Develop and refine methodologies, templates, and business process improvement tools, including Lean methodologies.
+ Gain and maintain expertise in issuance market trends and customer drivers to ensure recommendations align with business needs.
+ Conduct on-site assessments, interviews, and audits to develop detailed consulting reports.
+ Prepare and develop consulting reports with data visualizations, graphs, charts, and action plans.
+ Provide valuable insights to professional services teams for improving service efficiency and reducing costs.
**Sales Support (15%)**
+ Deliver customer-specific presentations to support sales engagements domestically and globally.
+ Support sales teams in assessing customer needs, articulating Entrust's value proposition, and delivering consulting expertise.
+ Provide global sales training on tools, methodologies, key messages, and best practices.
+ Maintain a bi-weekly forecasted pipeline of clients and strategize to expand the customer base.
+ Utilize feedback from sales interactions and client engagements to refine the sales strategy and improve onboarding experiences.
**Cross-Functional Coordination**
+ Collaborate with software engineers, developers, integrators, product owners, sales, and technical consultants to develop and implement solutions.
+ Provide insights to Professional Services teams for integration and project support.
+ Assist service teams in improving customer support operations using data insights.
+ Guide the development and roadmap of the analytics tool by influencing engineering and product teams.
**Market & Competitive Intelligence (15%)**
+ Conduct external and internal research on industry trends, market drivers, and competitive landscape.
+ Analyze big data to identify patterns, trends, and opportunities for customers.
+ Collaborate with regional sales and technical sales teams to identify new opportunities and develop regional strategies.
+ Lead meetings with international teams to track business development opportunities and consult on sales strategies.
+ Contribute to the analytics tool roadmap by collaborating with engineering and product teams.
Assets:
+ Experience in a sales support role, including customer presentations and engagement with senior management.
+ Must have legal authorization to work in the US without restrictions.
+ Experience managing multiple parallel-running complex-projects across different time zones.
+ Proficiency in advanced Excel, databases, and data querying tools.
+ Experience with statistics and big data analytics, translating data into meaningful information and actions.
+ Solution pre-sales or sales experience in business value consulting for Financial Central Issuance or Financial Instant Issuance solutions.
+ Experience in secure printing or packaging plants
+ Multilingual abilities are an asset.
+ Experience in attending client factory sites to conduct on-site analysis and audits.
+ Strong problem-solving and critical-thinking skills with a customer-focused attitude.
+ Creative and innovative mindset to develop solutions beyond conventional approaches.
+ Technical ability to troubleshoot software, query databases, write basic computer code, and edit software source code.
+ Capability to modify vast arrays of data using macros or software such as R Studio or Power BI or equivalent
+ Computer science skills in programming and networking are an asset.
+ Strong customer-focused mindset with a track record of building and maintaining relationships.
+ Innovative and creative thinker with an ability to develop out-of-the-box solutions.
**Basic Qualifications**
+ Bachelor's degree with a quantitative focus (e.g., Finance, Economics, Data/Information Systems, Statistics, Applied Sciences, Computer Science/Engineering, Industrial Engineering, or Mathematics).
+ 8+ years of professional experience within the **printing and packaging industry** , or closely similar manufacturing setting.
+ Proven ability to manage complex, multidisciplinary projects across different time zones.
+ Ability to travel internationally (minimum 35%).
+ Advanced background in querying databases and utilizing analytic tools for information intelligence analysis and data visualization + presentation.
**Preferred Qualifications:**
+ 4+ years of Project Management experience or equivalent certification (PMP).
+ Strong background in statistical analysis and translating big data insights into actionable recommendations.
+ Ability to automate and write scripts to create business reports, valuable graphical visualization of data, build automatic forms for customer information input, and automatically generate consulting reports using templates. Also, building data models and business cases.
+ Evident experience presenting in various settings; pre-sales, business case meeting, project delivery, project follow ups, customer complaints, customer experience follow ups, etc.
+ Lean Six Sigma certification or equivalent experience in a technology manufacturing setting.
**Skills & Competencies:**
+ Advanced Excel skills and familiarity with analytics querying tools.
+ Strong project management skills, including creating project roadmaps and tracking implementation.
+ Ability to collaborate effectively with software engineers, developers, product owners, and sales teams.
