1,729 Process Engineer jobs in the United States
Industrial/Process Engineer
Posted 7 days ago
Job Viewed
Job Description
Job Type
Full-time
Description
ME Elecmetal is a globally competitive supplier, recognized by its excellence and leadership in the delivery of integral solutions which add value to the mining processes and to other target markets. Our fast-paced production environment is recruiting for a talented and experienced Industrial Engineer in its Duluth, MN foundry.
Industrial Engineer: The Industrial Engineer will develop and maintain systems to accurately measure the specific cost of all products. Establish and maintain production standards, systems, and methods. Provide accurate product quotations and costs. Reduce operating costs by improving methods, processes, equipment, and materials for the effective utilization of human and plant resources to improve quality and productivity.
- Maintain costing, labor, quoting, and engineering data in the SAP Product Master.
- Coordinate, monitor, and ensure proper administrative controls are completed accurately by the appropriate person on all samples.
- Develop and maintain production standards through time studies, audits and other analytical processes to determine accurate product cost and efficiencies.
- Develop alternative production methods where appropriate based on labor and cost reductions.
- Keep Manager, Manufacturing informed of all relevant activity and actions.
- Maintain knowledge and understanding of the developments and changes in foundry technology.
This position must have an Engineering degree in Industrial Engineering, Systems Engineering, or a closely related field with a minimum of 1 year of related experience.
All qualified candidates must be:
- Committed to creating a safe work environment
- Adhere to high performance standards
- Able to work in a hot environment
- Committed to producing high quality products
- Willing to work in an environment that expects excellence.
OUR VISION:
Our Vision is to be a globally competitive supplier, recognized by its excellence and leadership in the delivery of integral solutions which add value to the mining processes and to other target markets.
OUR MISSION:
Our mission is to meet the needs and exceed the expectations of our shareholders, customers, employees, and communities where we operate, by providing comprehensive solutions to the market.
Our Values:
- Respect for integrity
- Teamwork
- Commitment to the community and environment
- Creativity and innovation
- Customer focus
- Proactive search for excellence
- Human development
- Responsibility and integrity
We are looking for employees who share our vision, mission and values. ME Elecmetal is an Equal Opportunity Employer and Drug Free Workplace.
Salary Description
$75,000 - $100,000
Industrial Process Engineer
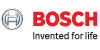
Posted 1 day ago
Job Viewed
Job Description
Welcome to Bosch Power Tools in West Memphis, AR, where innovation meets action in our bustling warehousing operation! As a key division of Robert Bosch Tool Corporation NA, we're not just distributing top-tier power tools-we're driving excellence and efficiency every step of the way. Our facility is a hub of activity, where every day is an adventure in logistics and distribution.
Here at Bosch Power Tools, we infuse our work with passion, energy, and a sense of ownership. Our team thrives on the excitement of optimizing operations and delivering high-quality tools to professionals around the world. We believe in making work fun and engaging while pushing the boundaries of what's possible in warehousing and distribution.
If you're ready to join a team where your drive and enthusiasm are valued, and where every role contributes to our mission, come experience the #LikeABosch spirit with us!
**Job Description**
The Industrial Process Engineer is responsible for driving operational excellence within both distribution and production environments. This role ensures process efficiency and standardization through the application of Bosch Production System principles, Lean Manufacturing concepts, and data-driven problem-solving methodologies. The Industrial Process Engineer collaborates with cross-functional teams to integrate new products, optimize workflows, and meet customer expectations while maintaining cost targets and safety standards.
**Primary Duties and Accountabilities:**
Operational Excellence and Continuous Improvement: Drive operational excellence initiatives with Engineering, Design, Project Management, Operations, and Logistics teams. Utilize Lean Production principles and BPS methodologies to identify and implement process improvements.
Process Standardization and Optimization: Support standardization and modularization in a Make-to-Order (MTO) environment to enhance efficiency. Integrate new products and processes into existing manufacturing systems while ensuring seamless transition.
Cost and Quality Control: Analyze product cost drivers and implement changes to meet cost targets. Define, measure, analyze, implement, and improve processes using data-driven approaches.
Problem Solving and Data Analysis **:** Utilize Plan-Do-Check-Act (PDCA) and A3 methodologies to control processes and drive sustainable improvement.
Cost and Quality Control: Analyze product cost drivers and implement changes to meet cost targets. Define, measure, analyze, implement, and improve processes using data-driven approaches.
Shop Floor and Logistics Support: Provide direct shop floor support to resolve process-related issues. Collaborate with engineers, planners, supervisors, and associates to optimize material flow and production efficiency. Apply Statistical Process Control (SPC) techniques and problem-solving tools in a production setting.
Software and Systems Utilization: Use SAP and Microsoft Office tools for data analysis and report generation. Work with CAD software to support process and line design activities.
Safety and Compliance: Ensure compliance with industrial safety requirements, including ergonomics and control system functionality. Develop and implement safety-conscious process improvements.
**Qualifications**
+ Bachelor's degree in Industrial Engineering, Mechanical Engineering, Electrical Engineering, Mechatronics or a related technical field required.
+ BPS (Bosch Production System) knowledge and experience preferred
+ Microsoft Excel, Word, Outlook and Warehouse Management (WMS) familiarity preferred
+ Knowledge of quality processes, product requirements, as well as quality hold reasons, typical product damages, and customer requirements for products.
+ 3-5 years of previous experience in a similar position
**Proficiency:**
+ Proven aptitude for line design, logistic movements, and process optimization.
+ Experience in executing projects and implementing Lean Manufacturing concepts.
+ Strong analytical and problem-solving skills with attention to technical details.
+ Ability to effectively communicate and collaborate across departments.
+ Proficiency in CAD software, SAP and data analysis tools.
+ Knowledge of industrial safety regulations and ergonomic standards.
+ Excellent verbal and written communication skills.
**Additional Information**
BOSCH is a proud supporter of STEM (Science, Technology, Engineering & Mathematics) Initiatives
+ FIRST Robotics (For Inspiration and Recognition of Science and Technology)
+ AWIM (A World In Motion)
Equal Opportunity Employer, including disability/veterans.
Thanks to the work of every associate, Bosch has been recognized for award-winning culture by the following organizations:
+ Great Place to Work Certified, 2024
+ Fortune's World's Most Admired Companies, 2024
+ America's Best Large Employers, 2024
+ America's Best Employers for Diversity, 2024
+ America's Greatest Workplaces for Women, Newsweek2024
+ Greatest Workplaces for Diversity, Newsweek 2024
**Indefinite U.S. work authorized individuals only. Future sponsorship for work authorization is not available.**
The U.S. base salary range for this full-time position is $90,000 to $105,000. Within the range, individual pay is determined based on several factors, including, but not limited to, work experience and job knowledge, complexity of the role, job location, etc.
In addition to your base salary, Bosch offers a comprehensive benefits package that includes health, dental, and vision plans; health savings accounts (HSA); flexible spending accounts; 401(K) retirement plan with an attractive employer match; wellness programs; life insurance; short and long term disability insurance; paid time off; parental leave, adoption assistance; and reimbursement of education expenses. Learn more about our full benefits offerings by visiting: . Pay ranges included in the postings generally reflect base salary; certain positions may include bonus, commission, or additional benefits.
Salary estimates published on online job boards, rather than the Bosch US Careers Page, may not be a true representation of the actual pay range offered for this position.
Industrial Process Engineer
Posted 18 days ago
Job Viewed
Job Description
Are you a process engineer with a passion for working on complex industrial (refining, chemical and power) engineering projects in a dynamic, multi-disciplinary environment? Eichleay is looking for an Industrial Process Engineer to join our process engineering team at Eichleay. This position offers the flexibility to work remotely. It may be based from a home office within 50 miles of one of Eichleay’s office locations - Orange, CA; Larkspur, CA; Billings, MT; or Ferndale, WA. We also welcome applicants located in states where Eichleay operates across the Western U.S., including CA, CO, ID, MT, NV, and WA. Please note that all remote roles will involve periodic travel. Don’t miss out on this exciting career move!
Compensation : $100,000-$150,000 *anticipated annual salary may vary based on skills, experience, qualifications and internal peer equity. The pay range listed for this position is based on the anticipated base compensation at the time of the posting.
Company Overview:
Eichleay is a dynamic organization with over 150 years of experience in delivering project management and engineering solutions across various industries, including life sciences, energy, and chemicals, power, and food and beverage. We are committed to innovation, excellence, and building long-lasting relationships with our clients.
Position Summary:
Do you enjoy getting involved in small to large projects collaborating with multi-disciplinary teams of engineers and designers? At Eichleay you will perform design engineering for a variety of brown field and revamp facilities in the refining, chemical and power industries. Design engineering consists of feasibility through detailed design and construction for reimbursable & lump sum projects.
Your duties will include performing process simulations / studies, heat and material balances, process flow diagram (PFD) and piping & instrumentation diagram/drawings (P&ID) development, design calculations, hydraulics and line sizing, equipment data sheets/specifications, utility requirements/systems analysis, relief contingency analysis and pressure safety valve (PSV) sizing, process engineering reports, and proposal development.
You may provide technical guidance to less experienced design and engineering personnel.
Key Responsibilities:
- Apply extensive and diversified knowledge of Chemical Engineering principles to complete process engineering tasks with minimal supervision.
- Interface with other internal engineering disciplines (mechanical, piping, civil/structural, electrical, instrumentation, automation, architecture) to ensure a coordinated design and complete engineering deliverables.
- Work on all project phases from feasibility studies, conceptual design, detailed design and construction support.
- Develop process data sheets for stationary and rotating equipment including pressure vessels, tanks, separators, filters, heat transfer equipment, pumps, and compressors.
- Review vendor drawings to ensure design accuracy and compliance with specifications.
- Oversee and/or produce process engineering calculations such as pressure drop, PSV sizing, and equipment sizing.
- Perform utility sizing calculations and utility system analysis.
- Prepare and complete equipment Qualification and/or Commissioning documentation.
- Participate in Process Hazard Analysis (PHA) sessions.
- Attend Factory Acceptance Testing and Site Acceptance Testing.
- Provide construction support activities including responding to submittals and RFIs.
- Consistently achieve goals, deliver quality and accurate work, and meet timelines. This includes reviewing project documents for conformity and quality assurance.
- May independently lead projects, manage process budgets and resources for small to medium sized projects.
Job Requirements:
- Experience: Minimum of 5 years of experience in process engineering, with demonstrated expertise in applying Chemical Engineering principles to execute complex, multi-discipline refinery or chemical plant projects.
- Education: Bachelor of Science in Chemical Engineering from an ABET accredited program.
- Skills: Strong communication skills, including writing skills, preparing reports to describe design conclusions, deliver presentations, analyses, etc.
Technical Competence:
- Experience developing process data sheets for stationary and rotating equipment including pressure vessels, tanks, separators, filters, heat transfer equipment, pumps, and compressors.
- Thorough knowledge of API, ASME and ANSI standards.
- Simulation experience using HYSYS, PRO II or other comparable process simulation software.
- Understanding of refinery or chemical plant unit operations.
- Proven ability to develop PFDs and P&IDs.
- Safety: Demonstrates awareness and commitment to health, safety, and environmental issues. Addresses those issues as necessary to ensure zero harm to all employees, clients, and contractors with zero environmental incidents.
- Collaboration: Ability to form and foster collaborative relationships within Eichleay and with clients and partners.