+ Strong communication skills to foster relationships with clients and internal stakeholders.
+ Ability to sell consulting ideas and help customers implement data-driven solution strategies.
+ Proven ability to analyze customer challenges and provide structured solutions through consulting reports.
+ Open-mindedness, patience, active listening, and strong relationship-building skills.
+ Ability to work in varied conditions across different international markets and customer sites.
At Entrust, we don't just offer jobs - we offer career journeys. Here is what you can expect when you join our team:?
+ Career Growth: Whether you're a budding developer or a seasoned expert, we're invested in your professional journey. With learning-forward initiatives and exciting challenges, your growth is our priority?
+ Flexibility: Life is all about balance. Whether you're remote, hybrid, or on-site, we offer flexible options that fit your lifestyle?
+ Collaboration: Here, your voice matters. Our teams thrive on sharing ideas, brainstorming solutions, and working together to build a better tomorrow?
We believe in securing identities-but it doesn't stop there. At Entrust, we're passionate about valuing all identities. Our culture is built on diversity, inclusion, and respect. From unconscious bias training for our leaders to global affinity groups that connect colleagues across the globe, we're creating a community where everyone is encouraged to be themselves?
**Ready to Make an Impact?**
If you're excited by the prospect of innovating, growing your career, and collaborating in a dynamic environment, Entrust is the place for you. Join us in making a difference. Let's build a more secure world-together?
**Apply today?**
For more information, visit ( ? Follow us on, LinkedIn ( , Facebook ( , Instagram ( , and YouTube ( Range:
The anticipated starting base pay for this position is: $112,847-$165,508 per year (in the primary posting location). Actual compensation will be determined based on geographic location, education, skills and experience. This position is also eligible for the company's discretionary annual incentive plan. In addition to your pay, Entrust offers eligible colleagues and their dependents comprehensive health and well-being programs which include medical, vision, dental, a generous 401(k) matching contribution, life and disability insurance, mental health coaching, virtual fitness programs, paid personal time off plus 12 paid holidays, parental leave and education reimbursement. Please speak with the recruiter for more details. Note: Benefit and Compensation programs are subject to eligibility requirements and other terms of the applicable plan or program. Entrust has the right to end, suspend or amend any of its plans at any time in whole or in part.
_For US roles, or where applicable:_
**Entrust is an** **EEO/AA/Disabled/Veterans** **Employer**
_For Canadian roles, or where applicable:_
**Entrust values diversity and inclusion and we are committed to building a diverse workforce with wide perspectives and innovative ideas. We welcome applications from qualified individuals of all backgrounds, and we strive to provide an accessible experience for candidates of all abilities.**
_If you require an accommodation, contact_ _._
**Recruiter:**
Steve Donahue
Entrust is an innovative leader in identity-centric security solutions, providing an integrated platform of scalable, AI-enabled security offerings. We enable organizations to safeguard their operations, evolve without compromise, and protect their interactions in an interconnected world - so they can transform their businesses with confidence. Entrust supports customers in 150+ countries and works with a global partner network, we are trusted by the world most trusted organizations.
Process Engineering Specialist
Posted 3 days ago
Job Viewed
Job Description
In this position.
Lead problem solving to assist plants and implementation teams in resolving tooling, equipment and conveyor performance issues and downtime
What you'll do.
- Support Manufacturing Process Engineering activity for Final Assembly
- Drive continuous improvement in safety, quality and productivity
- Apply engineering principles and analytical techniques to establish and continuously improve manufacturing processes and products
- Develop action plans as required to investigate and prioritize quality concerns and verify corrective actions on internal processes and supplier processes
- Lead and conduct process audits to ensure process discipline is consistent with Vehicle Operations guidelines
- Conduct job ergonomic evaluations and deliver corrective actions as required
- Analyze vehicle inventory root causes; engage in mapping and corrective actions to reduce vehicle inventory
- Create process and instruction sheets supporting quality methods and processes
- Deliver capable processes and tools for Trim and Chassis Assembly operations
- Lead role in resolving assembly related concerns. Lead variability reduction and lean manufacturing initiatives and best practices
- Ensure compliance to Plant, Corporate, Governmental and Environmental standards
- Support ISO 14001 compliance and support internal ISO auditing and compliance as required
- Support continuous improvement in safety, quality and productivity in Chassis and/or Trim areas
- Identify throughput constraints and drive root cause improvements
- Education: High School Diploma
- Experience: 5+ yrs of related experience
- Successful candidate must be able to demonstrate leadership in ONE FORD (leadership) behaviors combined with outstanding interpersonal, teambuilding, and communication skills
- Education: Bachelor's degree in engineering
- Experience:
- Effective oral and written communication skills
- Lean Manufacturing and Six Sigma experience
- 8D and 5Why corrective action and problem-solving skills
- Lean Tools - 5S, Kanban, Poka-yoke, and Value Stream Mapping
- DMAIC and DMADV (DFSS) Project Methodology experience
- TQM and Kaizen Methods
- FMEA, PPAP, and DOEs experience
- Visual Factory Management
- Ergonomic analysis knowledge and experience
You may not check every box, or your experience may look a little different from what we've outlined, but if you think you can bring value to Ford Motor Company, we encourage you to apply!
As an established global company, we offer the benefit of choice. You can choose what your Ford future will look like: will your story span the globe, or keep you close to home? Will your career be a deep dive into what you love, or a series of new teams and new skills? Will you be a leader, a changemaker, a technical expert, a culture builder.or all of the above? No matter what you choose, we offer a work life that works for you, including:
• Immediate medical, dental, and prescription drug coverage
• Flexible family care, parental leave, new parent ramp-up programs, subsidized back-up child care and more
• Vehicle discount program for employees and family members, and management leases
• Tuition assistance
• Established and active employee resource groups
• Paid time off for individual and team community service
• A generous schedule of paid holidays, including the week between Christmas and New Year's Day
• Paid time off and the option to purchase additional vacation time.
We have a commitment to our products and customers, but also know that our employees are the driving force behind our success. Find out what it is like to love your job. Come discover a Company that is focused on designing better cars, but also cares about you, your family and your community. By choice, we are an Equal Opportunity Employer committed to a culturally diverse workforce.
For a detailed look at our benefits, click here:
This position is a range of salary grades 6 and 7.
Visa sponsorship is not available for this position.
Candidates for positions with Ford Motor Company must be legally authorized to work in the United States. Verification of employment eligibility will be required at the time of hire.
We are an Equal Opportunity Employer committed to a culturally diverse workforce. All qualified applicants will receive consideration for employment without regard to race, religion, color, age, sex, national origin, sexual orientation, gender identity, disability status or protected veteran status. In the United States, If you need a reasonable accommodation for the online application process due to a disability, please call 1- .
#LI-Onsite
#LI-JL1
Responsibilities
NA
Qualifications
NA
Process Engineering Technician
Posted 5 days ago
Job Viewed
Job Description
ResponsibilitiesSupport manufacturing in all aspects of photolithography, including resist coating, and developing processes.Ensure all processes adhere to existing specifications.Work with a team of equipment engineers and operators to solve process problems as they occur.Run designed experiments to improve existing processes or create new processes.Use metrology equipment to monitor processes.Design reticle data layouts and mask designs using CAD software.Essential SkillsAt least a two-year technical degree.Minimum of 2 years of experience in a related field.Experience in CAD design.Experience in process engineering, ideally in development.Additional Skills & QualificationsExperience with photolithography processes.Familiarity with semiconductor manufacturing.Process development and improvement.Pay and BenefitsThe pay range for this position is $55000.00 - $101000.00/petitive benefits- opportunity for professional development like LEAN Six Sigma CertificationWorkplace TypeThis is a fully onsite position in Beverly,MA.Application DeadlineThis position is anticipated to close on May 12, 2025.About Actalent Actalent is a global leader in engineering and sciences services and talent solutions. We help visionary companies advance their engineering and science initiatives through access to specialized experts who drive scale, innovation and speed to market. With a network of almost 30,000 consultants and more than 4,500 clients across the U.S., Canada, Asia and Europe, Actalent serves many of the Fortune 500. The company is an equal opportunity employer and will consider all applications without regard to race, sex, age, color, religion, national origin, veteran status, disability, sexual orientation, gender identity, genetic information or any characteristic protected by law. If you would like to request a reasonable accommodation, such as the modification or adjustment of the job application process or interviewing due to a disability, please email actalentaccommodation@ for other accommodation options.