Preferred Skills/Experience:
- Professional Engineer (PE) Certification preferred
Industry Requirements:
This role may require all or some of the following requirements (as applicable):
- Client cGMP and Sterile Area Training and current badge or ability to obtain.
- RSO Safety Training and current card or ability to obtain.
- Client Safety Training and current badge or ability to obtain.
- TWIC Certification and current card or ability to obtain.
- Background screening including previous employment, education, criminal history, and driving record verification.
- Participation in random drug and alcohol program.
Work Environment and Physical Demands:
The characteristics described below are representative of those encountered while performing the essential functions of this position. Reasonable accommodation will be made to enable individuals with disabilities to perform the essential functions.
While performing duties of this job, you would occasionally be required to stand, walk, sit, reach with hands and arms, climb or balance, stoop or kneel, talk and hear (this includes being able to hear and talk on site based communication equipment), distinguish between various colors, be able to hear safety tones/notifications, and use fingers and hands to feel objects, tools, temperature or controls.
- Must occasionally lift and/or move up to 25 pounds.
- Specific vision abilities required include close vision, distance vision, depth perceptions, and the ability to adjust focus.
- Overtime may be necessary as workload dictates. This may include weekdays, weekends and/or holidays.
- Job duties may be performed at a Client’s office, client site, production facility or industrial/construction job site. Day to day job direction will typically be lead by our Clients designated project leader.
- Conditions and/or schedule will vary at each Client location, but the conditions listed above will generally apply.
- Candidates will be required to follow our clients' site based rules and protocols regarding infectious diseases.
All opportunities with Eichleay will require authorization to work in the US without the need for sponsorship. Positions will require in-person interactions and may require working onsite in an office or field envir onment. This position is subject to federally mandated drug/alcohol testing. Candidates applying to Eichleay must have the ability to be badged and maintain a badge as a safety sensitive position and/or within the Building and Construction trade for process safety management governed facilities. This will require in-depth drug screening for all positions.
We are an equal opportunity employer and value diversity at our company. Qualified applicants will receive consideration for employment without regard to race, color, religious creed, sex (including pregnancy, childbirth, breast-feeding and related medical conditions), sexual orientation, gender identity, gender expression, national origin or ancestry, age, mental or physical disability (including medical condition), military or veteran status, political preference, marital status, citizenship, genetic information or other status protected by law or regulation.
Education Required- Bachelors or better in Engineering
- cGMP Certification
- Professional Engineer
- TUV Certification
- TWIC
- Adaptability
- AutoCAD
- Automation
- Bluebeam
- Cadworks
- Application of codes and standards
- Collaboration
- Communication
- Computer skills
- Construction support
- Creativity
- Critical thinking
- Attention to detail
- Estimates
- Phase gate
- Interpersonal
- Quick learner
- Material requisition
- Navis Works
- Problem-solving
- Presentation skills
- Quality assurance
- Revit
- Research skills
- Software skills
- Technical bid evaluation
- Teamwork
- Time management
- Work package
Equal Opportunity Employer
This employer is required to notify all applicants of their rights pursuant to federal employment laws. For further information, please review the Know Your Rights notice from the Department of Labor.
Industrial Process Engineer (F/M/X)
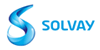
Posted 9 days ago
Job Viewed
Job Description
32485
**Industrial Process Engineer (F/M/X)**
Regular
My candidate profile ( is all about chemistry. We're not just referring to chemical reactions here, but also to the magic that occurs when the brightest minds get to work together. This is where our true strength lies. In you. In your future colleagues and in all your differences. And of course, in your ideas to improve lives while preserving our planet's beauty for the generations to come.
**About the role**
+ Our GBU Peroxides Industrial Technology Team, composed of four people (three engineers reporting to the GBU Peroxides Technology Development Manager - H2O2), is integrated into the GBU Peroxides Operations & Innovation department and focuses on providing a solid foundation of technical knowledge and competencies to ensure safe, sustainable, and effective operation of all of our 20+ GBU Peroxides sites worldwide. This is in collaboration with site production teams and the wider GBU Peroxides Industrial network.
+ As a GBU Industrial Process Engineer, you will work on acquiring solid knowledge of H2O2 plant safety and processes, analyzing and optimizing processes using digital tools like Advanced Analytics and Machine
+ Learning, and supporting production teams in troubleshooting to ensure plant and process performances meet targets. You will have the opportunity to contribute to continuous improvement and innovation and have a positive impact on global H2O2 production efficiency, safety, and sustainability.
+ You will be accountable for:
+ Acquiring and applying solid knowledge of H2O2 plant safety and processes.
+ Analyzing and following up on H2O2 process performance, including catalyst and organic working solution management.
+ Supporting production teams in troubleshooting and ensuring final product quality and quantity.
+ Conducting process optimization using digital tools and applying best practices.
+ Ensuring continuous improvement, proposing capital investments, and participating in regional/global projects.
+ We offer a permanent contract based on an on-site working mode, with travel for short-term missions.
**About you**
+ Relevant education degree or equivalent in Chemical Engineering.
+ Relevant work experience: 0 to 3 years of working experience in the chemical industry.
+ Competencies:
+ Analytical & conceptual thinking
+ Process analysis and optimization (including digital tools like JMP15, Advanced Analytics, Machine Learning)
+ Troubleshooting & problem solving
+ Chemical engineering design and process development
+ Project management
+ Fluent in English; other languages are a plus
+ Behaviors:
+ Eager to learn and proactive with a strong personal commitment
+ Excellent communication and collaboration/teamwork skills
+ Able to work under pressure and ready to work abroad for short-term missions
+ Demonstrates insights and a focus on continuous improvement
**About the pay and benefits**
+ Attractive and equitable pay for all: compensation is determined within a range to foster your development in the role. While the Belgium base pay reasonably expected for this role is 65,000 EUR to 86,000 EUR, your salary may ultimately be higher or lower based on your skills and experience. Additionally, we provide a competitive total rewards package that includes a bonus and/or other incentives.