Process Engineering Coordinator
Posted 7 days ago
Job Viewed
Job Description
Job DescriptionJob Description
WHAT WE NEED:
Process Engineering Coordinator
The Process Engineering Coordinator is responsible for planning, coordinating, and supporting process engineering activities to ensure the successful execution of multidisciplinary projects. This role involves supporting process design development, managing deliverables, facilitating collaboration across engineering disciplines, and ensuring compliance with industry standards and regulatory requirements. The coordinator acts as a central point of contact between project stakeholders, process engineers, and other departments to ensure alignment of project scope, schedule, and quality expectations.
Responsibilities:
- Coordinate process engineering efforts throughout all project phases, from conceptual development through detailed design, construction, and commissioning.
- Support the development and review of process engineering deliverables, including PFDs, P&IDs, process design basis, line lists, and process data sheets.
- Maintain project schedules for process engineering deliverables, track progress, and ensure timely completion in line with overall project timelines.
- Support the resolution of complex engineering issues by facilitating communication between disciplines and providing process engineering context where required.
- Ensure compliance with applicable codes, standards (e.g., ASME, API, NFPA), and regulatory requirements across all process engineering activities.
- Maintain and organize technical documentation, including process design files, calculation packages, and review comment trackers.
- Support regular project coordination meetings, ensuring that technical issues are identified early and addressed efficiently.
- Interface with clients, contractors, and vendors as required to ensure process design intent is maintained through procurement and implementation.
- Identify opportunities for design optimization, cost savings, and improved project execution efficiency.
- Contribute to the development and continuous improvement of internal engineering standards, workflows, and quality procedures.
WHO WE NEED:
- Bachelor's degree in chemical engineering.
- Minimum of 5 years of experience in process engineering, preferably with experience in projects.
- Strong understanding of process systems, equipment, and design principles across industries such as oil and gas, chemical, fertilizer, or utilities.
- Excellent organizational skills with the ability to manage multiple priorities and deadlines.
- Strong written and verbal communication skills; able to effectively engage with both technical and non-technical stakeholders.
- Attention to detail and commitment to maintaining high-quality deliverables.
- Familiarity with engineering work processes, stage gate project execution, and industry best practices.
WHO WE ARE:
Founded in 1987, Sigma is a professional multi-discipline engineering and design company that serves the petrochemical, fertilizer, and refining industries. Privately owned and operated by Engineers, Sigma's culture empowers employees and clients to choose relationships and projects that fit our values and ultimately act as an extension of our clients. Our technical resources provide unmatched quality in multi-discipline engineering and design, in-plant services, supplier quality inspections, field services, automation, procurement and expediting, construction management, and leadership training.
If you would like to see more of what Sigma is about visit our website at
"We are an equal opportunity employer, and all qualified applicants will receive consideration for employment without regard to , , , , , or expression, , , , status, genetic information, protected veteran status
- Ability to pass pre-employment drug/alcohol screening.
- Ability to pass background screening.
- Must be authorized to work in the United States
Job Posted by ApplicantPro
Process Engineering Specialist
Posted 10 days ago
Job Viewed
Job Description
In this position.
Lead problem solving to assist plants and implementation teams in resolving tooling, equipment and conveyor performance issues and downtime
What you'll do.
-
Support Manufacturing Process Engineering activity for Final Assembly
-
Drive continuous improvement in safety, quality and productivity
-
Apply engineering principles and analytical techniques to establish and continuously improve manufacturing processes and products
-
Develop action plans as required to investigate and prioritize quality concerns and verify corrective actions on internal processes and supplier processes
-
Lead and conduct process audits to ensure process discipline is consistent with Vehicle Operations guidelines
-
Conduct job ergonomic evaluations and deliver corrective actions as required
-
Analyze vehicle inventory root causes; engage in mapping and corrective actions to reduce vehicle inventory
-
Create process and instruction sheets supporting quality methods and processes
-
Deliver capable processes and tools for Trim and Chassis Assembly operations
-
Lead role in resolving assembly related concerns. Lead variability reduction and lean manufacturing initiatives and best practices
-
Ensure compliance to Plant, Corporate, Governmental and Environmental standards
-
Support ISO 14001 compliance and support internal ISO auditing and compliance as required
-
Support continuous improvement in safety, quality and productivity in Chassis and/or Trim areas
-
Identify throughput constraints and drive root cause improvements
You'll have.
-
Education: High School Diploma
-
Experience: 5+ yrs of related experience
-
Successful candidate must be able to demonstrate leadership in ONE FORD (leadership) behaviors combined with outstanding interpersonal, teambuilding, and communication skills
Even better, if you have.
-
Education: Bachelor’s degree in engineering
-
Experience:
-
Effective oral and written communication skills
-
Lean Manufacturing and Six Sigma experience
-
8D and 5Why corrective action and problem-solving skills
-
Lean Tools – 5S, Kanban, Poka-yoke, and Value Stream Mapping
-
DMAIC and DMADV (DFSS) Project Methodology experience
-
TQM and Kaizen Methods
-
FMEA, PPAP, and DOEs experience
-
Visual Factory Management
-
Ergonomic analysis knowledge and experience
You may not check every box, or your experience may look a little different from what we've outlined, but if you think you can bring value to Ford Motor Company, we encourage you to apply!
As an established global company, we offer the benefit of choice. You can choose what your Ford future will look like: will your story span the globe, or keep you close to home? Will your career be a deep dive into what you love, or a series of new teams and new skills? Will you be a leader, a changemaker, a technical expert, a culture builder…or all of the above? No matter what you choose, we offer a work life that works for you, including:
• Immediate medical, dental, and prescription drug coverage
• Flexible family care, parental leave, new parent ramp-up programs, subsidized back-up child care and more
• Vehicle discount program for employees and family members, and management leases
• Tuition assistance
• Established and active employee resource groups
• Paid time off for individual and team community service
• A generous schedule of paid holidays, including the week between Christmas and New Year’s Day
• Paid time off and the option to purchase additional vacation time.
We have a commitment to our products and customers, but also know that our employees are the driving force behind our success. Find out what it is like to love your job. Come discover a Company that is focused on designing better cars, but also cares about you, your family and your community. By choice, we are an Equal Opportunity Employer committed to a culturally diverse workforce.
For a detailed look at our benefits, click here:
(
This position is a range of salary grades 6 and 7.
Visa sponsorship is not available for this position.
Candidates for positions with Ford Motor Company must be legally authorized to work in the United States. Verification of employment eligibility will be required at the time of hire.
We are an Equal Opportunity Employer committed to a culturally diverse workforce. All qualified applicants will receive consideration for employment without regard to race, religion, color, age, sex, national origin, sexual orientation, gender identity, disability status or protected veteran status. In the United States, If you need a reasonable accommodation for the online application process due to a disability, please call 1- .
#LI-Onsite
#LI-JL1
NA
NA
Requisition ID : 46861
Be The First To Know
About the latest Industrial plants Jobs in United States !
Process Engineering Coordinator
Posted 11 days ago
Job Viewed
Job Description
WHAT WE NEED:
Process Engineering Coordinator
The Process Engineering Coordinator is responsible for planning, coordinating, and supporting process engineering activities to ensure the successful execution of multidisciplinary projects. This role involves supporting process design development, managing deliverables, facilitating collaboration across engineering disciplines, and ensuring compliance with industry standards and regulatory requirements. The coordinator acts as a central point of contact between project stakeholders, process engineers, and other departments to ensure alignment of project scope, schedule, and quality expectations.
Responsibilities:
- Coordinate process engineering efforts throughout all project phases, from conceptual development through detailed design, construction, and commissioning.
- Support the development and review of process engineering deliverables, including PFDs, P&IDs, process design basis, line lists, and process data sheets.
- Maintain project schedules for process engineering deliverables, track progress, and ensure timely completion in line with overall project timelines.
- Support the resolution of complex engineering issues by facilitating communication between disciplines and providing process engineering context where required.
- Ensure compliance with applicable codes, standards (e.g., ASME, API, NFPA), and regulatory requirements across all process engineering activities.
- Maintain and organize technical documentation, including process design files, calculation packages, and review comment trackers.
- Support regular project coordination meetings, ensuring that technical issues are identified early and addressed efficiently.