+ Solvay Cares program: minimum of 16 weeks of parenting leave for all employees and package with healthcare, disability and life insurance coverage.
+ Prioritization of well-being: work-life balance promotion, flexible approach to work part-time or hybrid work arrangements (depending on the type of job), employee assistance program with access to physical and psychological support.
+ Professional development: prioritization of internal talents for career progression, access to a training platform, opportunities to join Employee Resource Groups (ERG) for experience sharing and mentorship and free language courses.
About us
+ Solvay, a pioneering chemical company with a legacy rooted in founder Ernest Solvay's pivotal innovations in the soda ash process, is dedicated to delivering essential solutions globally through its workforce of over 9,000 employees. Since 1863, Solvay harnesses the power of chemistry to create innovative, sustainable solutions that answer the world's most essential needs such as purifying the air we breathe and the water we drink, preserving our food supplies, protecting our health and well-being, creating eco-friendly clothing, making the tires of our cars more sustainable and cleaning and protecting our homes. As a world-leading company with 4.7 billion in net sales in 2024 and listings on Euronext Brussels and Paris (SOLB), its unwavering commitment drives the transition to a carbon-neutral future by 2050, underscoring its dedication to sustainability and a fair and just transition.
+ At Solvay, we seek to promote unity and not uniformity. We value the diversity that individuals bring and we invite you to consider a future with us, regardless of background, age, gender, national origin, ethnicity, religion, sexual orientation, ability or identity. We encourage individuals who may require any assistance or accommodations to let us know to ensure a seamless application experience. We are here to support you throughout the application journey and want to ensure all candidates are treated equally. If you are unsure whether you meet all the criteria or qualifications listed in the job description, we still encourage you to apply.
#LI-ET1 #LI-Hybrid #middle
Job ID
32485
Regular
Manufacturing Process Engineer
Posted 4 days ago
Job Viewed
Job Description
Job ID Number
R5743Employment Type
Full timeWorksite Flexibility
OnsiteJob Summary
As Manufacturing Engineer, you will lead process optimization and standardization for molding and assembly, design and develop manufacturing processes and automation platforms, support product development with tool selection and optimization, and ensure manufacturability for new designs and smooth production ramp-up while advising plants on improvements.Job Description
We are looking for a highly motivated Manufacturing Engineer to join our Advanced Manufacturing Engineering Team in Mount Joy, PA. This contract position will be full-time and onsite. The work schedule for this role is 7:00am to 4:00pm or 8:00am to 5:00pm Monday-Friday.
This position requires access to information which is subject to stringent controls under the International Traffic in Arms Regulations (ITAR) or Export Administration Regulations (EAR). Applicants must be a U.S. citizen or national, U.S. lawful permanent resident, person granted asylee status in the U.S., or person admitted into the U.S. as a refugee
What You'll Do
Support large scale migrations projects from a data management and Industrial Engineering perspective
Support resolving Engineering Changes in SAP related to industrial engineering and data management for correct costing, scheduling, etc.
Works with cross functional teams to create cost models for P&L
Enter and maintain BOM's and process routing in SAP with Product Engineering, Manufacturing Engineering and Management for accuracy
Performs manufacturing process time studies
Identify cost drivers for focused improvement efforts / mfg. tooling or process opportunities
Engages and collaborates with plant finance and plant IE team members for accurate representation of cost rate assumptions, parameter assumptions and finance methodologies
Works directly with Mfg. Engineering team to establish ballpark estimates for tooling and develops cost model to determine manufacturing costs
Identifies cost-saving opportunities for both material and process savings
Maintains capacity database to ensure plant can handle added capacity created by business growth
Evaluates capacity impact for proposed modifications on existing tooling / process / plant operations to help sourcing decision
Creates phased Mfg. capacity plans for ALL New Product Development projects
Communicates plans for add-on capital per New Product Development P&L for potential creation of sustaining capacity add project
Supporting the integration of previously unconnected processes (departments) into one interconnected extended value stream from the customer's perspective
Developing and utilizing current and future state value stream maps to identify strategic projects
Willing to work between two different facility locations
What You'll Need
Required
Demonstrated success in project management within a manufacturing environment, delivering measurable results
Minimum of 5 years' experience working within Industrial Engineering and Project Management discipline or environment
Experience with lean manufacturing, Six Sigma, or other continuous improvement methodologies
Experience with SAP or other MRP systems
Excellent oral and written communication skills with the ability to communicate across all levels within and outside of the organization
Capability to work in a fast paced, dynamic global environment with multiple changing priorities
Proficient in MS Office Software such as Excel, Word, and PowerPoint
Demonstrated ability to work within a cross-functional team.
Excellent organizational and problem-solving skills
Preferred
Bachelor of Industrial Engineering or similar Advanced degree preferred
Experience working in a low volume, high mix environment is preferred
Experience with military/aerospace products is a plus
Knowledge in statistical software packages such as JMP and Minitab desirable but not required
Physical Demands
Ability to safely and successfully perform the essential job functions consistent with the ADA and other federal, state, and local standards
Sedentary work that involves sitting or remaining stationary most of the time with occasional need to move around the office to attend meetings, etc.
Ability to conduct repetitive tasks on a computer, utilizing a mouse, keyboard, and monitor
The pay range for this position is $50.00- $55.00 per hour (USD). Exact compensation may vary based on several factors, including location, experience, and education. Benefit packages for this role includes medical, dental, and vision insurance, as well as 401k retirement account access. Employees in this role may also be entitled to paid sick leave as provided by applicable law.
#LI-AL1
Reasonable Accommodation Statement
If you require a reasonable accommodation in completing this application, interviewing, completing any pre-employment testing, or otherwise participating in the employment selection process, please direct your inquiries to or (888) 824 - 8111.
Equal Employment Opportunity Policy Statement
CAI is committed to equal employment opportunity. We do not discriminate based on race, color, religion, sex, sexual orientation, gender identity, national origin, age, marital status, genetic information, disability, or veteran status. All employment decisions are based on valid job requirements, including hiring, promotion, and compensation. Harassment and retaliation are prohibited.
Manufacturing Process Engineer
Posted 6 days ago
Job Viewed
Job Description
Overview
Pactiv Evergreen is now a part of Novolex. Novolex is a leading manufacturer of food, beverage, and specialty packaging that supports multiple industries, including foodservice, restaurant delivery and carryout, food processing, grocery and retail, and industrial sectors. Our innovative product portfolio is designed to meet the diverse needs of businesses worldwide and the millions of customers they serve. Through continuous investment in research and development, we are committed to engineering more sustainable choices for the future. Our extensive manufacturing network spans North America and Europe, including two world-class plastic film recycling centers. Discover more about Novolex, our 20,000+ family members and our commitment to innovation and sustainability at .
This position is not eligible for any type of employment sponsorship, such as OPT, H1B, TN, F1, etc.
Responsibilities
The Manufacturing Process Engineer - Quality is responsible for developing and improving the manufacturing processes surrounding the production of Molded Fiber products and providing leadership for associates assigned to support quality and process monitoring.
-
Works with management, technicians and operators to continually improve manufacturing processes (Decrease cycle times/optimize production, maximize throughput rate, increase product quality, and minimize scrap) and troubleshooting processing problems.
-
Creates and maintains accurate engineering/process documentation such as molding specifications, Process Flow diagrams, Process Failure Modes and Effects Analyses (PFMEAs), etc.
-
Establishes set-up and processing parameters based on material, machine capabilities.
-
Develops molding procedures to ensure consistent processing of product on all shifts.
-
Monitors and reviews daily production efficiencies with Production Manager on machine/process to ensure consistent processing.
-
Performs specified design of experiments and establish capability studies.
-
Participates in documenting capital equipment justification.
-
Oversees the lab & process technicians, testing results, procedures, and overall quality program.
-
Lead Quality root cause investigations.
-
Monitors and coordinates responses to quality concerns from internal and external sources.
-
Manages and coordinates the NSF audit and GMP standards for the plant.
-
Immediately addresses and reports safety issues or hazards.
-
Maintains excellent safety record.
-
Maintains excellent attendance record.
-
Performs other duties as assigned.
Qualifications
Qualifications:
-
BA/BS in Chemical, Mechanical or Industrial Engineering required.
-
Three or more (3+) years of experience in a manufacturing environment; including successful completion of jobs or similar activities requiring control of a mechanical process and inspection of product to meet quality standards.
-
Three or more (3+) years of experience managing and leading direct reports in a manufacturing environment or relevant experience.
-
Must have Continuous Improvement experience
-
SPC Gain Seeker experience
-
Food Safety / GMP experience highly desired.
-
Paper science or paper making experience highly desired.
-
Must have management/supervisory experience.Must have analytical skills and proven leadership effectiveness.
-
Experience and/or working knowledge of Solid Works and AutoCAD is a plus.
-
Demonstrated self-compliance with company policies and procedures.
-
Effective verbal and written communication skills.
-
Proficient with Microsoft Office products.
-
PI systems experience (digital EOT systems)
-
Proficient to expert knowledge in pulp and fiber process and tooling.
-
Troubleshooting and problem-solving skills.
-
Time management.
-
Advance mathematical skills and numerical accuracy.
This position is eligible for an annual incentive bonus, 401(k) plan with no waiting period and dollar for dollar match up to 6% and immediate vesting, comprehensive medical, dental, and vision insurance, flexible spending and health savings accounts, paid time off, paid parental leave, up to nine paid Holidays and two floating Holidays, wellness program, tuition reimbursement and family care benefits.
Pactiv Evergreen is committed to a diverse and inclusive workforce. Pactiv Evergreen is an Equal Opportunity Employer. All qualified applicants will receive consideration for employment without regard to race, color, sex (including pregnancy), sexual orientation, religion, creed, age national origin, physical or mental disability, genetic information, gender identity and/or expression, marital status, veteran status or other characteristics or statuses protected by law. For individuals with disabilities who would like to request an accommodation, please call ( or email
All information will be kept confidential according to EEO guidelines and applicable laws.
Our Social Responsibility platform features a robust, employee-led Give Back program, which includes a matching gifts plan, community grants initiative, and our annual Company-wide Month of Action campaign. With each of these initiatives, our employees are empowered and equipped to give back to their communities and support the non-profits important to them and their families. Through our Give Back program, we own our commitment to Social Responsibility and live our purpose of Packaging a Better Future.