- Interface with clients, contractors, and vendors as required to ensure process design intent is maintained through procurement and implementation.
- Identify opportunities for design optimization, cost savings, and improved project execution efficiency.
- Contribute to the development and continuous improvement of internal engineering standards, workflows, and quality procedures.
WHO WE NEED:
- Bachelor's degree in chemical engineering.
- Minimum of 5 years of experience in process engineering, preferably with experience in projects.
- Strong understanding of process systems, equipment, and design principles across industries such as oil and gas, chemical, fertilizer, or utilities.
- Excellent organizational skills with the ability to manage multiple priorities and deadlines.
- Strong written and verbal communication skills; able to effectively engage with both technical and non-technical stakeholders.
- Attention to detail and commitment to maintaining high-quality deliverables.
- Familiarity with engineering work processes, stage gate project execution, and industry best practices.
WHO WE ARE:
Founded in 1987, Sigma is a professional multi-discipline engineering and design company that serves the petrochemical, fertilizer, and refining industries. Privately owned and operated by Engineers, Sigma's culture empowers employees and clients to choose relationships and projects that fit our values and ultimately act as an extension of our clients. Our technical resources provide unmatched quality in multi-discipline engineering and design, in-plant services, supplier quality inspections, field services, automation, procurement and expediting, construction management, and leadership training.
If you would like to see more of what Sigma is about visit our website at
"We are an equal opportunity employer, and all qualified applicants will receive consideration for employment without regard to race, color, religion, sex, sexual orientation, gender identity or expression, pregnancy, age, national origin, disability status, genetic information, protected veteran status
- Ability to pass pre-employment drug/alcohol screening.
- Ability to pass background screening.
- Must be authorized to work in the United States
Process Engineering Technician
Posted 16 days ago
Job Viewed
Job Description
RSCC Wire & Cable LLC
Come join a team where People make the difference! As a part of Marmon Holdings, Inc., a highly decentralized organization, we rely heavily on people with the aptitude, attitude, and entrepreneurial spirit to drive our success, and we're committed to attracting and retaining top talent.
The Process Engineering Technician is responsible for duties related to assisting with the development of new materials, producing wire and cable prototype samples, and assisting with research and developmental test plans.
Essentials Duties:
- Responsible for processing samples of wire and cable along with components and mitigating issues.
- Develop, train and maintain SOP's, including set-up procedures, operating conditions and shut down procedures for R&D equipment.
- Develop, train and maintain trouble shooting manuals for the machining equipment.
- Develop process on equipment when changes/updates occur from the supplier.
- Conducting research and developmental testing
- Ability to work independently to read and interpret specifications.
- Assist and participate in Lean/5S and continuous improvement initiatives.
- Work closely with the Development Engineer, Materials Development Manager, as well as outside Specialists to support and assist with process troubleshooting and special projects as assigned.
- Work as a team with peers, supervisors, managers and Marmon I&T employees
- Keep a clean and organized work area.
- Responsible for all other projects, tasks, etc., as assigned.
- 2-5 years as a process technician or similar role.
- High School Diploma/GED required, Associates Degree preferred.
- Experience in a manufacturing environment.
- Hands-on wire and cable experience preferred.
- Must be able to perform basic arithmetic, statistics, and other specific mathematical applications.
- Ability to read and write clearly.
- Ability to organize and prioritize work tasks efficiently.
- Basic knowledge of computer programs related to manufacturing.
- Ability to communicate with all levels of employees.
- Must be able to multi-task, follow priorities given, and have strong troubleshooting techniques.
- Self-starter: ability to work with minimal supervision.
- Ability to work in a manufacturing environment that can be noisy.
- Ability to follow safety guidelines and wear required PPE.
- Ability to work long hours while standing and operating machinery.
- Ability to work in high temperatures.
- Ability to move objects and materials of at least 50lbs.
Marmon Industrial Energy and Infrastructure East Granby is an Equal Opportunity Employer and makes employment decisions without regard to, and prohibits discrimination based on, race, color, religion, age, sex, pregnancy, national origin, sexual orientation, gender identity, disability, veteran status, or any other characteristic protected by applicable federal, state, or local laws.
Following receipt of a conditional offer of employment, candidates will be required to complete additional job-related screening processes as permitted or required by applicable law.
We are an equal opportunity employer, and all applicants will be considered for employment without attention to their membership in any protected class. If you require any reasonable accommodation to complete your application or any part of the recruiting process, please email your request to , and please be sure to include the title and the location of the position for which you are applying.
Process Engineering Technician
Posted 22 days ago
Job Viewed
Job Description
The Process Engineer Technician in the Process Engineering Group supports a team of engineers in the execution and improvement of propellant, pyrotechnic, and explosive manufacturing at the Mesa, Arizona facility. This position will provide technical and mechanical support for new, continuing, and engineering production efforts. In addition, the technician monitors processes/KPIs, trains manufacturing operators, authors/updates/redlines process documentation, and ensures work instruction implementation as directed by engineering.
How you will be rewarded as our Process Engineering Technician:
-
Competitive compensation
-
Monday-Thursday work week working four 10-hour days (off on Fridays)
-
Generous paid time off and Holiday Pay
-
Medical, Dental and Vision Insurance
-
401(K), employee assistance programs, health savings account
KEY RESPONSIBILITIES:
• Apply basic engineering level principles to safely process propellants, pyrotechnics, and/or explosives for product development or improvement to meet program requirements.
• Assist in the development of new tooling, processes, and techniques.
• Prepare technical reports detailing work progression and results.
• Ability to troubleshoot and assess risks.
• Provide training to operators.
• Review results of experiments and analyses performed by either engineering or operators.
• Collaborate with operators, quality, and engineering teams to sustain and improve current processes.
• Follow standard practices and safety procedures.
• Collect data and ensure its accuracy.
• Coordinate and schedule support work for other departments.
• Wear safety equipment such as protective eyewear, coveralls, conductive footwear, respirators, or self-contained breathing apparatus.
• Occasionally exert up to 50 lbs. of force in the course of normal work.
• Additional duties as required.
• Follow standard practices and safety procedures.
• Strictly adhere to all safety policies and procedures to ensure a safe working environment.
COOPERATION:
This role requires collaboration across internal teams and with external stakeholders.
LEVEL OF DECISION MAKING:
This position requires daily autonomous decision-making capabilities when working with both internal and external customers.
SKILLS & QUALIFICATIONS:
• Associate degree in a technical field or High School/General Education Diploma (GED) with hands-on work experience
• Minimum 0 years of experience with propellants, pyrotechnics, and/or explosives
• Proficient operator of larger and handheld equipment (pumps, forklift, mixers, hydraulics, feeder/extruders, compressors, particle size analyzer, ovens, drill press, etc.)
• Hands on experience with program/project work in applied R&D and/or production support
• Ability to obtain approval through ATF to handle Nammo Defense Systems’ products and information.
• Basic understanding of mechanical and electrical systems and interpreting their drawings
• Proficient in using basic hand tools and familiarity with precision measurement tools
• Safe operation of powered tools and equipment
• Ability to perform basic assembly and disassembly of components
• Conduct simple functional tests and inspections
• Recognize and escalate abnormal conditions, defects, or test results
• Follow written work instructions and procedures accurately
• Accurately record test data and observations
• Communicate findings clearly to engineering or supervisory staff
• Basic computer literacy (email, Excel, Word, simple data entry)
• Adherence to all safety policies and procedures
• Good housekeeping in work areas
• Ability to learn and take direction
• Dependable and punctual work ethic
• Ability to work effectively with the cross-functional NDS Mesa Team
**Must be able to obtain BATF approval
DESIRED SKILLS:
• General understanding of chemical science (overlapping polymers, analytical measurements, and physical properties)
• A working knowledge of energetic material regulations and safe handling/measurement
• Minimum 2 years of experience in manufacturing/laboratory environment (chemical industry preferred)
COMPETENCIES:
• Excellent communication and collaboration skills.
• Strong problem-solving and critical-thinking abilities.
• Ability to work in fast-paced environments.
• Leadership or teamwork abilities.
WORKING CONDITIONS:
• Full-time on-site position
• This position may require working in diverse settings and conditions.
Note : Due to US Export Control laws and regulations; applicants selected for employment must show proof of a U.S. Person status before employment may begin.