#LI-TM1
#INMISC
Job Locations US-GA-Macon
ID 2024-26228
Category Engineering
Position Type Full Time
Pay Type Salaried
Manufacturing Process Engineer
Posted 6 days ago
Job Viewed
Job Description
Brand: Post Consumer Brands
Categories: Engineering
Locations: Battle Creek, Michigan
Position Type: Regular Full-Time
Remote Eligible: No
Req ID: 26556
Job Description
Business Unit Overview
Headquartered in Lakeville, Minn., Post Consumer Brands, a business unit of Post Holdings, Inc., is dedicated to providing people and their pets with delicious food choices for every taste and budget. The company's portfolio includes beloved brands such as Honey Bunches of Oats®, PEBBLES®, Grape-Nuts® and Malt-O-Meal® cereal, and Peter Pan® peanut butter, as well as Nutrish®, Kibbles 'n Bits® and 9Lives® dog and cat food. As a company committed to high standards of quality and to our values, we are driven by one idea: To make lives better by making delicious food accessible for all. For more information about our brands, visit and follow us on LinkedIn and Facebook for the latest news. Brand Post Consumer Brands recently acquired several iconic pet food brands, venturing into a new market while remaining true to our purpose to provide delicious and accessible food that our consumers love. We're always searching the center store for the next exciting product to add to our portfolio, and right now, we're growing and need passionate, driven individuals with diverse perspectives to help us reach greater heights. That's where you come in. Join a team where your voice is not only heard but valued. Make a real impact on brands enjoyed by millions of people and their pets. At Post Consumer Brands, we take pride in our longstanding legacy of making one of every five breakfast cereals families eat daily. Today, we're just as focused on our future as we expand our grocery business with different shelf-stable foods, including snacks and peanut butter. We are committed to providing accessible and delicious food for families, and we're always searching the center store for the next exciting product to add to our portfolio. As we soar to new heights, we need creative, determined individuals from all walks of life to join our team, where your unique perspective and ideas are acknowledged and valued. Be a part of a company that empowers you to make a difference that's evident on grocery store shelves and families' tables across North America. Location Description Post Consumer Brands in Battle Creek, Mich., the cereal capital of the U.S., is the company's largest manufacturing plant and home to about 600 team members. When you join the team here, you'll be helping to produce some of the most iconic cereal brands, including Honey Bunches of Oats cereal, PEBBLES cereal, Grape-Nuts and Honeycomb cereal. The Battle Creek plant is also unique as it is home to the original barn where C.W. Post started the Postum cereal company in 1895. The Battle Creek team has deep community roots, supporting the city's Cereal Festival, local elementary schools, and hosting several on-site volunteer events throughout the year. Responsibilities Responsibilities and Accountabilities: Best Practice Implementation. Improvement of Process. Application of new technology and equipment to improve process. Support technical training for Process Operators and provide technical oversight. Provide daily support to sustain current process performance targets for safety, quality, yield, rate and efficiency. Lead efforts to improve current process to achieve planned goals and targets. Support data collection and reporting systems that enable process consistency and process improvement efforts. Support meaningful and accurate data from people and process instrumentation. Identify and recommend new and innovative equipment technologies that support process improvements and projects. Support cost reduction changes related to ingredient, materials and finished product. Lead small capital projects. Coordinate with internal and external resources commercializing new products. Support ongoing efforts to sustain process and product attributes related to finished product taste. Provide engineering support for safety improvements. Requirements: Understanding of Lean Manufacturing/Continuous Improvement methodologies. Must have strong analytical and business judgment including demonstrated problem-solving and trouble-shooting skills. Ability to influence, mentor and coach to get results through others. Results driven for being the low cost producer and supporting company growth strategies. Have strong bias for action, while proving the ability to inspire others. Convey high level of optimism while setting aggressive targets to teams, finding ways to achieve them. Communicates a compelling vision and inspired sense of purpose. Talks about the possibilities and is optimistic. Creates strong morale and spirit within team. Solves highly complex problems and prioritizes actions in a timely manner. Probes all sources for answers and can quickly sense what will help resolve issues. Establish clear directions, sets stretching objectives. Lays out work in a well-planned and organized manner and brings out the best in people through leveraging their strengths. Speaks candidly and provides constructive feedback in a professional manner. Organizes and manages projects; interacts, supports, facilitates and leads multi-functional work teams; leads teams to consensus; strong negotiation skills. Able to build strong and diverse relationships across the business groups they partner with. Supports and fosters change. Demonstrates a passion for safety. Able to develop and maintain a respectful and safe work environment. Qualifications EDUCATION: 4-year degree in science or engineering. EXPERIENCE: 5 years plus manufacturing related experience in process engineering and/or process development. Experience in the food industry or consumer products is preferred. Post Holdings and Post Consumer Brands provides equal employment opportunities to all employees and applicants for employment without regard to race, color, religion, gender, sexual orientation, national origin, age, disability, genetic information, marital status, status as a covered veteran and any other category protected under applicable federal, state, provincial and local laws.
Post Holdings provides equal employment opportunities to all employees and applicants for employment without regard to race, color, religion, gender, sexual orientation, national origin, age, disability, genetic information, marital status, status as a covered veteran and any other category protected under applicable federal, state, provincial and local laws.
Equal Opportunity Employer/Protected Veterans/Individuals with Disabilities
The contractor will not discharge or in any other manner discriminate against employees or applicants because they have inquired about, discussed, or disclosed their own pay or the pay of another employee or applicant. However, employees who have access to the compensation information of other employees or applicants as a part of their essential job functions cannot disclose the pay of other employees or applicants to individuals who do not otherwise have access to compensation information, unless the disclosure is (a) in response to a formal complaint or charge, (b) in furtherance of an investigation, proceeding, hearing, or action, including an investigation conducted by the employer, or (c) consistent with the contractor's legal duty to furnish information. 41 CFR 60-1.35(c)
Be The First To Know
About the latest Process engineer Jobs in United States !
Manufacturing Process Engineer
Posted 6 days ago
Job Viewed
Job Description
Job Description: Manufacturing Process Engineer
Utilize lean manufacturing principles to drive continuous improvement in productivity, quality, delivery, and cost. Generate process improvement projects and develop project timelines for implementation. Manage quarterly Tactical Implementation Plans for MPI Expert projects, lead kaizen events, and assist with root cause problem-solving activities in all areas. Contribute to the development of 5S, Kanban, and other lean systems. Coach and train others in lean and continuous improvement tools, while reporting metrics related to productivity and using statistical methods to analyze data for problem-solving. Create and modify standard operating procedures, work instructions, and graphical operations sheets.
Responsibilities
-
Utilize lean manufacturing principles to improve productivity, quality, delivery, and cost.
-
Develop and implement process improvement projects.
-
Manage quarterly Tactical Implementation Plans for MPI Expert projects.
-
Lead kaizen events to enhance processes.
-
Assist in root cause problem-solving activities.
-
Develop 5S, Kanban, and other lean systems.
-
Coach and train team members in lean and continuous improvement tools.
-
Report metrics related to productivity and analyze data using statistical methods.
-
Create and modify standard operating procedures and work instructions.
Essential Skills
-
Expertise in manufacturing engineering and process engineering.
-
Proficiency in machining and manufacturing processes.
-
3+ years of experience with lean manufacturing and continuous improvement.
-
Experience in root cause analysis, 5S, Kanban, and other lean systems.
-
Ability to create process flow diagrams, conduct time studies, and develop capability studies and control plans.
Additional Skills & Qualifications
- Bachelor of Science degree highly preferred.
Pay and Benefits
The pay range for this position is $75000.00 - $9000.00/yr.
Three (3)weeks of Paid Time Off annually for newly hired employees13 paid holidays, including floating holidays annuallyAnnual Bonus Program401(k) Savings Plan with company match and safe harbor contributionsMedical, Dental, and Vision Insurance eligibility upon date of hireCompany paid Basic Life Insurance & AD&D, Short-Term Disability Insurance, and Long-Term Disability Insurance (with enhanced buy up option)Optional Life Insurance & AD&D (including Spouse/Child Optional) coverageHealthcare Flexible Spending Account, Dependent Care Flexible Spending and a Health Savings Account (including company contribution) if enrolled in applicable Danfoss Medical PlanPaid Parental Leave and Adoption AssistancePaid Bereavement LeaveMilitary Leave BenefitsTuition Reimbursement ProgramReimbursement for industry/organization membership dues, home office expenses, etc., based on established eligibility criteriaEmployee Assistance ProgramEmployee Job Referral Bonus ProgramVoluntary benefits such as: Pet Insurance, Legal Assistance and Identity and Fraud Protection, Critical Illness Insurance, Accident Insurance and Hospital Indemnity InsuranceAdditional benefits such as virtual physical therapy sessions, fitness membership programs, and day care provider network assistance
Workplace Type
This is a fully onsite position in Freeport,IL.
Application Deadline
This position is anticipated to close on Jul 22, 2025.
About Actalent
Actalent is a global leader in engineering and sciences services and talent solutions. We help visionary companies advance their engineering and science initiatives through access to specialized experts who drive scale, innovation and speed to market. With a network of almost 30,000 consultants and more than 4,500 clients across the U.S., Canada, Asia and Europe, Actalent serves many of the Fortune 500.
The company is an equal opportunity employer and will consider all applications without regard to race, sex, age, color, religion, national origin, veteran status, disability, sexual orientation, gender identity, genetic information or any characteristic protected by law.
If you would like to request a reasonable accommodation, such as the modification or adjustment of the job application process or interviewing due to a disability, please email (% ) for other accommodation options.
Manufacturing Process Engineer
Posted 6 days ago
Job Viewed
Job Description
Introduction to BlueOval SK
At BlueOval SK, we will lead the transformation of the electric vehicle (EV) battery business through partnership (Joint Venture formed by Ford and SK On) to provide products and processes to increase our customers' experience. As the future of BlueOval SK, you will help lead the battery revolution by working alongside our teams as we build the batteries required for electric vehicle business excellence.
Ford and SK On are investing billions in Kentucky and Tennessee including building three state-of-the art battery manufacturing facilities between the two campuses at BlueOval City in Tennessee and BlueOval SK Battery Park in Kentucky. These brand-new advanced manufacturing facilities will use Ford's 100-years of automobile manufacturing expertise and SK On's 30+ years of electric vehicle battery expertise to become the world's best battery manufacturer.
The Manufacturing / Process Engineer at BlueOval SK - BlueOval City in Stanton, Tennessee will have a unique, once-in-a-lifetime opportunity to be a key member of the start-up team, launching the facility from the ground up.
Key Areas of Responsibility:
-
Support Manufacturing Process Engineering activity for Final Assembly
-
Drive continuous improvement in safety, quality and productivity
-
Apply engineering principles and analytical techniques to establish and continuously improve manufacturing processes and products
-
Develop action plans as required to investigate and prioritize quality concerns and verify corrective actions on internal processes and supplier processes
-
Conduct job ergonomic evaluations and deliver corrective actions as required
-
Analyze Cell / Array scrap root causes; engage in mapping and corrective actions to reduce waste
-
Create process and instruction sheets supporting quality methods and processes
-
Deliver capable processes and tools accordingly
-
Lead role in resolving assembly related concerns. Lead variability reduction and lean manufacturing initiatives and best practices
-
Ensure compliance to Plant, Corporate, Governmental and Environmental standards
-
Support ISO 14001 compliance and support internal ISO auditing and compliance as required
-
Identify OEE / throughput constraints and drive root cause improvements
Minimum Requirements:
-
Education: Bachelor's degree
-
Experience: 5+ yrs of related experience
-
Ability to support any shift in a 7-day work pattern
-
Candidate must be flexible to significant travel during initial plant start-up phase
-
Candidate must be willing to work remotely and in-person at temporary facilities as needed during initial plant start-up phase
-
Successful candidate must be able to demonstrate leadership behaviors consisting of outstanding interpersonal, teambuilding, and communication skills
Preferred Requirements:
-
Education: Bachelor's degree in Engineering
-
Experience:
-
Effective oral and written communication skills
-
Lean Manufacturing and Six Sigma experience
-
8D and 5Why corrective action and problem solving skills
-
Lean Tools - 5S, Kanban, Poka-yoke, and Value Stream Mapping
-
TQM and Kaizen Methods
-
FMEA, PPAP, and DOEs experience
-
Visual Factory Management
-
Ergonomic analysis knowledge and experience
About BlueOval SK
At BlueOval SK, we will lead the transformation of the electric vehicle (EV) battery business through partnership (Joint Venture formed by Ford and SK On) to provide products and processes to increase our customers' experience. As the future of BlueOval SK, you will help lead the battery revolution by working alongside our teams as we build the batteries required for electric vehicle business excellence. We have a wide variety of opportunities for you to accelerate your career.
The Opportunity
Ford and SK On are investing billions in Kentucky and Tennessee including building three state-of-the art battery manufacturing facilities between the two campuses at BlueOval City in Tennessee and BlueOval SK Battery Park in Kentucky. These brand-new advanced manufacturing facilities will use Ford's 100-years of automobile manufacturing expertise and SK On's 30+ years of electric vehicle battery expertise to become the world's best battery manufacturer.
For more information about BlueOval SK plans, please Follow this link.
What you'll receive in return:
As part of the BlueOval SK family, you'll enjoy excellent compensation and a comprehensive benefits package that includes generous paid time off (PTO), retirement contributions, incentive compensation and much more. You'll also experience exciting opportunities for professional and personal growth and recognition. If you have what it takes to help us lead the transformation of the EV battery business, we'd love to have you join us.
Benefits Include :
-
401k plan with retirement planning services
-
401k company matching after completing three months of service
-
Medical and prescription drug coverage
-
Dental and vision coverage
-
Preventative Care
-
Eligibility for great ancillary benefits including: Flexible Spending Accounts (FSAs), Short-Term Disability (STD) and Long-Term Disability (LTD), Employee Basic Life and Accidental Death Dismemberment (AD&D) insurance, and Employee Supplemental Life Insurance
-
Access to Paid Time Off (PTO) after completing probationary period and Emergency PTO
-
Parental Leave
-
Access to Ford Vehicle Discount Program
-
Climate-controlled working environment
-
For a full list of benefits, visit our website:
?
Candidates for positions with BlueOval SK must be legally authorized to work in the United States. BlueOval SK does not sponsor employment VISAs for candidates at this time. Verification of employment eligibility will be required at the time of hire.
We are an Equal Opportunity Employer committed to a culturally diverse workforce. All qualified applicants will receive consideration for employment without regard to race, religion, color, age, sex, national origin, sexual orientation, gender identity, disability status or protected veteran status.
Manufacturing Process Engineer
Posted 7 days ago
Job Viewed
Job Description
Our purpose at Avient Corporation is to be an innovator of materials solutions that help our customers succeed, while enabling a sustainable world.
Innovation goes far beyond materials science; it's powered by the passion, creativity, and diverse expertise of 9,000 professionals worldwide. Whether you're a finance wizard, a tech enthusiast, an operational powerhouse, an HR changemaker, or a trailblazer in materials development, you'll find your place at Avient.
Join our global team and help shape the future with sustainable solutions that transform possibilities into realities. Your unique perspective could be the key to our next breakthrough!
Job Summary
This position supports Plant Manufacturing and Technical Operations while maintaining a strong focus on continual Process Improvement and Optimization. Applies fundamental knowledge of basic principles, theories and concepts of industry standards and practices to design, automate, modify, or develop facilities, testing, machines, equipment or processes used in processing or manufacturing products.
Essential Functions
- Develops, designs, and communicates manufacturing processes.
- Monitors and revises processes to help generate cost savings and improve the quality and efficiency of product/process.
- Participates in design reviews to improve the ability to manufacture products.
- Responsible for the activities related to the development of new processes including researching current and emerging technologies, evaluating process cost, quality, and performing process characterization and optimization studies using designed experiments, problem-solving and decision making tools.
- Identifies and solves issues or problems with equipment/process. Troubleshoots possible causes and coordinates the activities of maintenance, production and other available resources to implement cost effective solutions.
- Provides coordination of new process installation and process changes.
- Other projects/duties as assigned.
Competencies
- Personal Skills - Stress Management, Reading/Comprehension, Self Motivated, Time/Priority Management, Work on a Team, Organizational Skills
- Software Skills - Microsoft Outlook, Microsoft Word, Microsoft Excel, SAP
- Leader of Self - Instills Trust, Action Oriented, Collaborates, Customer Focus, Situational Adaptability, Being Resilient, Demonstrates Self-Awareness, Communicates Effectively
Education and Experience
- Bachelors degree required -Mechanical Engineering or Equivalent field
- At least 3 years of Manufacturing - Manufacturing Operations experience required
- Manufacturing - Safety Procedures
- Cross Functional - Process Improvement
Physical Demands
- While performing the duties of this job, the employee is regularly required to stand; use hands to finger, handle, or feel; and reach with hands and arms.
- The employee is frequently required to walk.
- The employee is occasionally required to stoop, kneel, crouch, crawl and talk or hear.
- The employee is occasionally required to lift and/or move up to 50 lbs.
- Specific vision abilities may require close vision, color vision, depth perception, and ability to adjust focus.
- While performing the duties of this job, the employee is occasionally exposed to moving mechanical parts, toxic or caustic chemicals, and fumes or airborne particles.
- The noise level in the work environment ranges from normal office noise levels to loud.
We believe that all of our global employees are leaders and that the six most important behaviors for driving our strategy and culture are the same no matter if an employee is a leader of self, a leader of others, or a leader of the business.
By playing to win, acting customer centric, driving innovation and profitable growth, collaborating seamlessly across Avient, and motivating and inspiring and developing others and yourself you will accelerate your ability to achieve Avient's strategic goals, to meet our customer needs, and to accomplish your career goals.
#LI-AM1